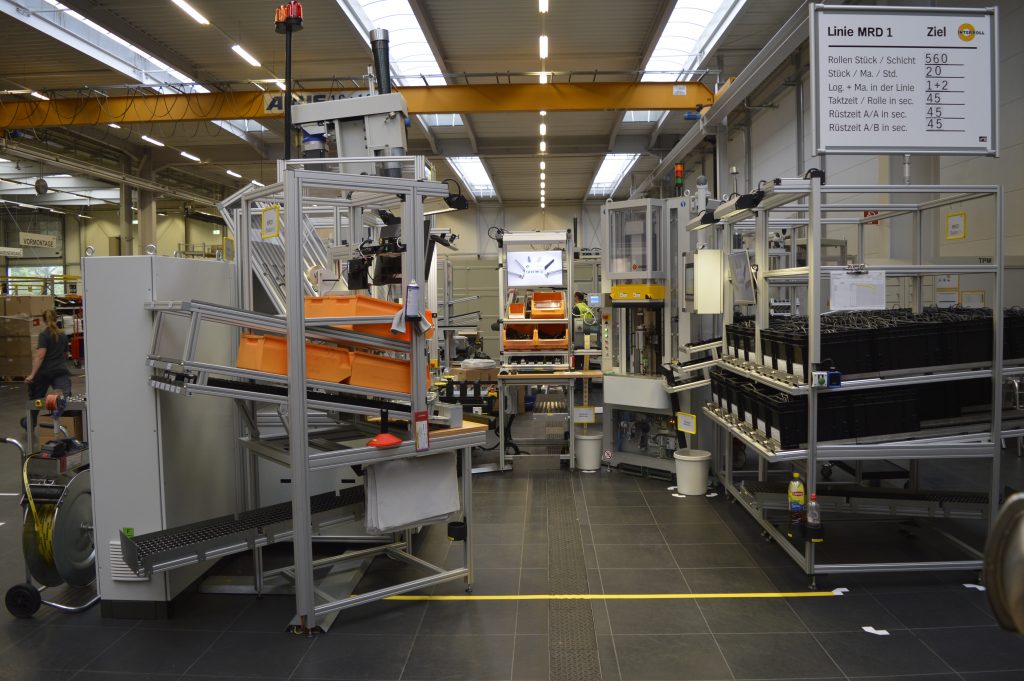
Interroll ist Anbieter von Lösungen für den Materialfluss. Ursprünglich war das Unternehmen mit Spurrollen gestartet, hat dann aber die ersten kunststoffgelagerten Rollen auf den Markt gebracht – also die Produktgruppe, für die es auch heute noch bekannt ist. Gegründet wurde Interroll 1959 in Wermelskirchen, doch schon in den 60er Jahren wurden erste Tochterunternehmen im Ausland gegründet. Heute gibt es weltweit 32 Standorte, die rund 28.000 Kunden versorgen. Weil das Angebot sehr vielseitig ist – es reicht von einzelnen Antriebskomponenten bis zu kompletten Förderanlagen – ist das Unternehmen nach sogenannten Center of Excellences aufgeteilt. Am heutigen Stammsitz in der Schweiz findet sich so z.B. das Exzellenzzentrum für Polymere. Weitere gibt es für Trommelmotoren, Fließlager, Rollen und Förder- und Sortieranlagen.
