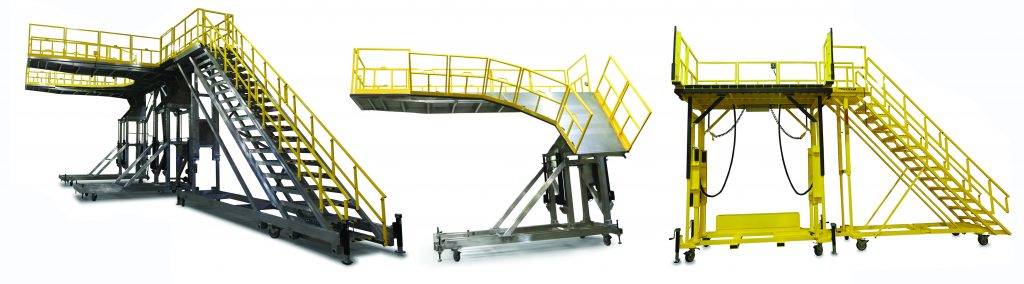
Das US-amerikanische Unternehmen Spika beliefert als Anbieter von Arbeitsbühnen unter anderem die Automobil- und die Luftfahrtindustrie mit entsprechenden Plattformen. „Die Sicherheitsbeauftragten unserer Kunden verlangen eine bestmögliche Einhaltung sämtlicher Arbeitsschutz- und Sicherheitsvorschriften“, erklärt Jeff Ruffner, Direktor Geschäftsentwicklung bei Spika. Zudem sei auch große Flexibilität und Höhenverstellbarkeit gefragt. „Erschwerend kommt hinzu, dass unsere Kunden gleichzeitig maßgeschneiderte, kostengünstige Lösungen mit immer kürzeren Lieferzeiten verlangen.“ Ein Schlüssel für diese Anforderungen liegt für das Unternehmen in der Wahl elektromechanischer Linearaktuatoren zum Heben und Senken der Arbeitsbühnen sowie der zugehörigen höhenverstellbaren Zugangstreppen.
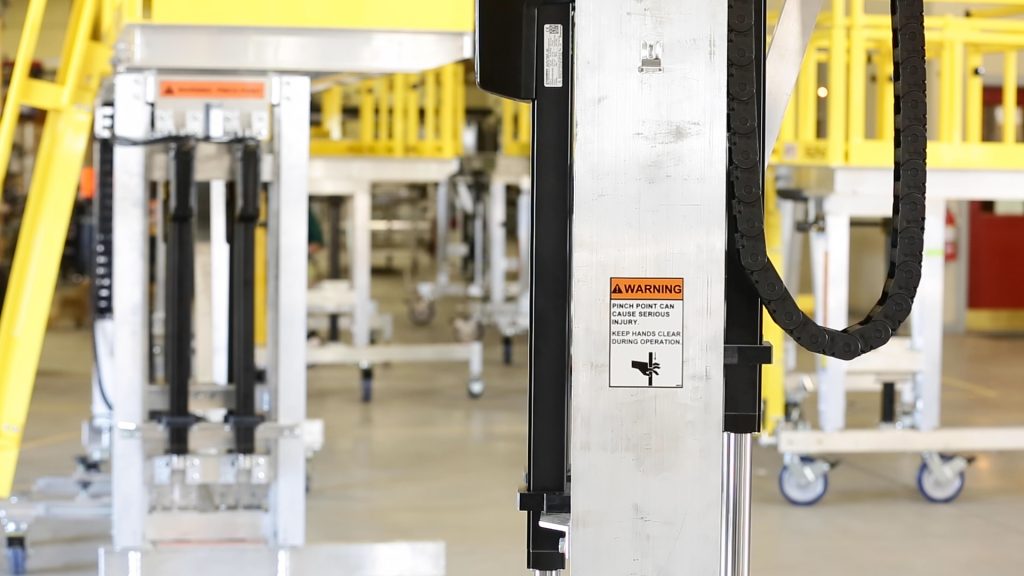
Alternativen gesucht
Die meisten Arbeitsbühnen von Spika sind 1m breit und 3 bis 5m lang. Angesichts dieser Maße ist es bezogen auf die Sicherheit und die Produktivität wichtig, die Bühne jederzeit in Waage zu halten. Vor dem Einsatz von Aktuatoren wurde die Höhenverstellbarkeit mit Hilfe manueller Spindelhubgetriebe realisiert. Hierzu wurde die Arbeitsbühne zunächst an einer Seite bis zur gewünschten Höhe angehoben, dann wurde die Spindel auf der anderen Seite solange gedreht, bis die Bühne austariert war. Dieser ineffiziente Prozess gab den Ausschlag, nach alternativen Lösungen zu suchen. „Wir probierten motor- und manuell per Kette betätigte Kugelgewindetriebe, aber diese erwiesen sich als zu umständlich“, erzählt Tom Spika, Unternehmensgründer und CEO. „Auch die in der Hebetechnik verbreiteten hydraulischen Systeme haben wir in Erwägung gezogen, stießen hier aber ebenfalls auf erhebliche Nachteile.“ Hierzu gehörten die Gefahr austretender Hydraulikflüssigkeit, ein schleichendes Absinken und die fehlende Möglichkeit, das System in Waage zu halten. Deshalb kristallisierten sich elektromechanische Aktuatoren als die für das Unternehmen wirtschaftlichste und effektivste Lösung heraus.
