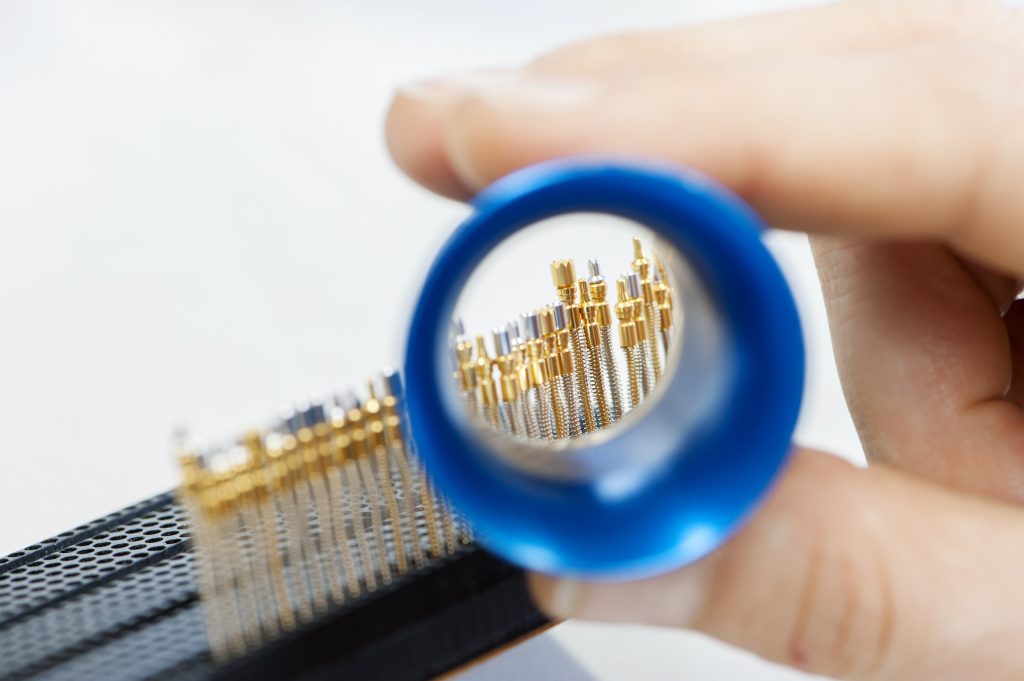
Die Ingun Prüfmittelbau GmbH produziert Kontaktstifte sowie ausgebaute und nicht ausgebaute Prüfadapter. Diese finden ihren Einsatz in Prüfgeräten der Elektronikindustrie. Dort werden diese benötigt, um die verschiedenen Funktionen von elektronischen Leiterplatten zu testen. Zentrales Element der Produkte bilden gefederte Kontaktstifte, welche die Leiterplatte kontaktieren und über elektrische Impulse Informationen erhalten. Stets anspruchsvollere Prüfungsanforderungen, z.B. von Kunden aus der Automobilindustrie oder der Kommunikationstechnologiebranche, fordern vom Konstanzer Prüfmittelbauer die stetige Weiterentwicklung der Prüfsysteme sowie die kontinuierliche Einführung neuer Produkte, wie Thomas Schrodi, Bereichsleiter Automation und Produktentwicklung bei Ingun, bestätigt: „Die Elektronikindustrie ist sehr dynamisch – die Produkte verändern sich in sehr hoher Frequenz was für uns zur Folge hat, dass die Vielfalt an Kontaktstiften kontinuierlich steigt. Während noch vor wenigen Jahren die Phase von der Zeichnungsfreigabe bis Auslieferung rund drei Monate betrug, liegt der Durchschnitt heute bei rund sechs Wochen. Damit wir auch weiterhin auf die Kundenbedürfnisse eingehen können, ist Flexibilität, Schnelligkeit sowie höchste Qualität und Präzision in der Produktion gefordert.“ Denn nicht nur die Produktlebenszyklen werden immer kürzer, auch der Trend zur Miniaturisierung verstärkt sich. Die Elektronik wird immer kleiner, wodurch die Anforderungen an eine präzise Messung zunehmen.
