Stillstand führt zu Ineffizienz. Dieses Motto gilt zwar in vielen Branchen – aber nirgends so sehr wie in der Produktion. Technologische Neuerungen wie das Internet of Things (IoT), Big Data und Cloud-Computing haben hier einen tiefgreifenden Wandel in Gang gesetzt, der von der Cybersicherheit bis zur Supply Chain reicht. So gehen beispielsweise aktuelle Schätzungen davon aus, dass die Zahl der vernetzten Dinge bis 2020 auf 30 Milliarden ansteigen wird, wobei das produzierende Gewerbe neben der Energieerzeugung und der Telekommunikation einen der drei Hauptabsatzmärkte darstellt. Mit dem Industrial Internet of Things (IIoT) ist zudem ein ganz eigener Teilbereich des IoT entstanden, der Prozessautomatisierung und Fertigung von Grund auf revolutioniert: Unternehmen können ihre Geschäftsabläufe künftig nicht nur verwalten, sondern in Echtzeit steuern. Denn das IIoT macht es möglich, unterschiedlichste vernetzte Sensoren nahtlos in das Prozesskontrollsystem zu integrieren. Mithilfe der dabei gewonnenen Daten lassen sich zum einen die Produktionsabläufe deutlich effizienter gestalten. Zum anderen können auch andere geschäftskritische Faktoren – wie z.B. Anlagensicherheit, Umweltschutz, Ausfallsicherheit und Rentabilität – direkt auf Anlagenebene gesteuert werden. Damit dies gelingt, müssen Mitarbeiter jedoch in der Lage sein, auf Basis einer Fülle von Produktionsdaten die richtigen Daten zu selektieren, Schlüsse zu ziehen um so fundierte Echtzeit-Entscheidungen zu treffen.
Digitale Kompetenz und technologische Weichenstellungen sind entscheidend
Über Jahrzehnte hinweg setzte das Zusammenspiel von Informationstechnologie und Anlagentechnik der Architektur von Automatisierungssystemen Grenzen. Intelligente Steuerungssysteme, die passgenau auf die Topologie eines Industriebetriebes zugeschnitten sind, ließen sich deshalb nur schwer realisieren. Die Umstellung auf eine vollumfassende Echtzeit-Prozesssteuerung stellte für Unternehmen daher eine enorme Herausforderung dar und schien lange Zeit sogar unmöglich. Blickt man auf die Zukunft der Prozessautomatisierung, so fallen jedoch einige frühere technologische Einschränkungen weg. Einzelne Komponenten wie z.B. intelligente Pumpen und Aktoren sind mittlerweile in der Lage, quasi autonom zu agieren, d.h. sich selbst zu steuern und zu überwachen. Nach dem ‚Bottom-Up-Prinzip‘ werden Industrieautomatisierung und Methoden zur Prozessoptimierung künftig alle Hierarchiestufen des Produktionsverbunds umfassen – von der Maschine über die einzelnen Funktionseinheiten und Produktionsabschnitte bis hin zu ganzen Fertigungsstandorten. Wichtige geschäftskritische Faktoren wie Sicherheit und Zuverlässigkeit können so künftig direkt auf Anlagenebene gesteuert werden. Voraussetzung hierfür ist allerdings, dass der zuständige Asset Manager auch hinreichende Informationen über die jeweilige Prozessdynamik erhält bzw. in die Lage versetzt wird, geschäftskritische Faktoren auch sinnvoll in den Automatisierungsprozess einzubinden. Denn die Produktionsumgebung der Zukunft benötigt Fachpersonal, dessen Aufgabenbereich über die bloße Effizienzkontrolle einzelner Prozesse hinausgehen wird. Zeitgemäße Automatisierungsstrategien müssen daher nicht nur positive menschliche Eigenschaften wie Urteils- und Anpassungsfähigkeit berücksichtigen. Sie sollten die Mitarbeiter darüber hinaus auch aktiver in die zugrundeliegenden Betriebsprozesse einbinden und sie durch geeignete Technologien und Qualifizierungsmaßnahmen zu fundierten Echtzeit-Entscheidungen befähigen. Doch wie lässt sich das konkret umsetzen?