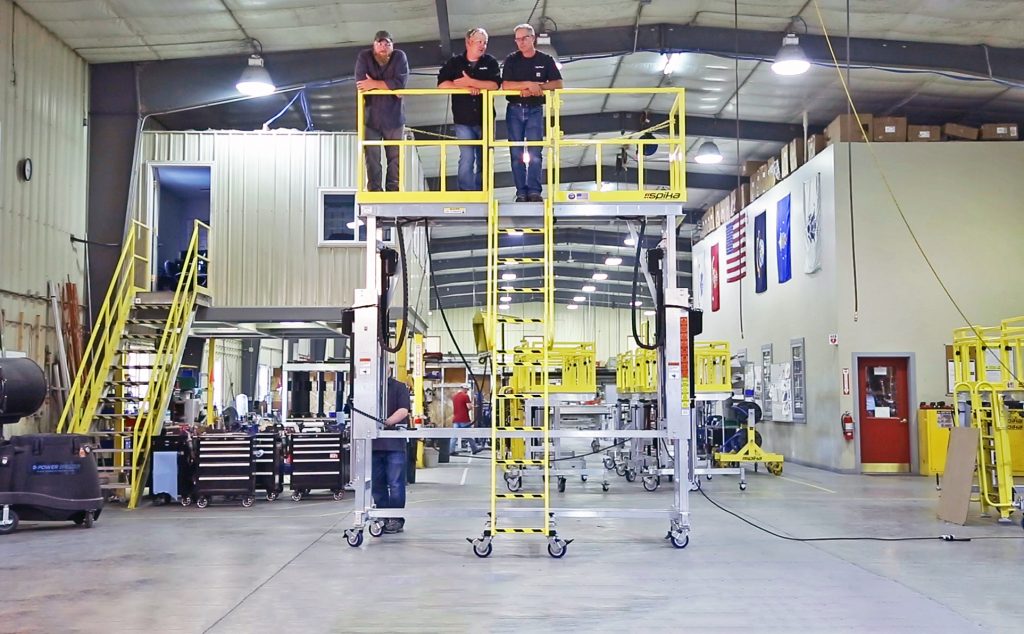
Aufgaben für Aktuatoren
Eine typische elektromechanische Konfiguration besteht aus vier Aktuatoren an einem Bühnensegment für eine Höhenverstellbarkeit von bis zu einem Meter, eine weitere aus zwei Aktuatoren an jeder Ecke, mit denen die Höhe um bis zu knapp zwei Metern angepasst werden kann. Genauso werden Aktuatoren zum Verstellen der neigungsvariablen Treppen genutz. Die Höhenverstellung lässt sich über Tasten an der Plattform steuern. Wenngleich eine deutliche Verbesserung im Vergleich zu den Spindelhubstützen, erschien Spika diese simple Anordnung von Aktuatoren noch als suboptimal. Schwankungen in der Lastverteilung oder Bodenbeschaffenheit führten immer wieder zu schief stehenden Plattformen. Eine ungleich verteilte Last führte z.B. dazu, dass der eine Aktuator schneller herauffährt als der andere, sodass es auch zu mechanischen Belastungen kommt.
Ruckfreie Synchronisierung
Um die Arbeitsbühnen stets in Waage zu halten, wurde eine frühe Generation selbst-synchronisierender Aktuatoren eingesetzt. Doch die Kunden verlangten immer größere Verstellbereiche bei höheren Lasten. „Waren früher 600mm Verstellweg oft ausreichend, werden heute nicht selten 2m oder mehr verlangt“, sagt Ruffner. Gesucht wurden also schnellere Aktuatoren mit höherer statischer Haltekraft. Nach Auswertung mehrerer Optionen entschied sich Spika für den elektromechanischen Aktuator Electrak HD von Thomson. Er bietet die notwendige Geschwindigkeit und Tragzahl, um wechselnden oder ungleichmäßigen Lastbedingungen standzuhalten. Bei einer Geschwindigkeit von über 38mm/s, einer statischen Tragzahl bis 18kN und Hublängen bis zu 1.000 mm erlauben die Antriebe ruckfreie Synchronisierung. Thomson liefert sie zudem innerhalb von zwei bis drei Wochen. Zur Synchronisierung verfügen die Aktuatoren über einen integrierten Mikrocontroller, mit dem sie über einen gemeinsamen Schaltkreis kommunizieren. Sie benötigen lediglich jeweils zwei Leiter für die Verbindung zur Stromversorgung. Anschließend kann jeder der Aktuatoren im Schaltkreis genutzt werden, um das System anzusteuern, wozu er über ein dreiadriges Niederstromkabel mit einem einfachen Schalter oder dem binären I/O einer SPS verbunden wird. In einer typischen Konfiguration liefert ein Aktuator als Master den Bezugspunkt auf den sich alle übrigen synchronisieren. Zudem bewegen sich alle Aktuatoren unabhängig von Laständerungen mit einer voreingestellten Geschwindigkeit. Wenn die Ansteuerung von der ganz eingefahrenen Stellung aus beginnt, folgt daraus eine stoßfreie, synchronisierte Bewegung, die asymmetrische und sogar wechselnde Lasten beherrscht. Unabhängig von der jeweiligen Lastverteilung bleiben die Bühnen stets in Waage.