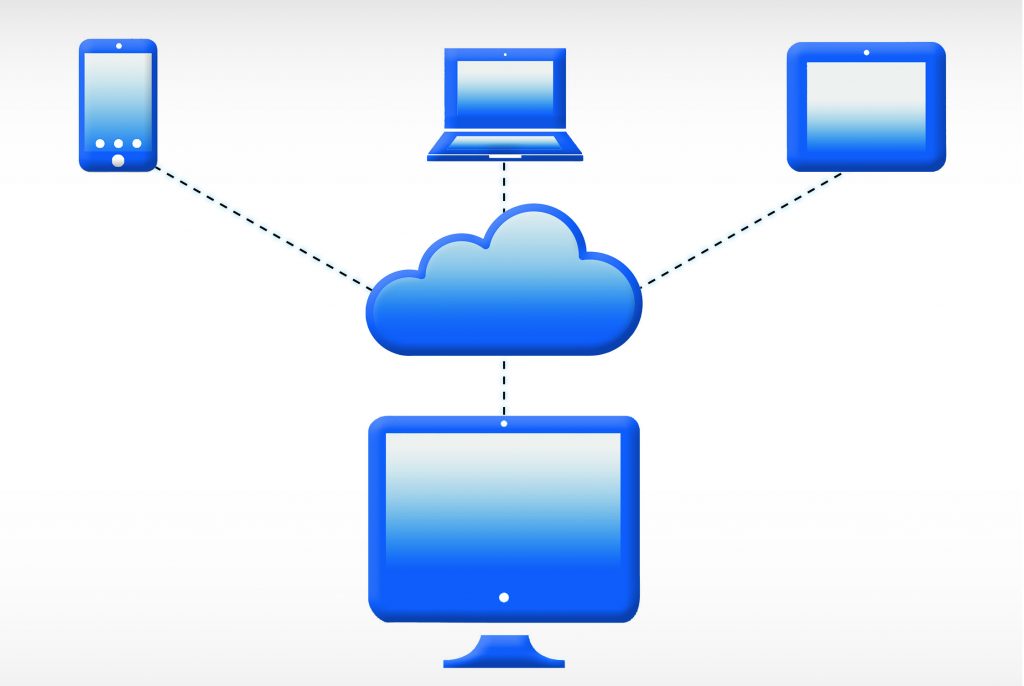
Die Automatisierungstechnik hat sich in den vergangenen Jahren stürmisch entwickelt. Leistungsfähigere Steuerungstechnik und Industrie-PCs konnten auf IP-gestützten Netzwerken mehr Sensordaten empfangen und verarbeiten und damit zusätzliche Automatisierungsaufgaben übernehmen. Der Software-Anteil an der Wertschöpfung im Maschinen- und Anlagenbau ist steil angestiegen, denn Mechanik wird -wo immer möglich- von Elektronik ersetzt. Inzwischen ist ein Punkt erreicht, an dem sich für viele die Frage stellt: Lohnen sich die Investitionen in Industrie 4.0? Kann man durch Produktivitätsgewinne tatsächlich die Kosten für modernere Vernetzung, mehr Sensorik, intelligente Steuerungen und Cloud-fähige Antriebe hereinholen und die OEE verbessern? Oft genug wird diese Rechnung angezweifelt – denn nach den bisherigen Maßstäben geht sie nicht auf.
