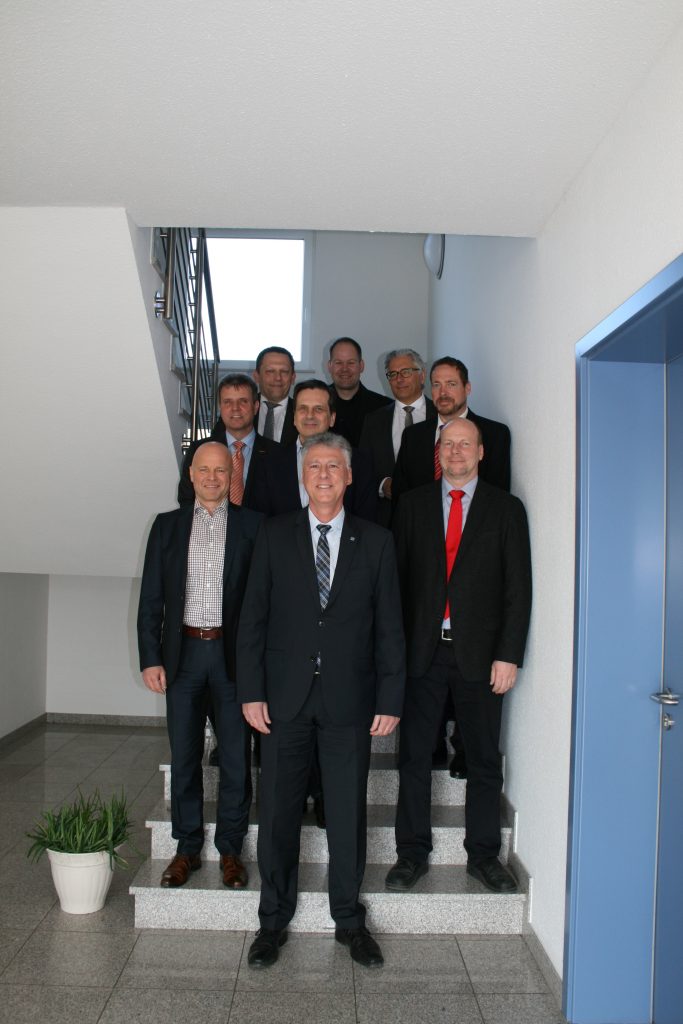
Sind IO-Link oder OPC UA mögliche Industrie-4.0-Schnittstellen für Drehgeber?
J. Pohany (Baumer): Bei den Absolutwertgebern werden wir Bussysteme wie OPC UA mit TSN sehen. Auch wir haben kundenspezifische inkrementale Drehgeber mit IO-Link entwickelt. Dort kann ich die Parametrierung über IO-Link durchführen, und das gleich weitergeben, was ich parametriert habe inklusive Metadaten. Das kann ich zwar auch bei Bus-basierten Gebern, nur beim Inkrementalgeber tue ich mich da noch ziemlich schwer. Dort kann IO-Link das Mittel der Wahl sein, um preisgünstig additive Daten weiterzugeben.
C. Leeser (Posital): Wir Drehgeberhersteller sind am Ende der Nahrungskette, d.h. wir können zwar darüber spekulieren, was sich durchsetzt, werden aber nicht darüber entscheiden; das sind die Steuerungs- bzw. Umrichterhersteller. Bei IO-Link bin ich mir ziemlich sicher, dass wir uns dort nicht die Finger verbrennen werden.
T. Brandenburger (Hübner): Bei Industrie 4.0 werden sich Double-Chanel-Strukturen durchsetzen. Wir brauchen also einen zweiten Kanal, über den Metadaten oder Parameter ausgetauscht werden. Welche Technik das sein wird, können wir aber heute noch nicht überblicken. IO-Link finden wir zwar für Inkrementalgeber interessant, allerdings haben wir dazu bisher kaum Anfragen gehabt.
P. Elbel (Hengstler): Oft ist über der IO-Link-Ebene noch Profibus/Profinet und dann ist es meist einfacher einen Profibus-/Profinet-Geber einzusetzen.
A. Hettich (Kübler): Ein Drehgeber wird zukünftig durch Integration weiterer Intelligenz zu einem zentralen Datensammelpunkt in einem Antrieb bzw. Achse werden, d.h. wir benötigen eine Schnittstelle, wie OPC UA, die kostengünstig zu implementieren ist. Der Mehrwert, irgendwelche Daten zu sammeln und irgendwohin zu schicken, muss allerdings da sein, damit der Geber auch mehr kosten darf.
Welche Rolle werden Drehgeber bei Industrie 4.0 spielen?
