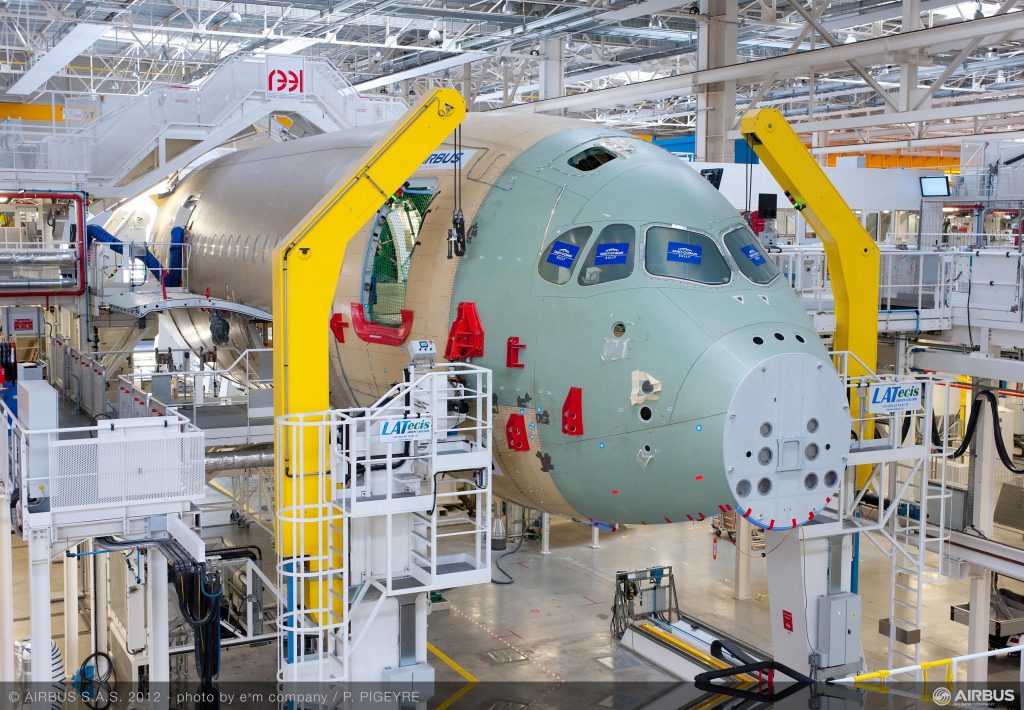
Der Rumpf des A350 XWB besteht aus drei Hauptteilen (vorne, Mitte und hinten). Diese werden an der ersten Hauptmontagestation P50 miteinander verbunden und das Fahrwerk angebaut. Danach wird der Rumpf zur Station P40 überführt, wo die Montage der Flügel und des Hecks erfolgt. Der Prozess der Paarung und der Verbindung großer Flugzeug-Baugruppen ist eine komplexe Aufgabe, da Gravitations- und Umgebungsbedingungen geometrische Verformungen verursachen. Dies gilt speziell für Bauteile aus kohlefaserverstärktem Polymer (CFRP), die weitgehend für den A350 XWB eingesetzt werden.
