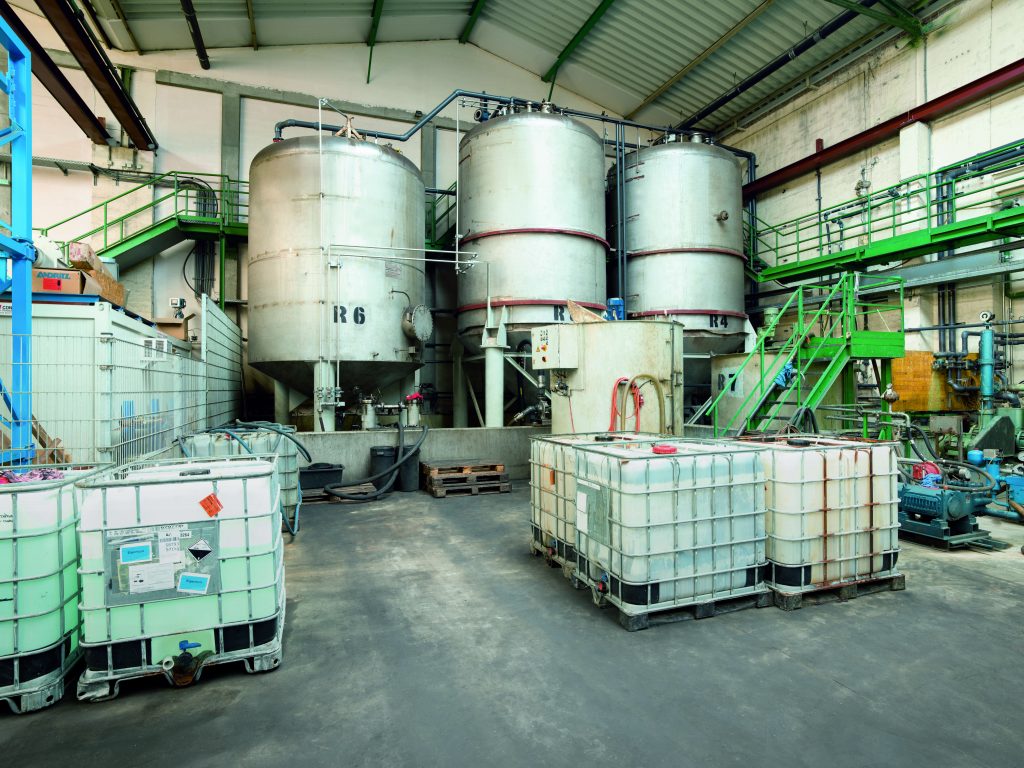
Die 1989 in Wien gegründete AVR GmbH gehört zu den führenden Abfallsammlern und -behandlern Österreichs. In ihren Anlagen werden jährlich zwischen 25.000 und 30.000 Tonnen gefährliche flüssige industrielle Abfälle verarbeitet, die im Hinblick auf die Schonung der Umwelt über die gesetzlich vorgeschriebenen Richtlinien hinaus zur Wiederverwendung aufbereitet oder gewissenhaft entsorgt werden. Das Unternehmen, das mittlerweile 28 Mitarbeiter beschäftigt und einen Umsatz von über fünf Millionen Euro erzielt, kümmert sich dabei um gefährliche Abfälle aller Art. Sein Spezialgebiet liegt allerdings in der Rückgewinnung von Stoffen aus flüssigen Abfällen. In der dazu erforderlichen chemisch-physikalischen Anlage werden unter anderem Säuren und Säuregemische, metallsalzhaltige Konzentrate, Emulsionen und Öl-/Wassergemische gespalten, abgetrennt und neutralisiert. Im Vergleich zu alternativen chemisch-physikalischen Anlagen substituiert die AVR GmbH die notwendigen Neuchemikalien jedoch, indem die bei den Kunden zu entsorgenden Materialien zur Behandlung anderer Abfälle eingesetzt werden. Daraus ergibt sich nicht nur eine Kostenersparnis für die Kunden, sondern auch ein geringerer Neuchemikalien-Verbrauch sowie eine Minimierung der anfallenden Schlammmengen. Darüber hinaus hat die AVR GmbH ein eigenes Verfahren entwickelt, um Öle aus Emulsionen – beispielsweise verwendete Kühlschmierstoffe für Dreh-, Fräs- und Bohrmaschinen – für eine erneute Raffinierung zu nutzen und nicht lediglich als Alternativbrennstoff einzusetzen. Dieser Ansatz ist in Österreich einzigartig und spiegelt den Anspruch des Unternehmens wieder, ökologisch sinnvoll, rechtskonform und zum wirtschaftlichen Nutzen seiner Kunden zu handeln.
