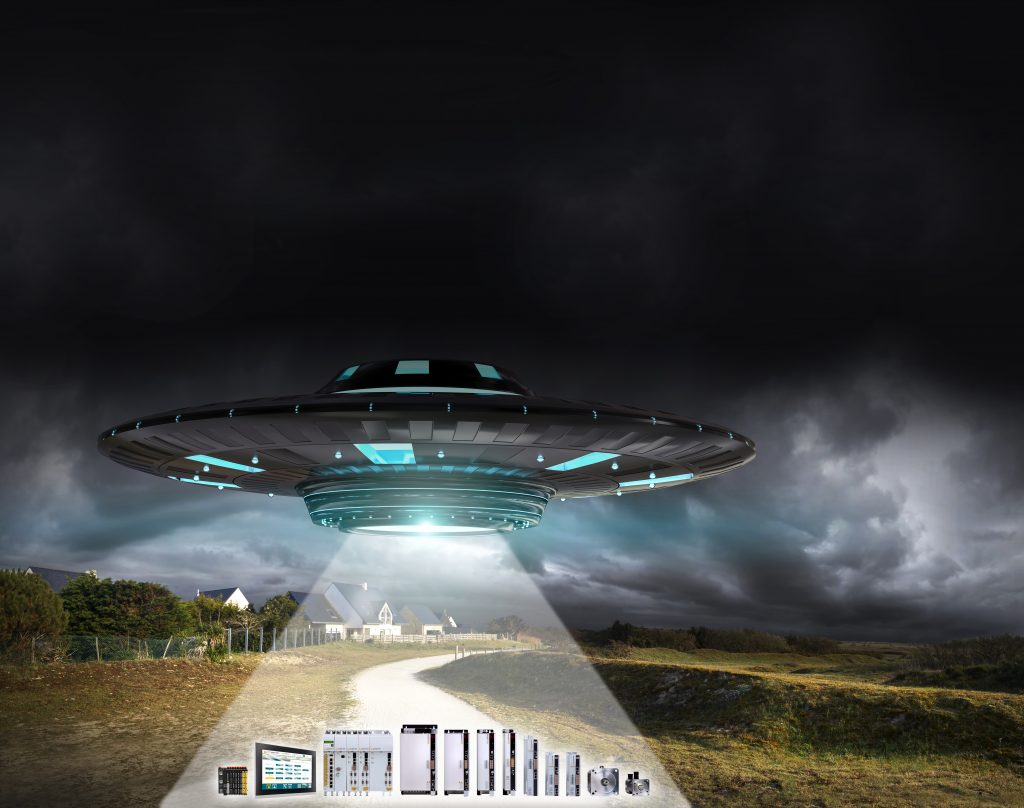
Die Auswahlkriterien für Automatisierungssysteme sind heute unterschiedlicher denn je. Auf der einen Seite vertraut der Maschinenbauer auf Lösungen aus einer Hand. Auf der anderen Seite will er größtmögliche Leistung und Funktionalität aus der Maschine herauskitzeln. Mit diesem Ziel wählt er bewusst Komponenten verschiedener Hersteller aus.
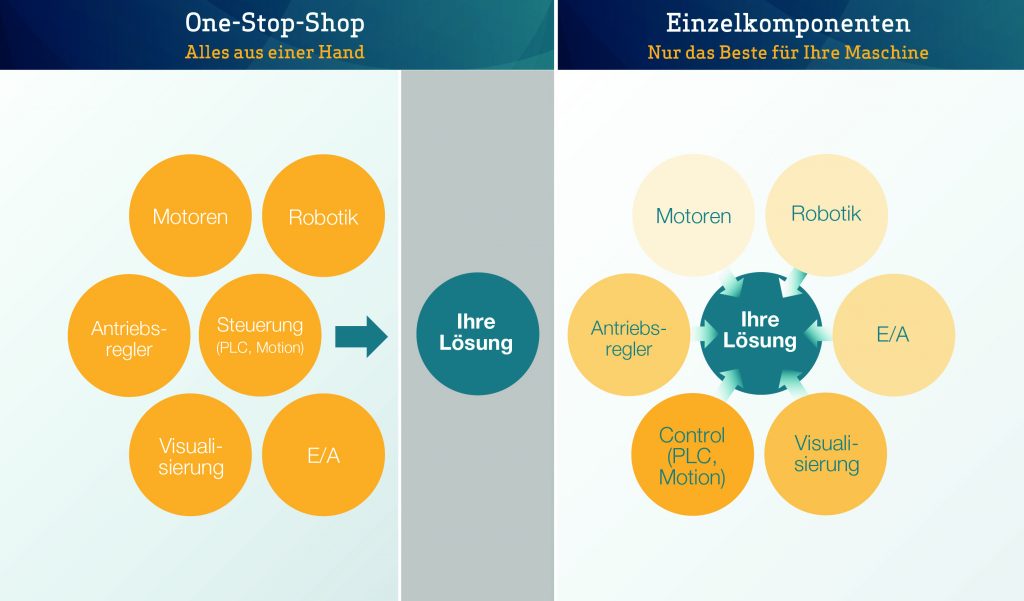
One-Stop-Shop oder das Beste verschiedener Welten?
Die One-Stop-Shop-Strategie vertraut darauf, dass nur ein Lieferant alle erforderlichen Automatisierungskomponenten im Portfolio hat. Vorteilhaft und selbstverständlich ist es, dass alle Teile miteinander kompatibel sind und so ein schnelles Plug&Play gewährleistet ist. Die Integration von Drittanbieterkomponenten ist dann aber aufwändig – wenn überhaupt möglich. Das Ergebnis liegt häufig in einem Kompromiss aus Preis und Performance der Maschine. Ein flexibles Automatisierungsportfolio bietet dagegen die gewünschte Offenheit für eine ziel- und prozessorientierte Maschinenautomatisierung. Durch die Möglichkeit, das bestmögliche System aus den leistungsstärksten Komponenten verschiedener Hersteller zusammenzustellen, kann der Anwender eine außergewöhnliche Maschinenperformance erreichen und behält zudem seine Unabhängigkeit. Dafür müssen die Produkte aber einfach und schnell integrierbar sein – sowohl als Komponente als auch als Teilsystem.