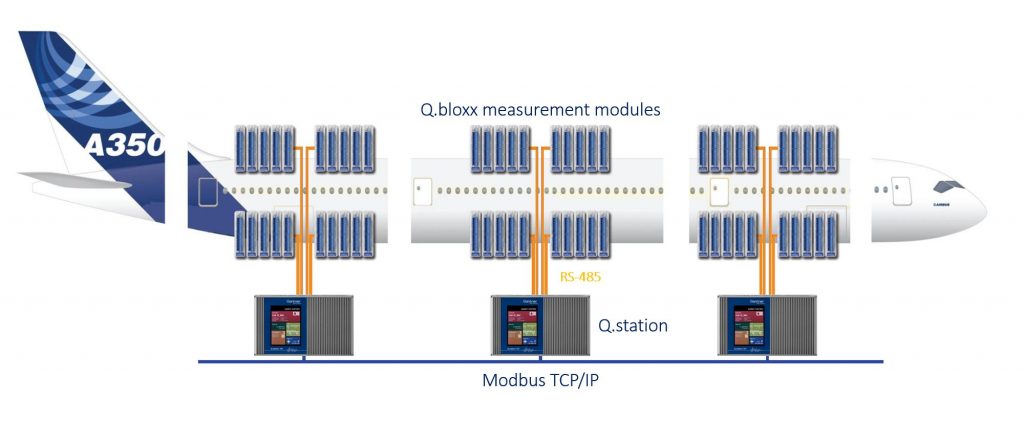
Synchrone Überwachung von Verformungen
Um die Herausforderungen der Lokalisierung und Positionierung großer Flugzeugsegmente zu bewältigen, wird ein messtechnisch unterstütztes Montagesystem verwendet. Eine Reihe von Mehrachsen-Positioniersystemen heben, bewegen und richten die Rumpf- und Flügelstrukturen aus, um eine optimale Passform zu gewährleisten. Der Schutz der großen Strukturen bei der Verarbeitung ist dabei von größter Bedeutung. Mithilfe von Wägezellen, die im Antriebsmechanismus des Stellungsreglers montiert sind, werden die auf den Aufbau wirkenden Kräfte während der Bewegung überwacht. Dies gewährleistet eine spannungsfreie Handhabung und verhindert so die Beschädigung der Teile. Darüber hinaus werden geometrische Verformungen überwacht und kompensiert, so dass eine Verbindung ohne Beanspruchung durch mechanische Spannungen der Flugzeugteile gewährleistet ist. Das gesamte Montagesystem umfasst 300 Wägezellen. Einachsige Wägezellen überwachen das Heben (Fz) und triaxiale Wägezellen überwachen die Kraft während der Montage (Fx, Fy und Fz). Alle Wägezellen haben DMS-Doppelbrücken, um eine Redundanz im System zu ermöglichen. Die Wägezellen sind an ein Messsystem der Reihe Q.bloxx angeschlossen. Zur Durchführung der primären Kraftüberwachungsaufgaben werden insgesamt 150 Q.bloxx-A101-Module verwendet. Zusätzlich werden 300 Q.bloxx-A102-Module für die redundante Überwachung eingesetzt.
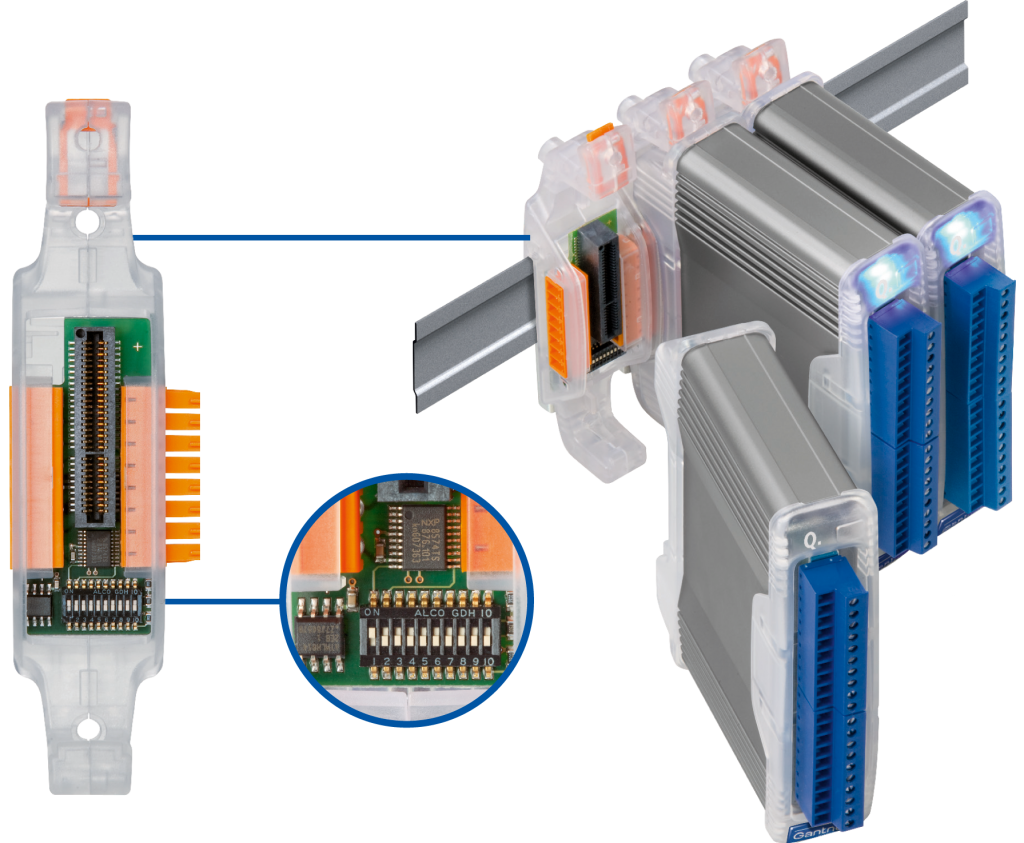
Datenübertragung bis zu 24MBaud
Der Abstand zwischen einer Wägezelle und einem Überwachungssystem kann bis zu 75m betragen. Die Anordnung der Messmodule nahe den tatsächlichen Messpunkten ist eine der Hauptanforderungen bei der Planung eines messtechnisch unterstützten Montagesystems. Die optimale Kanal-Granularität der Messmodule, kombiniert mit der Flexibilität, Module frei zu mischen und zu verteilen, bietet Airbus maximale Flexibilität. Die dezentralen Messmodule kommunizieren über die RS-485 Schnittstelle mit einem Q.station-Test-Controller. Dieser übernimmt alle Datenerfassungs-, Synchronisations- und Steuerungsaufgaben. Die Datenübertragung erfolgt mit mit einer Baudrate von bis zu 24MBaud. Trotz des dezentralen Aufbaus sind die Messungen aller Messkanäle untereinander synchron