Separate Weiterverarbeitung der Stoffe
Beim Recycling-Prozess von Emulsionen sehen sich die Abfallbehandler mit der Herausforderung konfrontiert, dass als Endprodukt möglichst reines Öl entstehen soll. Bestenfalls enthält das Öl nach den Reinigungsprozessen kaum Wasser (weniger als drei Prozent) und keine Mischfettsäuren mehr. Damit dies der Fall ist, wird die angelieferte Emulsion im ersten Schritt in große Tanks gepumpt. Da jede Lieferung unterschiedliche Eigenschaften aufweist, analysieren die AVR-Mitarbeiter eine Probe der Flüssigkeit im Labor. So lassen sich die geeigneten Trennstoffe feststellen, die dem vollen Tank danach zugegeben werden. Nach einer Weile trennt sich das Öl vom Wasser. Der ölige Anteil steigt aufgrund der geringeren Dichte in den oberen Teil des Tanks auf. Gleichzeitig sinkt das Wasser auf den Tankboden ab. Der Aufbau im Bild auf Seite 46 oben verdeutlicht den beschriebenen Abscheidungsprozess: Im linken Laborgerät befindet sich die angelieferte Emulsion. Nach der Zugabe der Trennstoffe ist rund 20 Minuten später im mittleren Behälter eine Reaktion sichtbar. Wartet das Laborpersonal ein wenig länger, hat sich das Öl im rechten Laborgerät fast vollständig vom Wasser getrennt. Öl und Wasser werden anschließend separat weiterverarbeitet, sodass die beiden Substanzen einzeln aus dem Tank herauszupumpen sind.
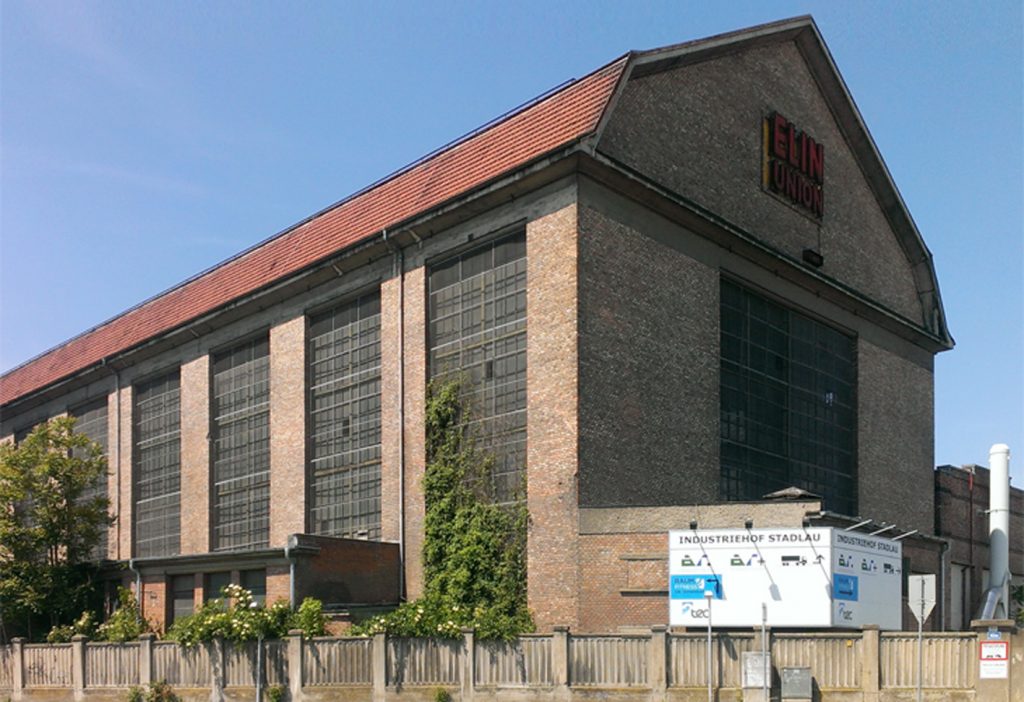
Änderung der Wirkleistung als Indikator
Zunächst war in der chemisch-physikalischen Anlage kein Sensor verbaut, der den Übergang von Wasser zu Öl hätte erkennen können. Die Pumpe wurde durch eine dafür abgestellte Fachkraft abgeschaltet. Zu diesem Zweck musste der Mitarbeiter das Ablaufrohr kontinuierlich visuell überprüfen und regelmäßig Proben entnehmen, um den Übergang von der Wasser- in die Ölschicht zu kontrollieren. Mit dieser Tätigkeit war die Fachkraft drei bis vier Stunden täglich beschäftigt. Die elektronischen Motormanager (EMM) von Phoenix Contact sind in der Lage, die Viskositätsänderung in der Übergangsphase von Wasser zu Öl zu detektieren. Sie messen die Wirkleistung von Motoren und überwachen sie auf Über- und Unterlast, Funktion, Verschmutzung und Verschleiß. Dazu werden frei parametrierbare Schalt- und Meldeschwellen