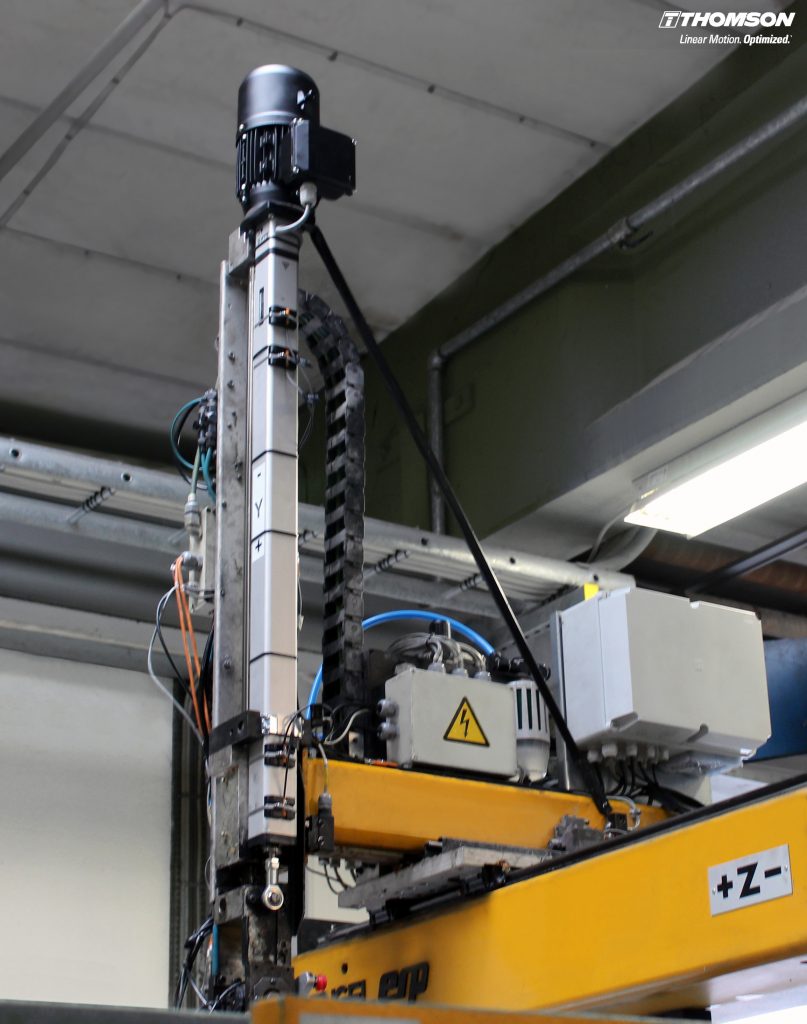
Als das Unternehmen Raaco vor rund 60 Jahren im dänischen Nykøbing die Produktion von Regal- und Transportsystemen aus Kunststoff aufnahm, waren pneumatische Aktuatoren die bevorzugte Technik für Spritzgussanlagen und halbautomatische Schweißstraßen. Dass diese jedoch anfällig für Druckverluste und Undichtigkeiten sind, machte sich auch bei Raaco über die Zeit immer mehr bemerkbar. Angetrieben von der Notwendigkeit einer höheren Produktionsleistung, um angesichts globaler Märkte und steigender Energiepreise wettbewerbsfähig zu bleiben, fiel der Entschluss, die vorhandenen Aktuatoren auf eine elektrische Lösung aufzurüsten.