Pohany: Siemens, Microsoft, SAP und Intergraph haben bereits 1998 eine Road Show zum Thema ‚The internet enabled manufacturing company‘ gemacht. Warum hat man aber knapp 20 Jahre gebraucht, um zu den ersten Implementationen zu kommen? Die Technologie musste erst preiswert und miniaturisiert genug sein, damit sie von der MES-Ebene in die Steuerungsebene und von dort in die Sensorikebene kommt. Je mehr preiswerte Rechenpower wir haben, umso mehr können sie an Funktionalität, die heute noch ausgelagert in Steuerungssystemen ist, direkt in den Drehgeber integrieren. Die Datennachbearbeitung der Sensorik wird zunehmend von der SPS in Richtung Drehgeber gehen. Zukünftig wird es also neben der klassischen Automatisierungspyramide auch Kanäle aus der Sensorik direkt in das MES oder in weiterführende Systeme geben.
Hettich: Für mich kann ein Drehgeber in Antrieben oder Achsen der Knotenpunkt sein, um Daten zu sammeln, allerdings nur, wenn man es zu vernünftigen Kosten implementieren kann. Die Frage ist, welche Schlüsse aus den Daten dann gezogen werden. Dort kommen wir ins Condition Monitoring oder Predictive Maintenance, was wir als Drehgeberhersteller nicht alleine definieren können. Hinsichtlich Industrie 4.0 oder IoT kann ich mir vorstellen, dass ein Knotenpunkt vom selbstständigen Bestellvorgang des Ersatzteiles bis hin zu Optimierung von Produkten und Maschinengenerationen dann alles selbst regelt.
Leeser: Es gibt Studien, dass wir vor zwei Jahren das erste Mal mehr IoT-Devices hatten als Menschen auf der Erde und die Vorhersage ist, dass wir bis 2020 weltweit über 50Mrd. IoT-Punkte haben. Dies bedeutet, dass an jeder Stelle, wo irgendeine Infrastruktur liegt, überall preisgünstige Sensoren sein werden. Da die Anzahl der IoT-Knoten viel schneller wächst als die installierte Basis der Maschinen, bedeutet dies, dass wir über einen Retrofitting-Markt reden. Es werden dort Systeme und Produkte kommen, die man an bestehende Maschinen ‚anklebt‘.
Pohany: Dank einer digitalen Schnittstelle bekommen wir mehr Informationen über den Lebenszustand eines Drehgebers, woraus wir Rückschlüsse auf die Applikation ziehen können. Unser neuer Geber für den Bahnbereich hat bereits eine integrierte Schnittstelle für Temperatur und Vibration. Das Problem ist die Normgebung an einer Lokomotive, die sagt, dass dort eine analoge Schnittstelle sein muss. Sie müssen also zwei Schnittstellen integrieren, um die analogen Drehzahlen und die additiven digitalen Daten zu übermitteln.
Für wen sind die Daten sinnvoller: Für die Hersteller oder den Anwender?
Leeser: Über eine große installierte Basis und die daraus verfügbaren Daten kann man schon einige Informationen erhalten. Wenn man diese dann noch mit Input aus der Anwendung verknüpft, kommen wir zu Smart Data. Dazu ist es aber notwendig, dass die Kunden Daten übermitteln, damit wir die statistischen Vorteile von Big-Data-Analysen nutzen können. Dazu wird allerdings Überzeugungsarbeit nötig sein, damit der Kunde uns seine Funktionsdaten übermittelt. Nur so kann die installierte Basis der Produkte besser werden und wir ihm vorhersagen, was passiert.
D. Schömel (Wachendorff): Wir müssen dann aber auch die richtigen Fragen stellen und die richtigen Antworten geben können, wenn der Konstrukteur nachfragt. Wir sind dann nicht länger nur Drehgeberhersteller, sondern müssen auch Branchenwissen aufbauen, um mit unserem Drehgeberwissen den Konstrukteur, der nur sein Branchenwissen hat, zu überzeugen.
Elbel: Wir liefern im Moment die Daten. Wer diese dann auswertet und nutzt – Drittanbieter, Sensorhersteller oder Kunde – ist noch offen.
Pohany: Es wird zukünftig dezentrale, intelligente Einheiten geben, bei denen ich neben der Intelligenz in der Sensorik und Aktorik auch eine kleine Micro-SPS und den Sammelknoten habe. Ich glaube nicht, dass das alles in einen Sensor oder Drehgeber rein geht, sondern wir werden einen Datenknoten haben, der ein wenig Intelligenz beinhaltet.
Hettich: Die Daten für Condition Monitoring oder Predictive Maintenance zur Verfügung zu stellen, kann parallel stattfinden, z.B. über Drehgeber mit einer Ethernet-Schnittstelle. Dort sehe ich bereits schon eine gewisse Intelligenz vorhanden.
Schömel: Wir werden in der Sensor-Aktor-Welt eine Vorverdichtung der Daten haben, um die Geschwindigkeit zu erhöhen. Alles, was ich der SPS an Arbeit abnehmen kann, macht sie für ihre eigentlichen Steuerungs- und Regelungsaufgaben schneller. Echtzeit werden wir zwar nicht erreichen, aber je näher wir dahin kommen, umso schneller können auch die Maschinen agieren und der Kunde hat letztendlich einen höheren Profit. Allerdings wird für die korrekte Inbetriebnahme eines intelligenten Sensors ausgebildetes Personal benötigt.
