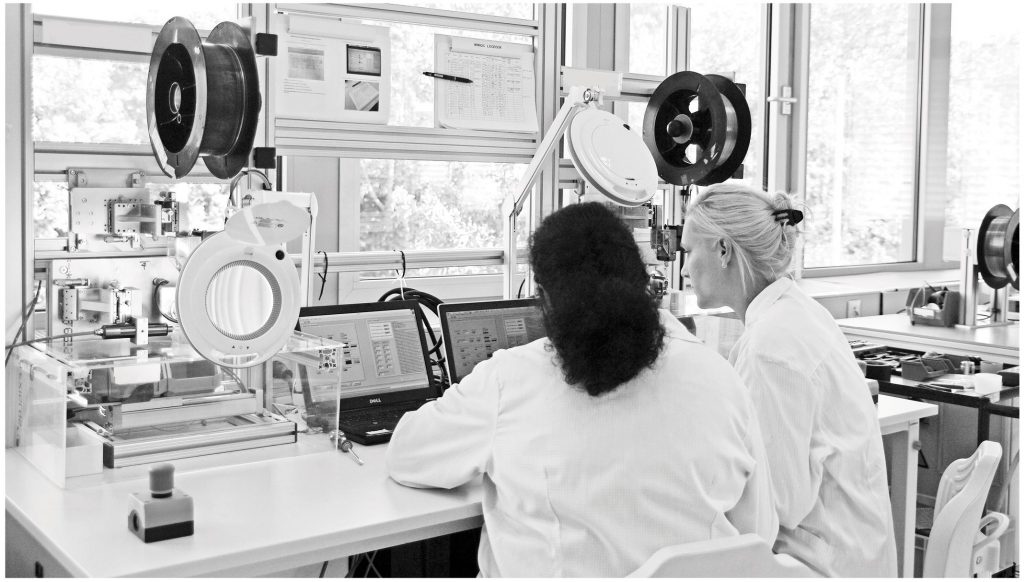
Die erste Besonderheit besteht darin, dass sich jeder Mitarbeitende der Centitech morgens frei entscheiden kann, an welchem der vorhandenen Schreibtische er sich mit seinem Laptop niederlässt. Dieses ungebundene Prinzip entspricht der Fraba-Philosophie, dass alles im Fluss ist. 2011 zog die Produktentwicklung vom Kölner Firmenhauptsitz nach Aachen um, drei Jahre später eröffnete dann an gleicher Stelle das Wiegand-Technologiezentrum. Mittlerweile arbeiten am Standort im Dreiländereck 40 Forscher und Entwickler aus 12 Ländern. Insgesamt beschäftigt die Fraba-Gruppe derzeit weltweit 230 Mitarbeiter. Die Firmensprache ist Englisch. Einer der Gründe für den Umzug war die enge Zusammenarbeit der Fraba-Entwickler mit der Rheinisch-Westfälischen Technischen Hochschule (RWTH) sowie der Fachhochschule (FH) Aachen. „Bei uns laufen die Ideen für neue Produktentwicklungen aus sämtlichen Fraba-Standorten weltweit zusammen und werden dann umgesetzt. Das Produktmanagement für Europa befindet sich in Köln. Ferner betreuen Produktmanager in Amerika und Asien ihre jeweiligen lokalen Märkte. Sie sind genauso stimmberechtigt im Hinblick auf Neuentwicklungen wie die Produktmanager in der rheinischen Firmenzentrale, da sie ihre Märkte und deren Bedarfe am besten einschätzen können“, erläutert Dimitri Pritzkau, dessen Funktion als Leiter von Entwicklungsprojekten bei Fraba sich erst auf Nachfrage offenbart, da keiner der Mitarbeiter seine Stellung innerhalb des Unternehmens auf der Visitenkarte aufgedruckt hat. Hierarchie bedeutet nicht viel beim Drehgeberspezialisten, der eher auf Kompetenz und Eigenverantwortung setzt. Bei allen länder- und branchenspezifischen Anpassungen der Drehgeber besteht ein wesentliches Merkmal der Produkte in ihrer Modularität, das heißt sie haben alle einen identischen Kern und werden dann je nach Bedarf im Baukastenprinzip zusammengestellt. Auf diese Weise bleibt die ungeheure Varianz an Drehgebern der Marke Posital gut beherrschbar.
