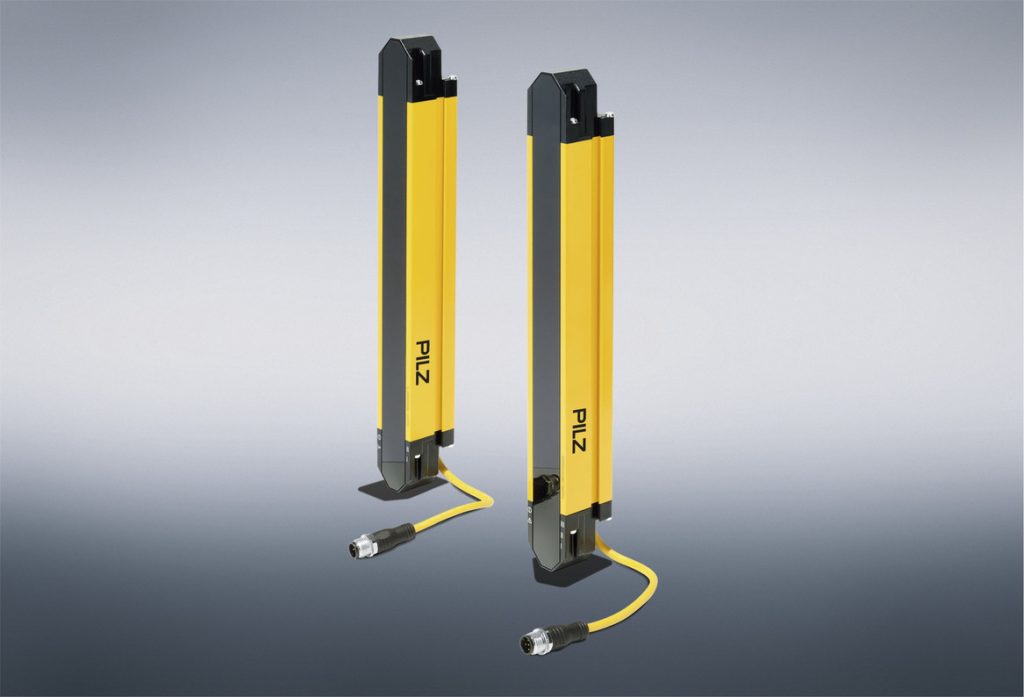
Berührungslos wirkenden Schutzeinrichtungen, kurz BWS, bieten sich überall dort an, wo Bediener oft und regelmäßig in den Gefahrenbereich einer Maschine eingreifen. Wenn auf das Öffnen von mechanischen Schutzeinrichtungen verzichtet werden kann, spart das Zeit und Arbeitsaufwand. So wird die Anlage produktiver und der Arbeitsplatz bedienerfreundlicher. Auch werden umstehende Personen geschützt, weil das unbewusste Eingreifen in die Gefahrensituation einen Maschinenstopp herbeiführt. Zudem werden BWS immer häufiger im Zusammenhang mit arbeitsplatzunterstützenden Robotern eingesetzt.
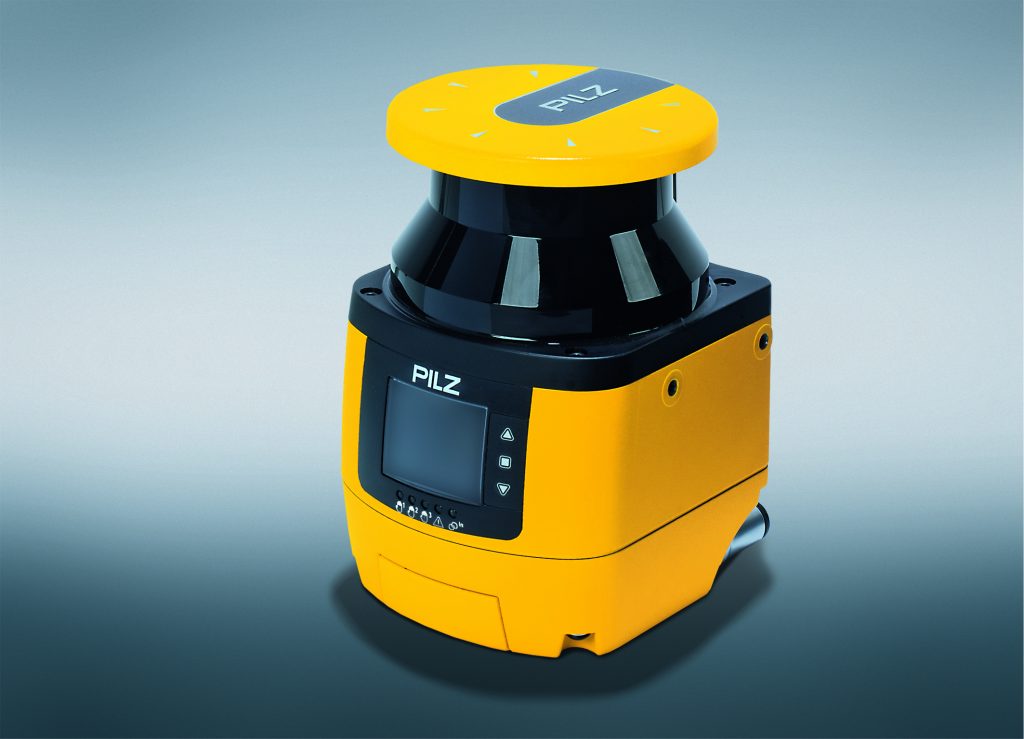
Pflichten der Betreiber
Arbeitsschutzgesetz und Betriebssicherheitsverordnung (BetrSichV) erfordern es, Gefahrensituationen am Arbeitsplatz zu analysieren und geeignete Schutzmaßnahmen zu treffen. Für Maschinen bedeutet das, dass der Betreiber vor der ersten Verwendung eine Gefährdungsbeurteilung erstellen und das System prüfen muss. Die erste Prüfung der BWS zielt insbesondere auf die ordnungsgemäße Montage, Installation und sichere Funktion. Zudem ist es Pflicht, die BWS wiederkehrend zu prüfen. Der Betreiber muss dabei feststellen, dass der Stand der Technik erhalten bleibt. Die technischen Regeln TRBS 1201 zur Prüfung von Arbeitsmitteln konkretisieren die Anforderungen an Prüfart, -umfang und -fristen. Für die Einhaltung der Prüffristen sind die Betreiber verantwortlich. Zunächst gilt es zu kontrollieren, ob die BWS in der bei Inbetriebnahme festgelegten Position sicher montiert ist, ob sie verändert oder manipuliert wurde und ob sie den Arbeitsablauf beeinträchtigt. Mit einer kalibrierten Nachlaufmessung wird die Zeit vom Anhalten der Funktion bis zum tatsächlichen Stillstand der Maschine ermittelt. Wenn die Messergebnisse von den Herstellerangaben abweichen, kommt es darauf an, dass der berechnete Sicherheitsabstand auch bei maximaler Nachlaufzeit ausreicht. Andernfalls muss der Betreiber eine neue Gefährdungsbeurteilung erstellen und Maßnahmen ergreifen. Wichtig ist auch: Gibt es eine Wiederanlaufsperre, wenn sich eine Person im Gefahrenbereich befindet? Gibt es Vorkehrungen zur Wiederaufnahme des Betriebs, wenn die Schutzeinrichtung ausgelöst und die Maschine in einen sicheren Zustand überführt hat? Ist der Gefahrenbereich aus einer nicht abgesicherten Richtung zugänglich?
Besondere Herausforderungen