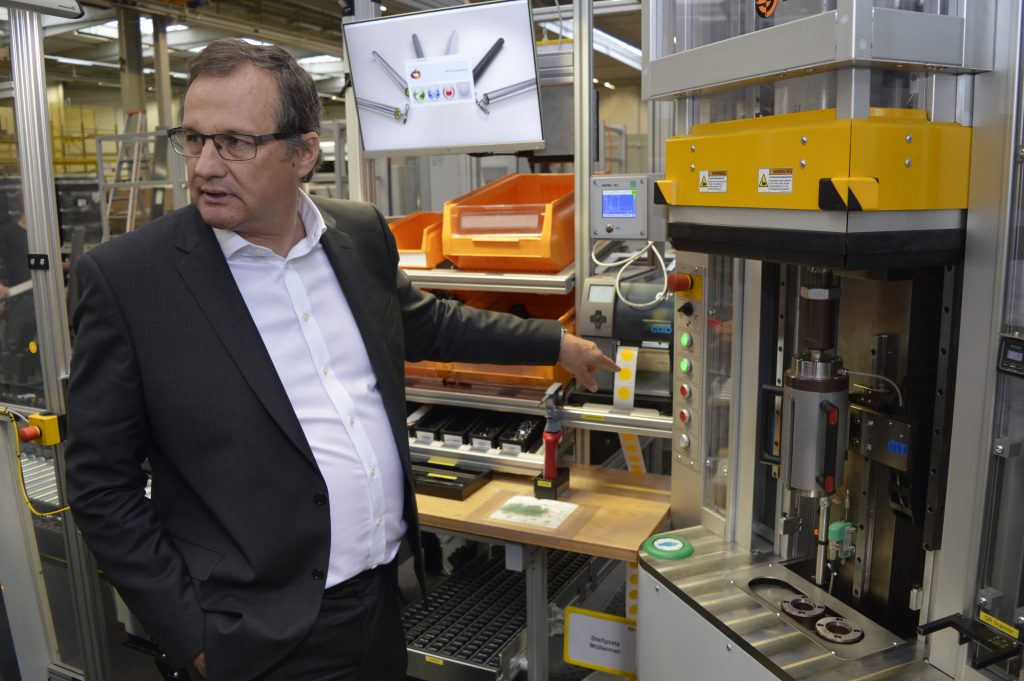
Kompetenzzentrum für Motorantriebe
Das Kompetenzzentrum für Förderrollen sowie die rollenintegrierten Antriebe der RollerDrive-Familie bildet seit Ende der 1990er-Jahre der Gründungsstandort im Bergischen Land. Hier wurde als erste elektronisch kommutierte Motorrolle auf dem Markt auch die Baureihe EC300 entwickelt, die sehr erfolgreich vertrieben wurde. „Die Nachfolgegeneration EC310 ist bis heute erhältlich, mit der Baureihe EC5000 wurde zur diesjährigen Logimat aber wiederum deren Ablöse eingeleitet“, erklärt Daniel Heinen, der als Produktmanager für dieses Segment verantwortlich ist. „Um neuen technischen Entwicklungen sowie dem Lösungsgedanken Rechnung zu tragen, haben wir parallel zu den neuen Antriebsrollen ein komplettes System aus einen Guss auf den Markt gebracht: die DC Plattform, die auch Steuerungen und Netzteile umfasst.“ So ziele man darauf ab, ein komplett aufeinander abgestimmtes Paket für Förderanwendungen aus einer Hand zu liefern. „Durch die Vernetzung der EC5000-Antriebe und der Multicontrol-Steuerung per Feldbus kann der Kunde die Fördertechnik künftig durchgängig in seine Automatisierungslösung integrieren.“

Weltweit einheitliche Fertigung
Eine neue Antriebsgeneration setzt natürlich auch eine neue Produktions- und Montagelinie voraus. „Als Center of Excellence sind wir nicht nur für die Entwicklung der RollerDrive verantwortlich, sondern auch für die Produktionsstandards und die Montageprozesse“, betont Armin Lindholm, Geschäftsführer am Standort Wermelskirchen. „Und weil die Motorrollen der neuen EC5000-Serie nicht nur in Deutschland, sondern auch im US-amerikanischen Wilmington sowie im chinesischen Suzhou gebaut werden, versorgen wir diese Produktionsstandorte von hier aus ebenfalls mit neuen Montageanlagen.