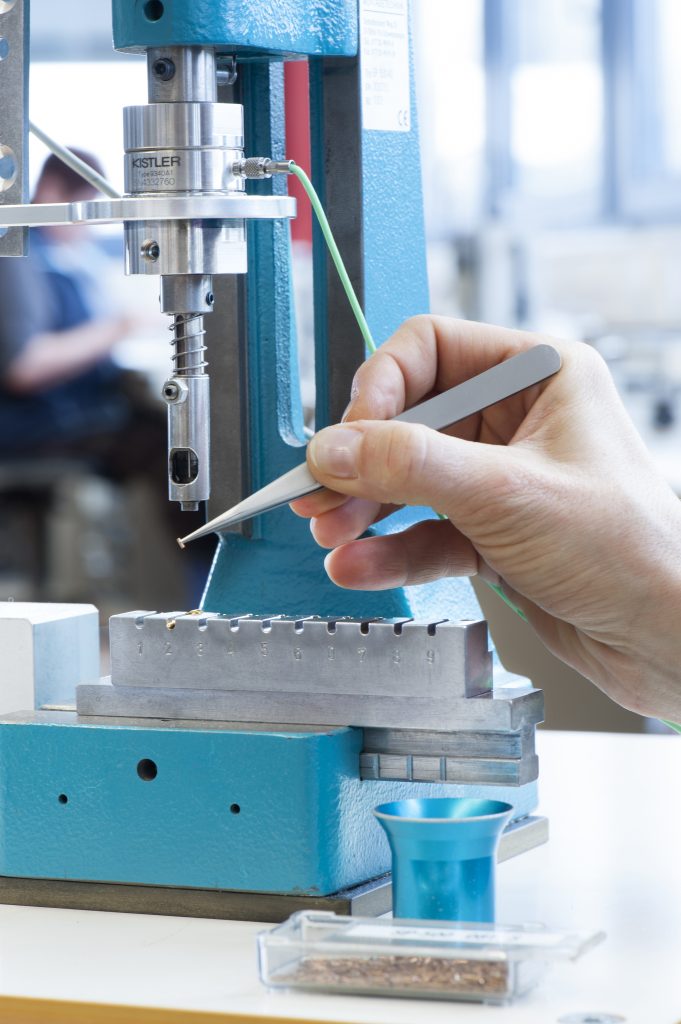
Kraftsensoren und Überwachungssysteme
Auch für Klaus König, der bei Ingun seit mittlerweile acht Jahren an der Entwicklung von Vorrichtungen und Automaten arbeitet, steht das Thema Qualität im Fokus. Ihm zufolge bilden die Sensoren und Systeme von Kistler eine wichtige Rolle, um eine präzise und wiederholgenaue Prüfung der elektronischen Baugruppen sicherzustellen: „Um die Federkraft in den Stiften möglichst genau zu messen, setzt unser Unternehmen seit 20 Jahren erfolgreich auf die Messtechnologie von Kistler. Denn nur wenn die Kontaktstifte einwandfrei funktionieren können wir die Qualität unserer hochpräzisen Prüfsysteme gewährleisten“. Aufgrund der kürzer werdenden Produktlebenszyklen wurden die Zeitfenster innerhalb der Produktion immer enger. Thomas Schrodi erklärt: „Kunden fordern heute eine viel kürzere Produkteinführungszeit. Deshalb ist es nicht mehr möglich, bis zu einem Dreivierteljahr auf eine neue Produktionsanlage zu warten. Seit vier Jahren wird daher der Anlagenbau, der für die Produktion der Kontaktstifte benötigt wird, in-house realisiert.“ Dieser Schritt brachte Ingun ein hohes Maß an Flexibilität. Indem Maschinenbau als Kernkompetenz ins Unternehmen integriert und damit auch das Produktions-Know-how ins Haus geholt wurde, können neue Produktionsanlagen viel schneller und individueller aufgebaut werden. In Anbetracht der großen Produktvielfalt ist diese Flexibilität im Produktionsprozess für das Unternehmen von besonderer Bedeutung. Aktuell besitzt Ingun vierzehn automatisierte Anlagen auf denen die Kontaktstifte gefertigt werden. Jedes Jahr kommt eine neue Anlage hinzu. In den Anlagen erfolgt die Fertigung in mehreren Schritten. Jeweils im letzten Schritt wird der Kontaktstift mit den Kistler Sensoren geprüft. Die Anlagen sind mit Kraftsensoren vom Typ 9217A bzw. 9340A1 sowie mit je einem maXYmos Überwachungssystem ausgerüstet. Durch die Kraft-Weg-Überwachung wird jeder einzelne Kontaktstift am Ende der Produktion auf Funktionalität geprüft. Die Integration der Qualitätskontrolle in den automatisierten Fertigungsprozess stellt sicher, dass Schlecht-Teile direkt aus der Produktion ausgeschlossen werden. Auch in der manuellen Produktion, in der kleine Serien montiert werden, kommen maXYmos BL mit Sensoren des Typs 9340A1 zum Einsatz. So wird sichergestellt, dass auch in der manuellen Produktion 100% Qualität gewährleistet werden kann. „Für uns hat dies den Vorteil, dass wir sowohl in der manuellen als auch automatisierten Produktion ein und dieselbe Qualitätsprüfung implementiert haben. Wir haben mit dem maXYmos BL ein System gefunden, dass sich dank der intuitiven Bedienoberfläche einfach programmieren lässt und uns auf einen Blick verrät ob Gut- oder Schlechtteile produziert werden.“ so Klaus König.