Pohany: Plakativ ausgedrückt: Der Drehgeber darf nicht intelligenter sein als derjenige, der ihn anschraubt. Wenn sie einen Heavy-Duty-Drehgeber anbringen, ist alles unter einem 18er- Schlüssel schon Feinmechanik. Demjenigen, der so ein Gerät installiert, auch noch beizubringen, wie er OPC UA parametriert, wird schwierig. Auf der anderen Seite haben wir ein System auf den Markt gebracht, das quasi ein Resolver-Ersatz ist, bei dem wir von den vielen Leitungen, die von dem Resolver weggegangen sind, nun zu einer One-Cable-Technologie gekommen sind. Das wird nicht von einem Monteur mit einem 32er-Schlüssel montiert, sondern dort, wo der Motor hergestellt wird und dort haben wir eine ganz andere Intelligenz bei den Personen.
Wie klein kann ein Drehgeber werden?
Leeser: Das Wachstum des Marktes wird wahrscheinlich in kleineren Größen stattfinden. So werden Roboter und Cobots immer kleiner. Ein Robotsensor ist fast nicht mehr sichtbar und die begrenzenden Faktoren, wie klein die Geräte werden, kommen eher von der Kommunikationstechnik. Wenn sie einen Profinet-Chip einbauen, bestimmt der die Größe des Sensors.
Elbel: Da ist auch der Stecker das limitierende Element. Ein 17-poliger M8-Stecker macht dort keinen Sinn.
Hettich: Es gibt bereits 24er-Drehgeber, aber es kommt immer auf die Relation an, was gefordert ist, z.B. ein kleiner Durchmesser oder Bautiefe. Dann kommen wir wieder zu den lagerlosen Systemen. Wenn sie eine große Hohlwelle haben, dann macht es keinen Sinn einen 24er-Geber gelagert anzubauen.
A. Bäuerle (TR-Electronic): Den kleinsten Geber, den wir momentan anbieten, ist ein 22er-Multiturn-Absolutwertgeber mit Getriebe. Es geht zwar noch kleiner, dann aber in schlichter Bauform als Singleturn-Geber auf Chipgröße.
Pohany: Wir haben 20mm-Geber im Portfolio und gerade einen magnetischen 28mm-Geber gelauncht. Der begrenzende Faktor ist tatsächlich der Übertragungschip. Allerdings habe ich bei einigen Technologiefirmen bereits Geberprototypen im Bereich von 14mm gesehen. Wenn ich Cobots betrachte, die nicht in einem industriellen Umfeld, sondern eher im Haushalt eingesetzt werden, kann ich mir aber durchaus vorstellen, dass es in eine solche Richtung geht. Allerdings ist dies dann kein Anbaugeber mehr, sondern ein Kit, das ich in einen Motor mit einbaue.
Leeser: Die Tatsache, dass man das Lager und Flansch einspart, wird immer wichtiger, je kleiner man wird. Die Cobots werden kleine Elektromotoren haben, bei denen der Sensor mit drin ist. Wir sehen für Drehgeber ein sehr positives Marktumfeld. Im Vergleich zu Hydraulik und Pneumatik gewinnt der elektrische Antrieb immer mehr an Bedeutung. Da die Wertschöpfung immer mehr in Richtung Algorithmen, Mikroprozessoren und Programmierung geht und die Mechanik an Stellenwert verliert, ist dies ein Prozess, dem wir uns stellen müssen, aber nicht aufhalten werden.
Brandenburger: Zudem wird nicht nur der Drehgeber intelligenter, sondern andere Maschinenteile auch. Bei Kugellagern sieht man heute schon erste Beispiele, die bereits Drehzahlen messen. Vielleicht wird irgendwann in gewissen Applikationen der Drehgeber gar nicht mehr gebraucht, weil das Kugellager die Informationen liefert, oder ein anderes Element.
Pohany: Ein Motorenhersteller hat einmal gesagt, ich habe für einen Drehgeber genau zwei Prämissen: Ich will euch los haben, weil Ihr mir zu teuer seid und wenn ich euch nicht los werde, dann müsst Ihr gefälligst mehr tun, als nur eine Drehzahl zu übermitteln. Die Motorenhersteller versuchen im Antriebsbereich, wo es geht, Lösungen ohne einen Drehgeber anzubieten. Wenn sie aber einen Drehgeber nehmen müssen, dann soll der mehr tun, als nur ein inkrementales Drehzahlsignal zu übermitteln.
• Baumer Group: Dr. Johann Pohany,
Leiter Produktsegment Motion Control
• Posital: Christian Leeser, CEO
• Fritz Kübler GmbH: Arnold Hettich,
Produktmanager Positions- & Bewegungssensorik
• Hengstler GmbH: Peter Elbel,
Manager Product Implementation
• Johannes Hübner Gießen: Thomas Brandenburger,
Leitung Produktmanagement
• TR-Electronic: Andreas Bäuerle, Technischer Vetrieb
• Wachendorff Automation GmbH & Co. KG: Dieter Schömel,
Produkt- & Key Account Manager