Bei den Prüfungen sind Knowhow und Erfahrung gefragt, damit es nicht zu Detailfehlern kommt. Erhöhte Aufmerksamkeit erfordern z.B. BWS an fahrerlosen Transportsystemen (FTS). Hier dienen die Schutzeinrichtungen dazu, Personen und Gegenstände im Fahrweg zu erkennen und Kollisionen zu verhindern. Häufig kommen Laserscanner gemeinsam mit Drucksensoren zum Einsatz, die das System bei Kontakt anhalten. Die Besonderheit bei FTS: Die Reaktionszeit (Nachlaufzeit, bzw. Nachlaufweg) zur Abschaltung der Fahrbewegungen zu ermitteln ist besonders wichtig, jedoch mitunter nicht ganz einfach. Wie sehr das Fahrzeug verzögert und wie schnell es schließlich zum Halt kommt hängt von den Umgebungsbedingungen ab. Diese sind nicht immer konstant und damit auch die Prüfbedingungen nicht. Auf den Bremsweg wirkt sich vor allem die Art des Bodenbelags aus. Wenn ein FTS in Außenbereichen eingesetzt wird, spielen auch Luftfeuchtigkeit und -temperatur eine Rolle. Weil die Systeme nicht fest im Raum montiert sind, lassen sich die Messgeräte für die Prüfungen nicht immer exakt gleich zum Fahrzeug positionieren. Auch bei Förderbändern ist Bewegung ein erschwerender Faktor für die BWS-Prüfung. Neben beweglichen Teilen der Anlage selbst, kann auch vom Transportgut eine Gefahr ausgehen. Das Produkt auf einem Förderband ist nicht gegen verrutschen gesichert. Der plötzliche Stillstand der Anlage sorgt unter Umständen für eine gefährliche, weil unkontrollierte Bewegung. Beziehen die Ingenieure die Schutzwirkung auf diese Produktbewegung, können sich, je nach Gewicht und Reibung, verschiedene Messwerte ergeben. Besondere Bedingungen ergeben sich auch durch Muting-Funktionen. Sie setzen die Auslösung der Sicherheitsfunktion durch die BWS zeitlich begrenzt außer Kraft. Nötig ist das etwa beim Transport von Waren in einen Sicherheitsbereich oder aus diesem heraus. Während die Funktion pausiert, müssen andere Maßnahmen die Sicherheit gewährleisten. Anschließend muss die BWS ihre Funktionen wiederherstellen. Prüfer müssen das Muting bei den Messungen berücksichtigen.
Funktionstest vs. Prüfung
Ungeachtet der wiederkehrenden Prüfungen schreiben Hersteller meist regelmäßige Funktionstests für BWS vor. Maschinenbediener stellen mit diesen, häufig arbeitstäglichen Kontrollen sicher, dass das System jederzeit einen wirksamen Schutz bietet. Mit einfachen Sichtprüfungen erkennen sie offensichtliche Schäden. Durch einmaliges Auslösen mittels eines Prüfstabes verifizieren sie die Funktionstüchtigkeit der Einrichtung und ob sich die Umgebungsbedingungen geändert haben. Idealerweise testen die Bediener die Anlagen selbst. Eine einfache Unterweisung reicht dafür in der Regel aus. Die Tests ersetzen keinesfalls die gesetzlich vorgeschriebenen, wiederkehrenden Prüfungen, bei denen die gesamte Einbausituation, der Auslösevorgang und der Nachlauf von einer befähigten Person detailliert untersucht werden.