“ Durch komplett identische Produktionsprozesse will der Hersteller weltweit eine einheitliche Qualität seiner Antriebe sowie kurze Lieferzeiten sicherstellen. Die Serienproduktion der neuen Antriebsbaureihe wurde unmittelbar nach der Vorstellung auf der Logimat 2019 in Wermelskirchen initiiert. „Um die RollerDrive lokal vor Ort für die jeweiligen Märkte zu produzieren, wurden zwei weitere Produktionslinien aufgebaut und in Betrieb genommen“, so Lindholm, „die wir anschließend an unsere Standorte in den USA und China schicken.“
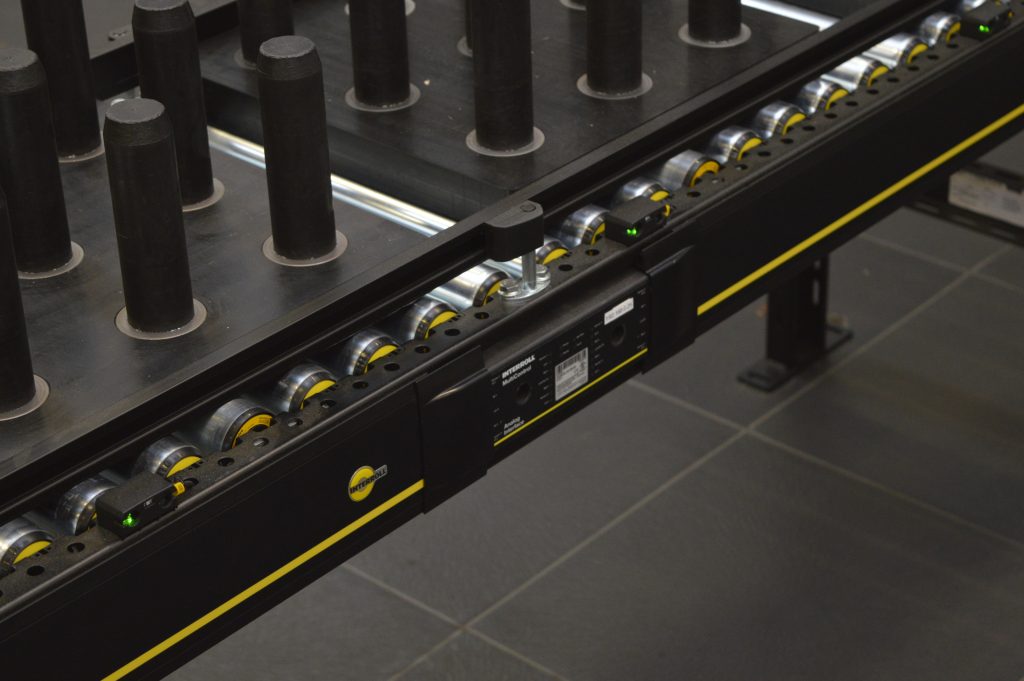
Montage in Wermelskirchen
Wermelskirchen ist nicht nur der älteste Standort der Unternehmensgruppe, sondern auch der umsatzstärkste. Entsprechend wurde er mehrmals erweitert, zuletzt im Rahmen der neuen DC-Plattform. „Wir haben extra eine neue Prüfhalle gebaut, in der die DC-Plattform im großen Stil getestet wird bzw. schon bereits während der Entwicklung getestet wurde“, sagt Heinen. „Produziert wird auf einer Fläche von 9.000m². Im vergangenen Jahr waren es über 8 Millionen Förderrollen, aufgeteilt auf 60.000 Varianten und 120.000 Auftragspositionen.“ Bei den jährlich gefertigten 300.000 Antriebsrollen sei die Varianz ähnlich. „Wir fertigen viele Rollen und Antriebe also nur ein einziges Mal in der geforderten Variante“, ergänzt Lindholm, „was, kombiniert mit unserem Anspruch, den Kunden innerhalb von drei bis fünf Tagen zu bedienen, ein sehr ausgefeiltes Produktionskonzept voraussetzt.“ In der Folge sind die Anlagen darauf ausgelegt, jede Variante einmal pro Schicht bauen zu können. „Das passiert in der Praxis nicht, zeigt aber, wie schnell wir die Maschinen umrüsten können – aktuell in etwa 80 Sekunden“, fährt der Geschäftsführer fort. Insgesamt kommt die Produktion pro Jahr auf die stolze Zahl von rund 600.000 Umrüstungen.