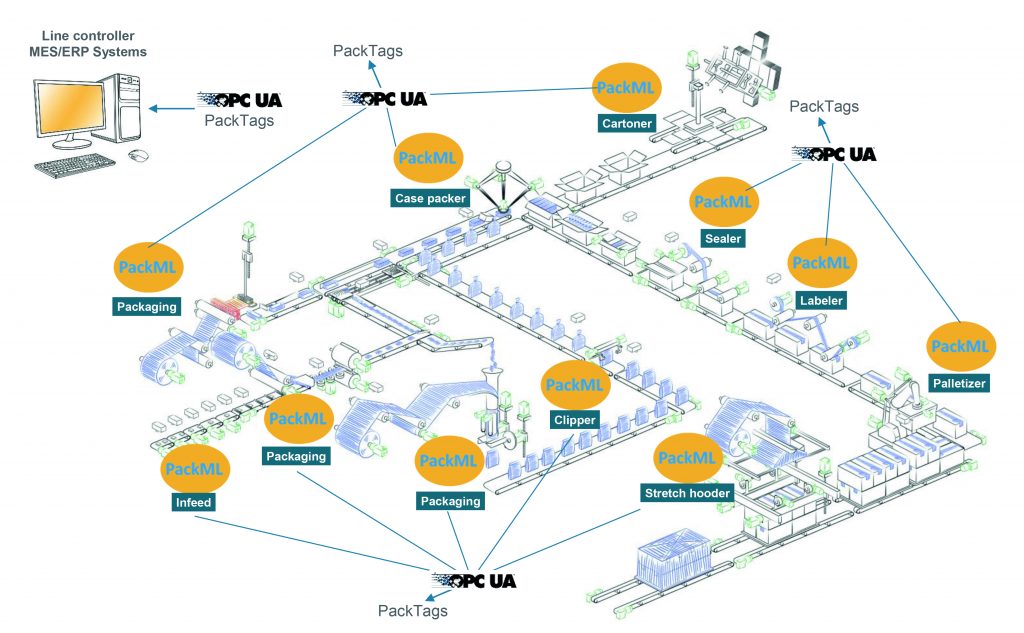
Die Antriebstechnik erhöht den Mehrwert
In der Maschine setzen Antriebe die Steuersignale in die gewünschte Bewegung um. Präzision oder Dynamik sind dabei zwei wichtige Schlagworte, um im Ergebnis einen idealen Be- oder Verarbeitungsprozess zu realisieren. Häufig ist die Maschinensteuerung etabliert oder durch Endkundenvorschriften gesetzt. Die Antriebe des Systempartners erfüllen aber nicht immer die spezifischen Anforderungen. Offene Antriebs- und Servosysteme bieten hier eine attraktive Alternative. Die Systemintegration erfolgt schnell mit einer auf die jeweilige Steuerung abgestimmten Gerätebeschreibungsdatei. Kommuniziert wird mit standardisierten Feldbussen wie Ethercat bzw. Profinet oder klassischen Systemen wie CANopen oder Profibus. Standardisierte Bewegungsprofile lassen Steuerung und Antrieb eine Sprache sprechen. Spezialmotoren sind für kompakte und effiziente Maschinen das Salz in der Suppe:
- Trommelmotoren werden platzsparend in die Transportstrecke eingebaut.
- Torquemotoren bewegen Prozesse verlustoptimal und spielfrei.
- Linearmotoren steigern durch ihre dynamischen Eigenschaften die Performance der Maschine.
Moderne Antriebsregler beherrschen den Betrieb dieser Motoren genauso einfach wie den von Servomotoren. Ein Autotuning stellt alle Parameter schnell und zuverlässig ein. Die Anpassung an die Bewegungsaufgabe erfolgt mit grafischen Bedienelementen. Das offene Multimotor-Interface wertet zudem eine Vielzahl von Gebersystemen aus. Hochauflösende Systeme in Ein- und Zweikabeltechnik sind ebenso möglich wie der klassische Resolver oder Hallsensoren.
Der Antrieb als Industrie-4.0-Datenquelle
Im Zeitalter von Industrie 4.0 wird der Wunsch nach einem ‚Antriebssystem als Sensor‘ zur Realität. Predictive Maintenance oder Condition Monitoring sind nur möglich, wenn der Antrieb die erforderlichen Daten sammelt und sie der Maschinen- und Liniensteuerung übermittelt. Unterschiedliche Konzepte werden diskutiert: Ist der Antrieb nur Datensammler oder ist bereits eine Analyse der Daten erforderlich? Trotz der enormen Bandbreite heutiger Feldbusse ist das Übertragen aller Daten nicht immer möglich. Hier schlägt die Stunde des intelligenten Antriebs. Er wertet alle Daten nach definierten Mustern aus und versendet nur den Status. Eine im Antrieb integrierte SPS bietet dabei ein hohes Maß an Flexibilität. Sie setzt die individuelle Prozesskenntnis des Maschinenbauers in Algorithmen um, die lediglich das Ergebnis darstellen. Damit entlastet die SPS den Feldbus und die Maschinensteuerung. Das Know-how des Anwenders bleibt gewahrt, da er den Ablauf in Eigenregie definieren, programmieren und testen kann.