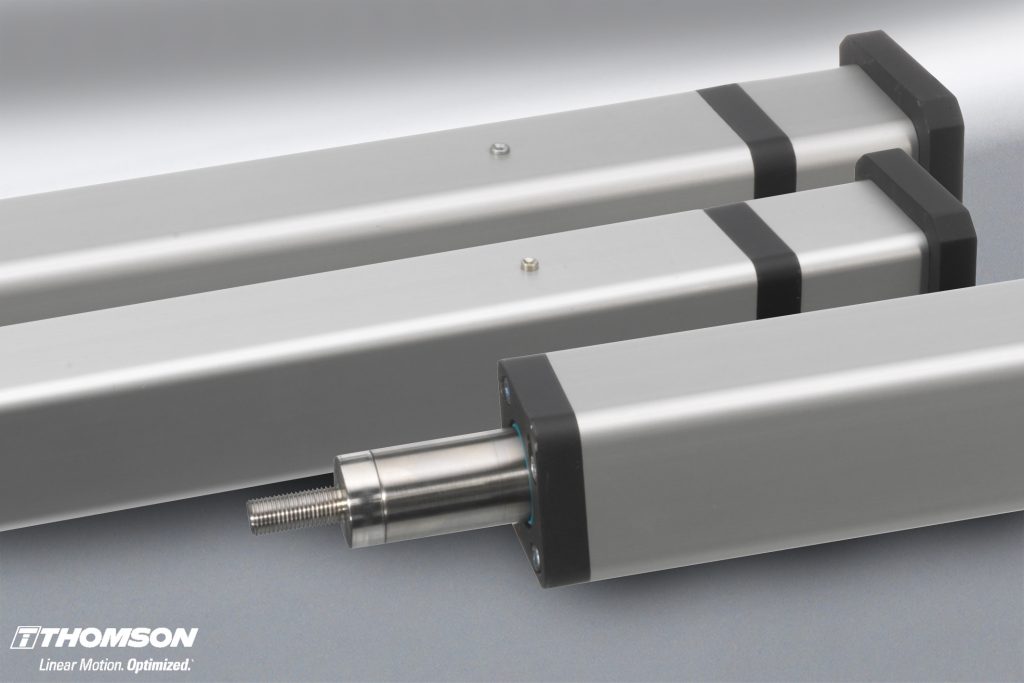
Kompakt und zuverlässig
Um seine Möglichkeiten auszuloten, wandte sich Raaco an den dänischen Thomson-Vertriebspartner AVN Teknik, über den das Unternehmen seit vielen Jahren Industriekomponenten bezieht. Unter Berücksichtigung der Vorgaben nach einer kompakten, zuverlässigen und langlebigen Lösung, die zudem kurze Entwicklungszyklen ermöglicht, analysierte Flemming Blauert, Produktexperte bei AVN Teknik, das Problem. „Die auf pneumatische Zylinder einwirkende Last verdichtet die Luft in einem unerwünschten Maß, was die Präzision und Steuerbarkeit der Systeme beeinträchtigt. Wir kamen zu der Einschätzung, dass bei Raaco zwischen dem Kompressor und dem Stellglied fast ein Drittel der Verdichtungsleistung verloren ging“, so Blauert. „Anschließend verglichen wir die Möglichkeiten der Aktorik, wobei wir die Parameter Kosten, Effizienz, Produktivitätssteigerung, Wartung und Sicherheit zugrunde legten.“ Raaco wusste, dass die Aktuatoren ohnehin ausgetauscht werden mussten, und war darauf eingestellt, die Kosten dafür zu tragen. Ob man in diesem Rahmen mit 1.800E für elektromechanische Aktuatoren jedoch das fünffache des Preises von Pneumatik-Aktuatoren ausgeben (360E) würde, sollte vom tatsächlichen Nutzen des Technologiewechsel abhängen. Das Ergebnis zeigt, dass sich die Anschaffung von elektromechanischen Aktuatoren gleich mehrfach lohnt.