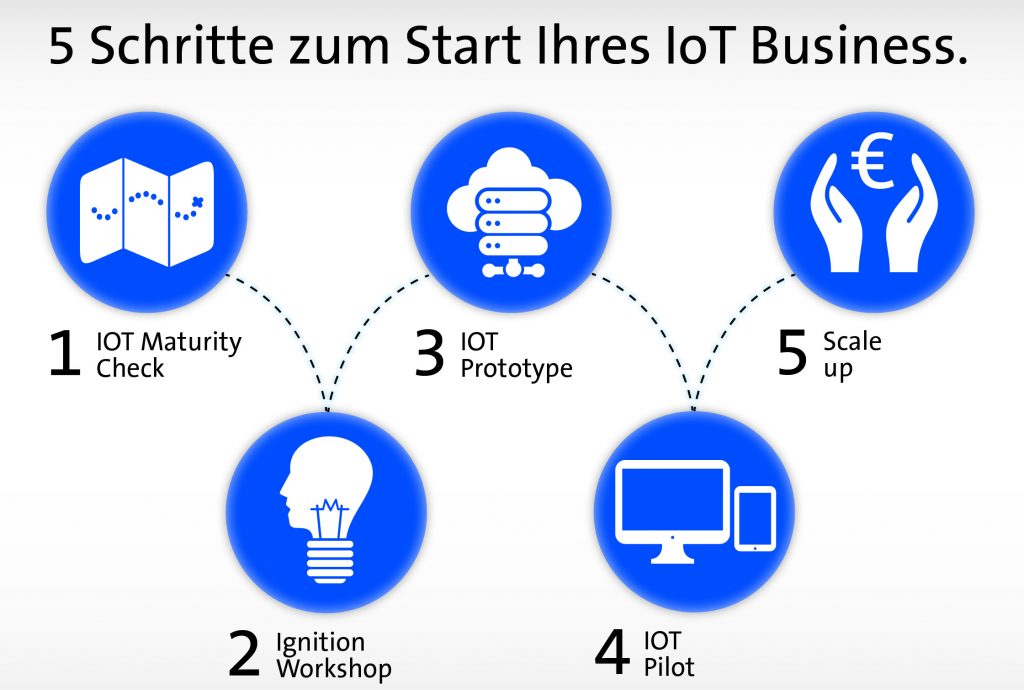
Qualitätssprung
Tatsächlich aber geht es nun nicht mehr darum, hier und da ein bisschen Strom, ein bisschen Arbeitskraft einzusparen und dort einen kleinen Qualitätsfortschritt zu erzielen. Wenn OT und IT zusammenwachsen, ergibt sich ein qualitativer Sprung in der Entwicklung der Produktionstechnik, mit dem auch ein sprunghafter Anstieg in der Produktivität erzielt werden kann. Edgar Schüber, Managing Director bei der Lenze-Tochter logicline, weiß um die Unsicherheit bei diesem Thema: „Jeder spricht darüber. Aber kaum jemand weiß, was zu tun ist, um diese Vorteile zu realisieren. Denn Industrie 4.0 oder Predictive Maintenance gibt es nicht als Komponente zu kaufen.“ Seine Antwort lautet: der OEM bietet nicht die Hardware mit bestimmten Funktionen an, sondern den Produktivitätsfortschritt quasi als Produkt – lässt sich also vom Anlagenbetreiber letztlich für den Service bezahlen, der seinem Kunden trotzdem Geld spart.
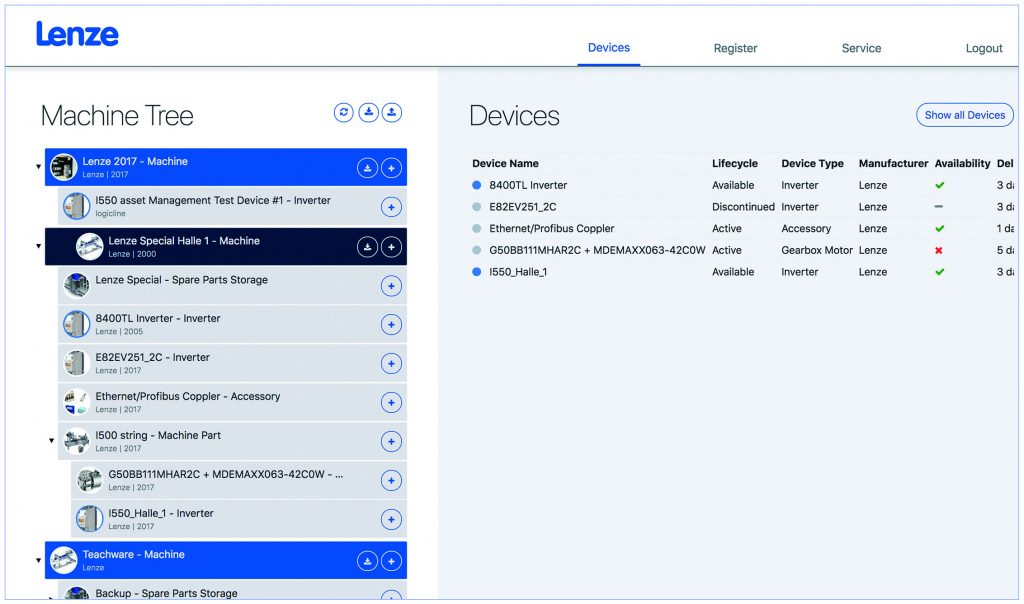
Connectivity an erster Stelle
Für dieses Geschäftsmodell bedarf es allerdings einiger Voraussetzungen auf Seiten der Infrastruktur. Nimmt man alles zusammen, scheint die Aufgabe riesig zu sein: „Schaffen Sie eine intelligente Fabrik.“ Dies lässt sich jedoch auf einzelne Schritte herunterbrechen, die durchaus zu bewältigen sind. Eine der Grundlagen für die vorausschauende Wartung ist die durchgehende Vernetzung aller wesentlicher Komponenten – also der Start in das Zeitalter des Industrial Internet of Things (IIoT): Connectivity auf Basis von IP-Netzen in der Fertigung, Intelligenz vor Ort, die in der Lage ist, Daten vorzuverarbeiten und zu konsolidieren, kombiniert mit Cloud Services, in denen Daten langfristig gesammelt und mittels Big-Data-Methoden analysiert werden können. „Ein erster Nebeneffekt an dieser Stelle: Sie schaffen zugleich die Voraussetzung für Ferndiagnose und Remote-Services“, erläutert Schüber – damit sei bereits ein erster Schritt Richtung höherer Produktivität und besserer Services getan. Über die lückenlose Protokollierung der Maschinendaten wird zudem ein Benchmarking auch über Standorte hinweg möglich.