verwendet. Die Schwellen für beide Drehrichtungen lassen sich identisch oder separat einstellen. Zur Parametrierung wird die aufgenommene Wirkleistung herangezogen, die sich aus den drei Größen Strom, Spannung und Phasenwinkel ergibt. Unabhängig von Spannungsschwankungen und der Belastung der Antriebsmaschine bietet die Wirkleistung eine wesentlich präzisere Grundlage als eine reine Strombetrachtung. Während ein cos -Wächter lediglich Unterlastzustände und ein Motorschutzrelais nur Überlastzustände erfasst, werden mit der Wirkleistungsmessung alle kritischen Lastzustände des Motors sowie Wirkleistungsänderungen festgestellt. Die Änderung der Wirkleistung nutzt AVR für die Trennung von Wasser und Öl.
Motor wird zum Sensor
Beim elektronischen Motormanager EMM handelt es sich somit um ein Messgerät, bei dem der Motor zum Sensor wird. Aufgrund der exakten Wirkleistungsmessung verfügt der Motormanager über eine so hohe Genauigkeit, dass er selbst Viskositätsänderungen wahrnimmt. Andere, deutlich aufwändigere Sensoren – wie ein Coriolis-Massendurchflussmesser oder Trennschicht-Sensoren – haben in der chemisch-physikalischen Anlage nicht funktioniert, weil sie den Wasser- nicht sauber vom Ölanteil trennen konnten. Darüber hinaus wären derartige Lösungen sowohl in der Anschaffung als auch der Implementierung erheblich teurer gewesen. Im Gegensatz dazu arbeitet der elektronische Motormanager EMM einwandfrei und zeichnet sich zudem durch niedrige Investitionskosten aus. Denn neben dem geringen Preis der Geräte erhält der Anwender eine kostenfreie Software, sodass keine zusätzliche Steuerung angeschafft werden muss. Wegen des integrierten Motorschutzes und der Diagnosefunktion kann ferner auf weitere Bauteile verzichtet werden. Die größte Kostenersparnis ergibt sich jedoch aus der Automatisierung der Aufgabenstellung. „Durch den Einsatz des elektronischen Motormanagers reduzieren sich unsere Kosten monatlich um etwa 1300 Euro“, berichtet Tobias Olbrich, Geschäftsleiter und abfallrechtlicher Geschäftsführer der AVR GmbH. „Daher haben wir nicht lange überlegt und uns für das Gerät entschieden, das nicht nur wirtschaftlich, sondern ebenfalls einfach handhabbar ist und außerdem zuverlässig funktioniert.“