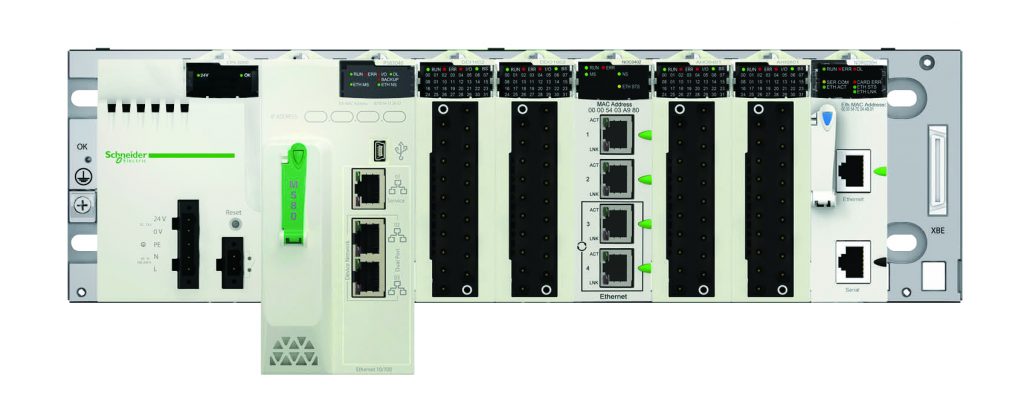
Moderne Visualisierungen und intelligent aufbereitete Daten unterstützen Entscheidungsprozesse
Echtzeit-Entscheidungen im industriellen Umfeld müssen heute zügig und meist auf begrenzter Datengrundlage getroffen werden. Zur Verbesserung von Entscheidungsfindung und Prozessmanagement werden allerdings nicht zwingend mehr, sondern vor allem intelligent aufbereitete und kontextbasierte Daten benötigt. Von entscheidender Bedeutung sind hier ausgefeilte Mensch-Maschine-Schnittstellen (Human Machine Interfaces/HMI). Sollen sie die Interaktion zwischen Mensch und Maschine optimal unterstützen, müssen sie nicht nur den jüngsten Industrietrends gerecht werden (immer komplexere Kontrollsysteme, wachsende Datenmengen, generell höhere Automatisierungsgrade, vermehrter Einsatz von Fernwirksystemen), sondern auch mit Blick auf die Situational Awareness konzipiert sein. Nur so können Bedienfehler auch bei weniger geschulten Mitarbeitern verringert und kritische Situationen identifiziert werden, noch bevor sie einzelne Prozessabläufe beeinträchtigen. Neuere HMIs ermöglichen zudem nicht nur die vereinfachte Darstellung von Produktionsdaten, sondern liefern auch kontextbasierte Informationen zu den jeweiligen Abläufen. Durch optimierte Situational Awareness lassen sich Fehlfunktionen so bereits im Vorfeld bis zu fünfmal schneller identifizieren. Kommt es tatsächlich zu einem kritischen Ereignis, können verbesserte Navigationssysteme die Reaktionszeit der Mitarbeiter um mehr als vierzig Prozent senken. Angepasste HMI-Designs mit integrierter Situational Awareness können somit nicht nur ausfallzeitbedingte wirtschaftliche Verluste reduzieren, sondern optimieren auch Prozesssicherheit und Durchlaufleistung sowie die allgemeine Anlagen- bzw. Geschäftsperformance. Moderne Dashboard-Designs, die bei der Darstellung von Alarmsignalen standardisierte Stile, Farben und Schriftarten verwenden, sorgen außerdem für eine verbesserte Arbeitseffizienz und mehr Sicherheit.