Single Point of Truth
Der zweite Schritt auf dem Weg zur Smart Factory ist, dass die entstehenden IT-Systeme, in denen die Daten vorgehalten werden, mit Schnittstellen versehen und integriert werden. Dabei gilt es auch, einen zentralen Punkt zu schaffen, der alle verfügbaren Daten versammelt. Der Logicline-Geschäftsführer betont: „Die Daten dieser Instanz müssen verlässlich, sprich von hoher Qualität und Aktualität und mit der richtigen Bedeutung versehen sein.“ Dies ist eine Aufgabe für Datenanalysten, die in der Lage sind, aus den vorhandenen Daten die richtigen Schlüsse zu ziehen. Solche Experten sind auf dem Markt oft nur schwer zu finden. Hier können Lenze-Partner auf die Unterstützung ihres Lieferanten und seiner Digitalisierungstöchter zurückgreifen. Lenze und die Digitalisierungs-Tochter logicline haben bereits eine Asset-Management-Applikation entwickelt, die eben jene zentrale Dateninstanz darstellt. Durch eine Bestandsaufnahme der gesamten Maschine werden alle relevanten Komponenten der Maschine (‚Assets‘) mit Seriennummer, Gerätekennzeichnung, Einbaulagen-Fotos und Funktionsbereich in der Lenze-Asset-Management-Software vor Ort aufgenommen. Dieser Datenstamm wird angereichert mit Informationen wie z.B. Lieferzeiten und Verfügbarkeit Wartungsintervallen, dem Lebenszyklus der Komponente sowie Dokumentationen wie Bedienungsanleitungen und vielem mehr. Dadurch entsteht ein digitales Profil der Maschine, das als Basis für verschiedene Servicepakete dienen kann – eines davon ist Predictive Maintenance. „Das Entscheidende ist, dass die Anwendung die komplette bestehende Infrastruktur mit Komponenten unterschiedlicher Hersteller – das Brownfield – erfassen kann und hier einen Single Point of Truth darstellt“, so Edgar Schüber. Der Datenstamm der Applikation dient zugleich der Visualisierung und der Analytik, die dem Predictive Maintenance zugrunde liegt. So kann es keine widersprüchlichen Informationen geben.