Feiner Draht mit Potenzial
Ein wesentlicher Faktor für das mit 12,4 Prozent im Jahr 2018 wieder überdurchschnittliche Wachstum findet sich im Mikrokosmos des Wiegand-Technologiezentrums, das 2014 innerhalb der Centitech eröffnet wurde. Die Einrichtung beschäftigt sich mit der Weiterentwicklung der 1972 vom amerikanischen Forscher John Wiegand begründeten Technologie (siehe Kasten) und ist zudem eine von weltweit zwei Fraba-Produktionsstätten für den Wiegand-Draht. Die zweite Fertigung befindet sich im US-Bundessraat New Jersey, die ausschließlich für den amerikanischen Markt produziert. „Am Anfang wurde die Technologie vorwiegend bei Chipkarten in Systemen für die Zutrittskontrolle eingesetzt. Seit Mitte der 2000er Jahre ist sie vor allem in Zusammenhang mit dem Thema ‚Energy Harvesting‘ interessant, da sie einen batterielosen, energieautarken Betrieb von Sensoranwendungen ermöglicht“, sagt Dimitri Pritzkau. Der Fraba fällt dabei eine Art Hüter- und Haupttreiberrolle dieser Technologie zu, nachdem sie vor fünf Jahren die Produktionsmittel und das Knowhow übernommen hat, die teilweise bis zu der von John Wiegand gegründeten Firma zurückreichen. Das Aachener Team hat sich seitdem verdoppelt. „Wichtig bei der Drahtfertigung ist einmal natürlich dessen Zusammensetzung, die schriftlich in der sogenannten Wiegand-Bibel festgehalten ist. Hierzu dürfen nur sehr hochwertige Materialien verwendet werden, denn selbst kleinste Verunreinigungen können den benötigten Effekt zunichte machen. Zudem ist das Verfahren, mit dem der Draht produziert wird, sehr aufwendig“, betont Pritzkau. Ganz wichtig bei der Herstellung des Produktes ist die Qualitätskontrolle. Daher werden alle Drähte individuell geprüft. „Innerhalb eines Drahtes kann es durchaus unterschiedliche Qualitäten geben. Mittlerweile verfügen wir über einen Automaten, der den Draht einzieht, scant und schließlich die guten Abschnitte herausschneidet“, so der Entwicklungsleiter. Pro Tag fertigt Fraba rund einige Tausend Stück des feinen Drahtes, der in eigenen, aber auch in Produkten von Drittanbietern eingesetzt wird, die sich der Wiegand-Technologie bedienen. Fraba liefert die Drähte in seine Produktionsstätten im polnischen Slubice sowie nach Malaysia, wo dann die eigentlichen Wiegand-Sensoren hergestellt werden. Anders als bei den optischen Drehgebern sieht Pritzkau das Entwicklungspotenzial bei Sensoren, die auf dem magnetischen Prinzip basieren, noch lange nicht ausgereizt: „Die Präzision der Magnetik werden wir mit der entsprechenden Rechenpower weiter steigern können. Folgt man dem Moorschen Gesetz, müssen wir also lediglich auf die ständig steigende Leistungsfähigkeit der Microchips vertrauen. Zudem sind wir sehr zurversichtlich und arbeiten mit Hochdruck daran, auch die Energieausbeute beim Energy Harvesting weiter zu steigern.“ Derzeit erzeugt der Wiegand-Effekt 7V bzw. 190 nJ. Neben der höheren Energieausbeute, die eine weitere Verkleinerung des Sensors bewirken könnte, forschen die Mitarbeiter an den insgesamt sechs Prüfplätzen u.a. noch an der Stabilisierung der Drahtgüte und der damit verbundenen Verringerung des Ausschusses.
Pro Tag werden in Aachen rund 2.000 Stück des Wiegand-Drahtes gefertigt. – Bild: Fraba GmbH Die Einzelbestandteile des Wiegand-Sensors – Bild: Fraba GmbH Der Wiegand-Sensor montiert auf einem Drehgeber der Marke Posital – Bild: Fraba GmbH
Encoder-Kits für die einfache Nachrüstung
So herausfordernd und spannend das Wiegand-Thema auch ist: Der Löwenanteil der F&E-Tätigkeit in Aachen entfällt auf andere Bereiche. Derzeit ist dies vor allem die Entwicklung der 3. Generation von Kit-Encodern, die direkt an der Antriebswelle montiert werden und die eine kostengünstige Nachrüstung vereinfachen. Jüngste Mitglieder im Produktportfolio sind die magnetischen Motorfeed-Kits für Schrittmotoren mit BiSS C- sowie SSI-Schnittstelle. Auch diese machen sich Energy Harvesting zunutze. Etliche der Innovationen gehen auf die enge Zusammenarbeit mit Partnern wie z.B. Antriebsherstellern zurück, wobei Fraba im Vorfeld deren Anforderungen genau evaluiert. Die Dynamik seines F&E-Teams sieht Pritzkau dabei in der eingangs erwähnten Mündigkeit jedes Einzelnen begründet: „Dies geht so weit, dass wir bei Bewerbungsgesprächen Teams von bis zu fünf Personen bilden, bei denen jeder ein Mitsprache- und Vetorecht hat, ob jemand eingestellt wird oder nicht. Die Entscheidung für oder gegen einen Bewerber fällt dann stets am Tag des Gesprächs.“ Die hohe Internationalität stellt laut Pritzkau einen echten Wettbewerbsvorteil insbesondere auf dem Gebiet der Forschung dar, da es keinerlei Verständigungs- und damit Integrationsprobleme talentierter Nachwuchskräfte gebe. Interessenten dürften einen Tag im Unternehmen verbringen und Mitarbeiter mit Fragen ‚löchern‘. Ist ein neues Mitglied ins F&E-Team aufgenommen, muss es ein sogenanntes ‚Eiswasser-Projekt‘ bearbeiten, das in Alleinregie nicht zu lösen ist und für das es sich aus dem Team heraus die notwendigen Informationen und Ressourcen erarbeiten muss. Hierdurch solle die ‚Spielfreude‘, die für das Arbeiten bei Fraba so wichtig ist, geweckt werden. Dynamisch sind auch die Entwicklungsmöglichkeiten innerhalb der Fraba. „Wir praktizieren Offenheit in alle Richtungen. Wenn jemand z.B. nicht mehr in der Entwicklung arbeiten und lieber ins Produktmanagement oder den Vertrieb wechseln möchte, so wird ihm dies in aller Regel ermöglicht. Vor meiner Tätigkeit hier in der Entwicklung war ich beispielsweise Produktmanager für den Bereich Neigungssensoren“, berichtet Dimitri Pritzkau, dem sein Unternehmen, das 2018 immerhin sein 100-jähriges Bestehen feierte, manchmal wie ein Startup vorkommt. So lange es gut läuft, muss sich die Mannschaft in Aachen auch keine Gedanken um die finanziellen Ressourcen machen. „Konservativ geschätzt, investieren wir gut zehn Prozent unseres Umsatzes in Forschung und Entwicklung – ein sehr hoher Anteil, der aber essenziell für unsere Innovationsfreude ist“, sagt Dimitri Pritzkau abschließend. (jwz)