- Risikoprioritätszahl (RPZ) = BxAxE:
Je höher die RPZ, umso grösser ist das Risiko, dass ein poten zieller Fehler auftritt.
- Abstellmaßnahmen:
Bei einer RPZ > 100 ist das Risiko nicht mehr tolerierbar und es sollten Abstellmaßnahmen eingeleitet werden, wobei zuerst mit den höchsten RPZ begonnen wird.
- Aber Achtung: Der Fokus liegt auf der Fehlervermeidung – sollten also Einzelbewertungen:
B höher als 7, A höher als 5 und E höher als 6 liegen, so sollten auch diese Auswirkungen untersucht werden, egal wie hoch letztlich die errechnete RPZ ist.
Das oben erwähnte Beispiel einer Ursache-Wirkungs-Kette ist in Abbildung 4 in ein mögliches FMEA-Formblatt übertragen.
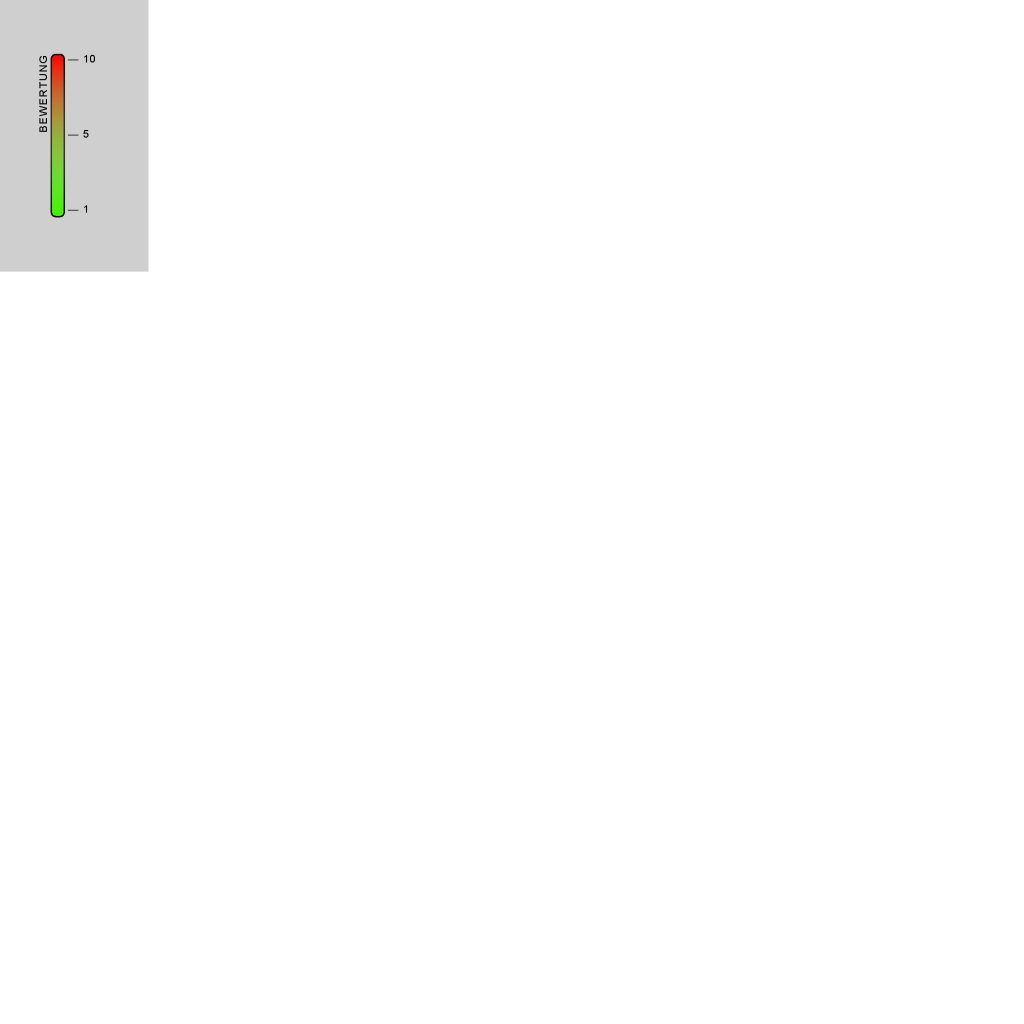
Auslöser für eine FMEA
Der Auslöser einer FMEA kann die Definition und Entwicklung eines neuen Produktes oder Prozesses sein, es kann aber auch die Verwendung des Produktes in einer neuen Anwendung oder die Einführung eines neuen Systems sein. Für die Überprüfung eines Produktes, Systems oder Prozesses mit einem niedrigen Neuigkeitsgrad bei Änderung empfiehlt sich eine verkürzte Form, die Methode Design Review based on Failure Mode – DRBFM.
FMEA-Varianten
Der Verband der Automobil Industrie (VDA) unterscheidet zwischen einem System-FMEA-Produkt und einem System-FMEA-Prozess, also zwischen den Produktmerkmalen, die von einem idealen Prozess ausgehen und den Produktionsprozessmerkmalen, die von einem ideal konstruierten Produkt ausgehen. In der Praxis wird das System-FMEA-Produkt meist in weitere FMEA unterteilt, wie z.B. bei einer Safety-Entwicklung zur Ermittlung der Diagnosefunktionen (diese spezifische FMEA wird im nächster Artikel im Detail diskutiert): Diese FMEAbauen aufeinander auf und geben jeder nachfolgenden FMEA Eingangsparameter (Abb. 5). Während eine System-FMEA – wie der Name bereits vermuten läßt – die Systemzusammenhänge analysiert, geht eine Design-FMEA auf die einzelnen Konstruktionsmerkmale ein. Abbildung 6 soll dies verdeutlichen. Eine Prozess-FMEA hat auf der obersten Ebene das Gesamtsystem bzw. das zu liefernde Produkt mit den Funktionen und Fehlfunktionen in Betrachtung. Auch die Anforderungen des Kunden an das Produkt im Zusammenhang mit dem Prozess, werden hier berücksichtigt. Auf der zweiten Ebene werden die einzelnen Prozess- bzw. Arbeitsplätze aufgeführt. Als Funktion bzw. Fehlfunktion sind hier die einzelnen Prozess- bzw. Arbeitsschritte je Station dargestellt, die durchgeführt werden müssen bzw. falsch ausgeführt werden können. Auf der dritten Ebene befinden sich folgende Einflussfaktoren nach Ishikawa – Mensch, Material, Maschine, Methode, Millieu (Umwelt): Anhand des genannten Beispiels soll auch dies in Abbildung 7 verdeutlicht werden.
Tipps und Tricks für die Durchführung einer FMEA
Um den Aufwand mittelfristig für eine FMEA zu reduzieren empfiehlt es sich für wiederkehrende Strukturelemente eine generische FMEA durchzuführen. Wiederkehrende Strukturelemente haben identische Funktion und identischen Aufbau. Diese generische FMEA kann dann für weitere Produkte herangezogen werden. Die übernommenen Umfänge sind bezogen auf den jeweiligen Anwendungsfall kritisch zu überprüfen, insbesondere die Bewertung mit den Erfahrungen aus der Anwendung. Es ist darauf zu achten, dass z.B. geänderte Parameter in der Dimensionierung nicht zu geändertem Verhalten führt.