mit einem Jitter kleiner als 11µs. Diese Architektur garantiert zuverlässige Messergebnisse in einem industriellen Umfeld und vermeidet Kabelkomplexität. Das Montage-Überwachungssystem umfasst eine Schneider Electric Safety SPS. Der Open-Architecture-Test-Controller kommuniziert mit der Safety SPS über Modbus TCP/IP. Durch die Trennung des Q.station-Test Controllers von den Messmodulen wird die Kommunikation und Interoperabilität mit dem Monitoring-System deutlich optimiert. Darüber hinaus, da Schnittstellen- oder Leistungsanforderungen weiterentwickelt werden, ist es für Airbus einfach, den Controller allein zu aktualisieren, so dass ein Großteil der Systeminvestition erhalten bleibt und zukunftssicher ist.
Messmodule mit Hot-Swap-Funktion
Die Q.bloxx-Module verfügen über On-Board-Mikroprozessoren, 24-Bit-A/D-Wandler, Anti-Aliasing-Hardware-Filter und eine galvanische Trennung der Kanäle untereinander, zur Versorgung und zur Schnittstelle mit einer Isolationsspannung von bis zu 500VDC. Die Messmodule unterstützen Abtastraten von bis zu 100kHz pro Kanal. Jedes Modul verfügt über ein FPGA, das eine vollständige Signalaufbereitung und Datenverarbeitung an der Stelle ermöglicht, an der die Sensordaten in das Messsystem gelangen, was die Netzwerkbelastung enorm reduziert. Nur prozessrelevante Informationen, wie Mittelwert, Min/Max und Spitze-Spitze-Messung, werden an das Montage-Überwachungssystem gesendet. Dies vermeidet die Netzwerk-Latenz und verbessert die Reaktionszeiten. Die Flugzeugmontage kann bis zu 40 Prozent der gesamten Flugzeugherstellungskosten ausmachen. Die betriebliche Verfügbarkeit des Montagesystems ist daher von größter Bedeutung. Jedes Q.bloxx-Modul verbindet sich mit einem Sockel mit eingebautem Flash-Speicherchip. Eine Kopie der gesamten Modulkonfiguration wird im Sockel gespeichert. Wenn ein defektes Modul ausgetauscht wird, besteht somit keine Notwendigkeit, das neue Modul oder das Überwachungssystem manuell neu zu konfigurieren. Module können ausgetauscht werden, während sie im eigentlichen Betrieb sind, ohne dass die Stromversorgung unterbrochen werden muss. Das System benötigt 5sec, um die Konfiguration vom Sockel in das neue Modul zu klonen. Die Messung wird automatisch fortgesetzt, wenn die Konfiguration wiederhergestellt wurde.