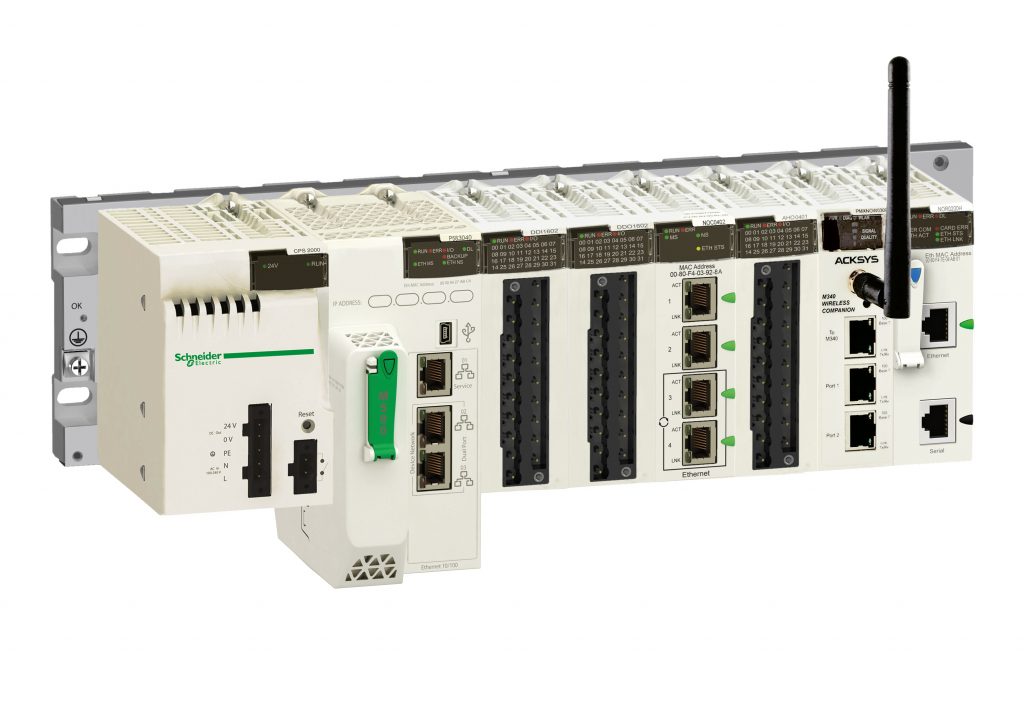
Produktionsausfälle vermeiden
Auch vorausschauende Instandhaltung und Decision-Support-Plattformen eröffnen Produktionsleitern neue Möglichkeiten zur Kontrolle von Betriebskosten sowie zur Steigerung von organisatorischer Effizienz und Durchlaufleistung. Denn im Schnitt verursacht ein unvorhergesehener Shutdown oder Slowdown jährlich 6,2 Tage Produktionsausfall, was ganz erhebliche finanzielle Schäden zur Folge haben kann. Leistungsfähige Tools zur vorausschauenden Instandhaltung können dieses Ausfallrisiko reduzieren, indem sie frühzeitig Aufschluss über den Anlagen-Output sowie über Abweichungen in den Soll-Betriebsabläufen geben. Die Einführungskosten für solche Softwaretools amortisieren sich aufgrund der verringerten Ausfallzeiten bereits innerhalb von drei Monaten. Eine weitere Maßnahme zur besseren Einbindung personeller Ressourcen sind Ethernet-fähige Process Automation Controller (ePACs). Diese Controller wurden eigens für das IIoT entwickelt. Sie verfügen über eine größere Verarbeitungs- und Speicherkapazität, bieten höhere Redundanzlevel und unterstützen alle gängigen I/O-Schnittstellen. Dieses Plus an Leistung und Vernetzung macht laufende Prozesse transparenter und beschleunigt somit die Entscheidungsabläufe. ePACs verringern darüber hinaus die Time-to-Market nachweislich und können den Energieverbrauch im Produktionsverbund um bis zu 30 Prozent senken.