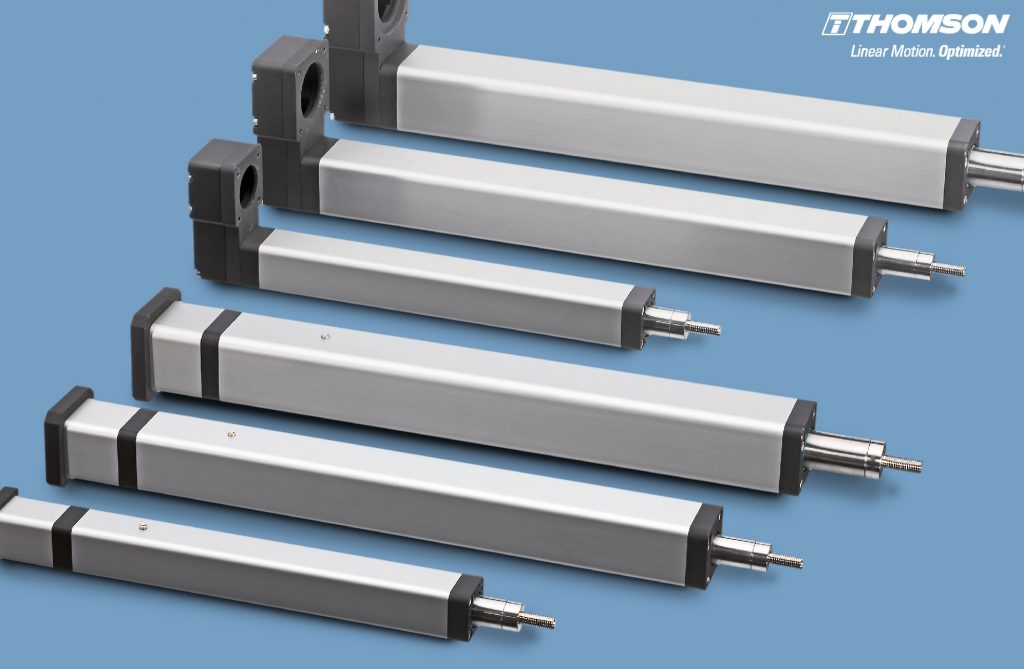
Betriebskosten und Wirkungsgrad
Mit Hilfe eines von Thomson bereitgestellten Dimensionierungs- und Berechnungs-Tools, das Abmessungen, Drehmomente, Energiekosten, Arbeitsspiele, Auslastung und Umgebungsfaktoren einbezieht, wurden die Betriebskosten eines Pneumatikzylinders auf 739E pro Jahr veranschlagt – dazu stehen im Vergleich lediglich 63E für den elektromechanischen Zylinder. Pneumatisch betriebene Aktuatoren verbrauchen erheblich mehr Energie, da sie laufende Kompressoren erfordern, selbst wenn gerade keine Verstellbewegung ausgeführt wird. Darüber hinaus beträgt der Wirkungsgrad bezogen auf die elektrische Energie für Pneumatikzylinder gerade einmal 15 Prozent, während er im Vergleich dazu bei elektromechanischen Aktuatoren 80 Prozent erreicht. Bei Einsparungen von 613E pro Jahr amortisieren sich die elektromechanischen Aktuatoren demnach allein energieseitig innerhalb von drei Jahren. Dies stellte aber nur ein Teil der Wertschöpfung dar: Die Produkte der PC-Serie von Thomson ermöglichen darüber hinaus Verbesserungen in puncto Leistung, Produktivität und Wartung. Raaco stimmte daher einem ersten Test zu.