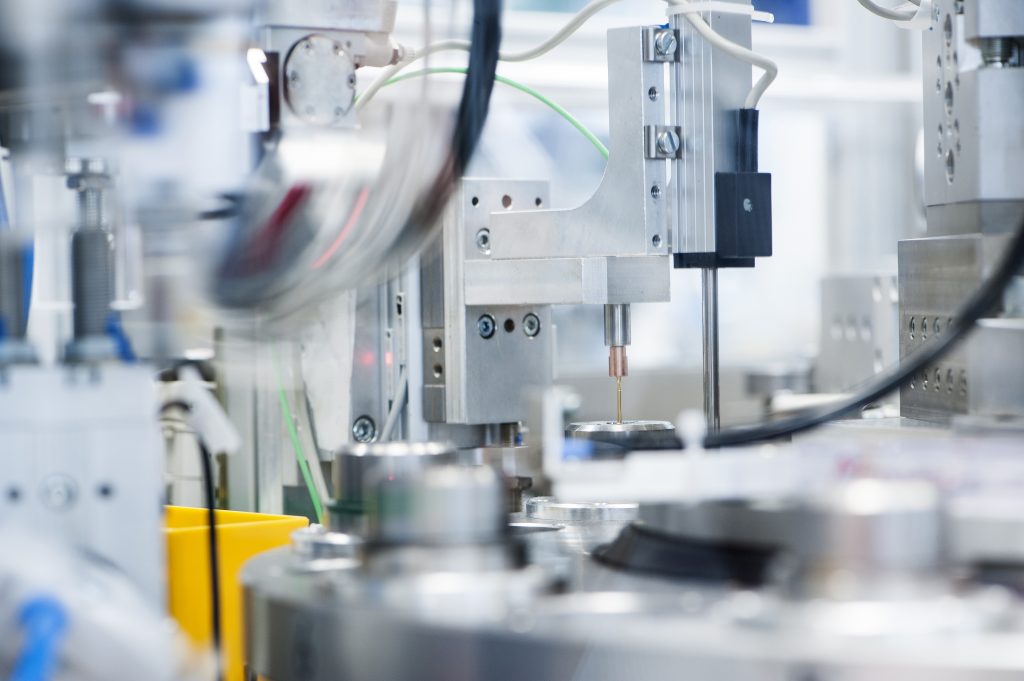
40 Millionen Stifte pro Jahr
Mit den Anlagen des Prüfmittelbau Spezialisten werden pro Jahr 40Mio. Stifte produziert, d.h. in jeder Maschine werden, abhängig vom Schichtmodell, 3 bis 8Mio. Stifte gefertigt. Um diese hohen Stückzahlen zuverlässig zu erreichen, müssen alle Maschinen eine extrem hohe Taktung fahren. Um eine weitere Frequenzsteigerung zu ermöglichen, überlegt sich die Entwicklungsabteilung von Ingun längerfristig eine komplette Integration der Qualitätssicherung in den wertschöpfenden Prozess. Hierzu bieten die piezoelektrischen Kraftsensoren wiederum eine wichtige Basis: Die winzigen Sensoren messen mit kleinsten Krafteinleitungsflächen auch bei kleinsten Platzverhältnisse präzise, wiederholgenau und mit hoher Auflösung. Gleichzeitig sind die Sensoren auch bei hoher Taktung robust, überlastsicher und damit langlebiger als andere Sensoren.