Fertigung mit Kaizen und Kanban
Die Fertigung am Standort Wermelskirchen folgt dem konzernweiten Interoll-Produktionssystem (IPS) und nutzt Toyota-Konzepte von Kaizen, Kanban oder der Lean Production. Die Produktion ist in Zellen organisiert und 95 Prozent der Rollen bzw. Antriebe werden im Single Piece Flow produziert. Es gibt also kaum Fertigteile im Bestand oder im Halbfertigbestand. Obwohl Interroll mit diesem Ansatz sehr erfolgreich gefahren ist und das Fertigungskonzept über die Jahre konsequent weiterentwickelt hat, zeigte sich, dass das Unternehmen vor dem Hintergrund der Smart Factory noch weiter gehen muss. „Aber wo ansetzen? Wo bringt die Digitalisierung den stärksten Hebel“, fragte sich Lindholm. „Die Umrüstzeiten hatten wir ja schon dermaßen optimiert, dass hier nur noch Zehntelsekunden zu holen gewesen wären.“ Größeres Potenzial fand sich beim Informationsfluss der Aufträge, die bislang immer noch als klassische Papierausdrucke in der Produktion ankamen. Deswegen nutzt der Geschäftsführer jetzt vermehrt die Möglichkeiten der Digitalisierung, um manuellen Tätigkeiten und papierbasierte Prozesse im Auftragswesen zu eliminieren. Dahingehend sind auch die neuen Produktionslinien für die DC-Plattform konzipiert: Die Maschinen werden künftig automatisch auf den jeweiligen Auftrag umgerüstet. Die entsprechenden Informationen für die Mitarbeiter werden über Bildschirme direkt an den Arbeitsstationen visualisiert. „Auftragszettel und Charts auszuhängen gehört dann der Vergangenheit an“, so Lindholm. Interroll will mittelfristig auch die klassischen Kanban-Karten durch elektronische Pendants bzw. moderne Informationsmedien ersetzen. „Parallel werden wir noch mehr Sensorik und Intelligenz in die Anlagen hineinbringen“, führt Lindholm weiter aus. „Insgesamt heben wir unsere Kaizen-Philosophie mithilfe der Digitalisierung auf das nächste Level.“

Zellenanbindung ans ERP
Die neue RollerDrive-Linie ist als U-förmige Fertigungszelle konzipiert. Die Mitarbeiter beginnen mit der Montage auf einer Seite und werden über ein Pick-by-Light-System durch das U und den kompletten Workflow geführt. Die jeweils benötigten Montagedaten kommen direkt aus dem ERP-System in die Linie. Parallel werden dem Montageplatz auch die passenden Motoren und Getriebe zugeführt. Vor Ort werden deren Seriennummern ausgelesen und zu einer neuen verheiratet. Anschließend wird die Antriebseinheit im Rohrzylinder verbaut und kommt in die Teststation. Dort durchlaufen die Rollenantriebe eine Prüfung, die mit allen Daten und Parametern auf den entsprechend konfigurierten Antrieb abgestimmt ist. Die Montage- und Prüfdaten jedes Antriebs werden digital über die Azure Cloud wieder zurück ins ERP-System gespielt und dort gespeichert – ganz im Sinne des digitalen Zwillings. „Gesteuert aus dem ERP-System können wir so zigtausend Varianten unserer RollerDrives auf einer Linie produzieren“, unterstreicht Produktmanager Heinen. „Egal welche Länge, ob 24 oder 48V, ob mit oder ohne Feldbus-Schnittstelle – sogar konische und zylindrische Rollen entstehen an einer Station.“
Mensch oder Maschine?
„Ergänzend zu den großen baugleichen Montagelinien in Deutschland, den USA und China wollen wir mittelfristig auch lokale Ausbaustufen für die Produktion der RollerDrives realisieren, allerdings mit kleineren Montageeinheiten – z.B. in Brasilien, Thailand oder Australien“, blickt Lindholm voraus. Doch wie sieht es mit weiteren Automatisierungsmaßnahmen aus? Ist es das Ziel, die Motorrollen irgendwann vollautomatisiert und ohne Zutun von Mitarbeitern zu produzieren? „Bei der Automatisierung von Prozessen müssen immer Effizienz- und Qualitätsgewinne oder Kostenvorteile das Ziel sein“, ist sich Lindholm sicher. „Automatisieren um des Automatisierens Willen halte ich hingegen für fatal.“ Denn die Automatisierung eines Prozessschritts sei nicht nur in vielen Fällen teurer als der Montagemitarbeiter. „Heute können Menschen bestimmte Teile der RollerDrive-Antriebe nach wie vor schneller bzw. besser verbauen als z.B. Roboter.“ Die Produktion der Motorrollen bei Interroll erfolgt also bis auf weiteres im Zusammenspiel von Mensch und Maschine. (mby)