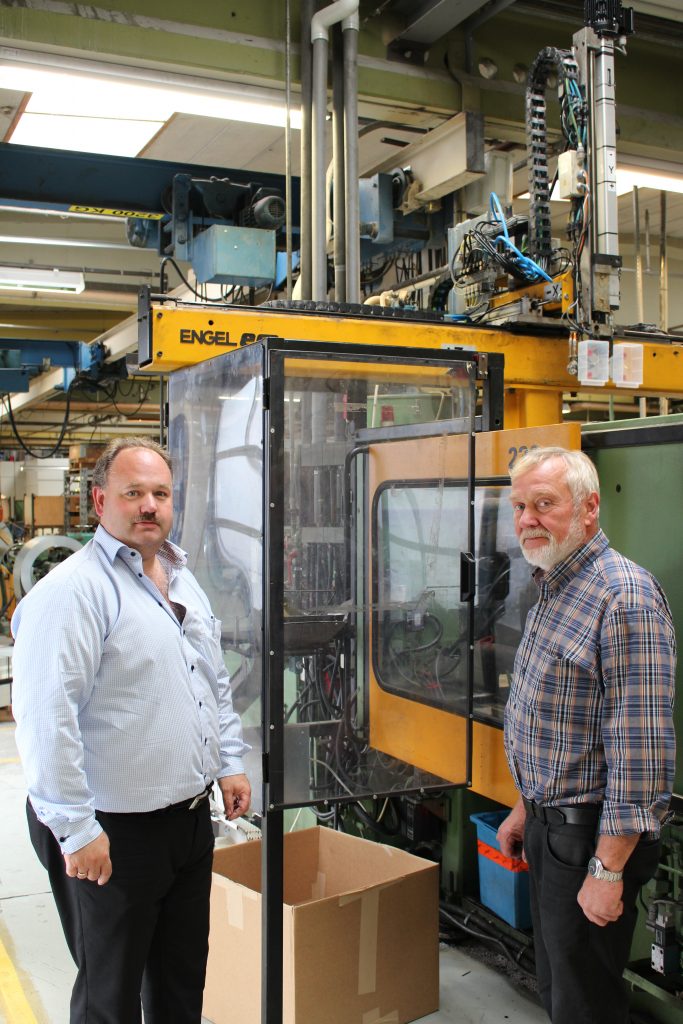
Test am Schweißautomaten
Zu diesem Zweck wurde der Pneumatikzylinder an einem Trapezschweißautomaten ersetzt, der zur Reparatur von Metallteilen dient. Wenngleich nicht direkt Teil der Produktion, reichte dieser Test aus, um die Vorteile elektromechanischer Aktuatoren gegenüber ihren pneumatischen Pendants in Bezug auf Geschwindigkeit, Sicherheit, Belastbarkeit und Energieeffizienz nachzuweisen. Im nächsten Schritt wurde der Pneumatikaktuator, der den Arm einer Spritzgusseinrichtung betätigt, durch einen PC-Aktuator getauscht. Dessen Funktion besteht darin, einen Roboterarm auf die Maschine herunterzubewegen, um ein Teil aus der Gießform zu entnehmen, es anzuheben, zur Seite zu bewegen und auf einem Förderband zur weiteren Verarbeitung abzulegen. Für die Umrüstung erwartete man bei Raaco zunächst eine Stillstandszeit mit zweitägigem Produktionsstopp. Tatsächlich waren die Aktuatoren bereits nach wenigen Stunden vollständig betriebsbereit. Die Energieeinsparungen gestalteten sich wie erwartet. Die jährlichen Energiekosten sanken hier von 179 auf 19E. Parallel zum geringen Stromverbrauch wurde eine deutliche Leistungssteigerung verzeichnet, denn der neue Aktuator dreimal so schnell wie sein pneumatischer Vorgänger. Damit spart Raaco bis zu 1,2s pro Takt. In der Zeit, in der zuvor zwei Teile aufgenommen und abgelegt wurden, schafft das System jetzt drei Teile. Bei einer durchschnittlichen Maschinentaktung von 2.880 Zyklen pro Tag ergibt sich daraus ein deutlicher Produktivitätsanstieg. Zudem verringert sich der Wartungsaufwand. Bei den elektrischen Aktuatoren sind nur dreimal pro Jahr die Schmiernippel einzufetten. Demgegenüber muss bei pneumatischen Aktuatoren ein Dehydrierungssystem gewartet werden, das die Feuchtigkeit aus der Luft zieht, bevor sie in den Zylinder gelangt. Hierzu sind häufige Schmierung und Kontrolle der Ventile und zugehörigen Armaturen erforderlich.