
Die Simulationssoftware steht dabei als Middleware im Zentrum und fungiert als eine bereichsübergreifende Plattform, auf der zu jedem Zeitpunkt der aktuelle Entwicklungsstand verifiziert und auf Realisierbarkeit mit weiteren Bereichen überprüft wird. Dabei greifen die Fachbereiche Mechanik, Elektrik und Software zeitgleich auf dieselben Modelle zurück, die sie jeweils in ihrer nativen Entwicklungsumgebung bearbeiten, gemeinsam weiterentwickeln und mittels der Simulation sofort im Zusammenspiel testen. So wird der aktuelle Entwicklungsstand in der Mechatronikentwicklung bereits in den frühen Phasen des Prozesses interdisziplinär und kontinuierliche getestet – in Form einer kontinuierlichen virtuellen Inbetriebnahme in kleinen Schritten. Dieser ganzheitliche Entwicklungsansatz ermöglicht, dass zahlreiche Aufgaben im Engineering vorgezogen werden, angefangen bei der Auslegung von Maschinen inklusive dynamischer Bewegungs- und Antriebskinematik bis hin zur virtuellen Inbetriebnahme mit der realen Steuerung. Durch eine kontinuierliche virtuelle Inbetriebnahme lässt sich der Aufwand gegenüber der üblicherweise finalen Inbetriebnahme also deutlich reduzieren – sowohl zeitlich als auch kostentechnisch. Denn durch den permanenten Abgleich des Arbeitsstandes werden jederzeit Machbarkeit und Erreichbarkeit der Ziele überprüft, eine stets konsistente Entwicklung ist realisierbar. Die Inbetriebnahmezeiten am Ende reduzieren sich so drastisch um bis zu 75 Prozent und auch eine deutliche Kostenersparnis sowie eine Verkürzung der Durchlaufzeiten um bis zu 15 Prozent ist durch den Einsatz von Simulationssoftware möglich.
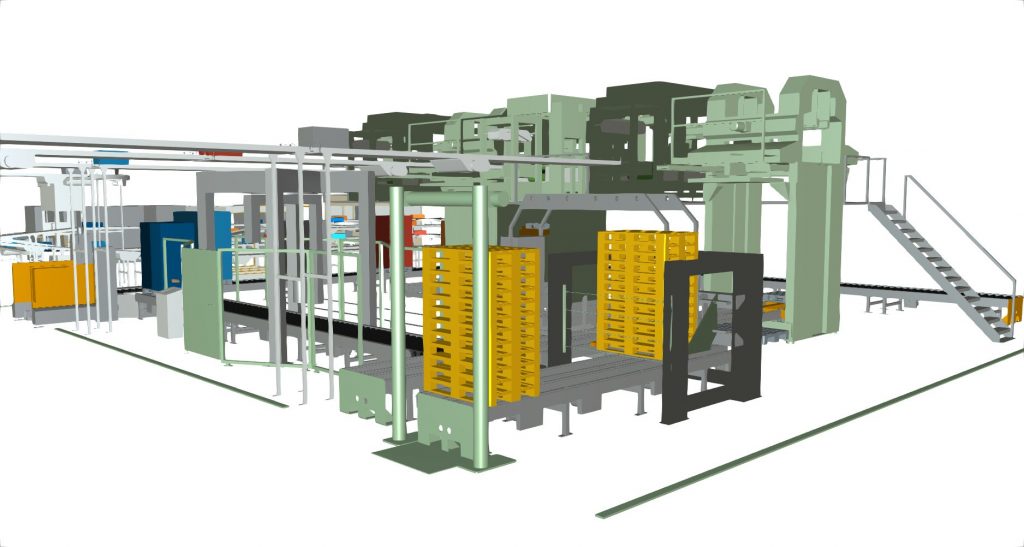
Von der Entwicklung bis zur Inbetriebnahme
Damit eine Simulationssoftware als bereichsübergreifende Plattform gewinnbringend zum Einsatz kommt, ist es erforderlich, alle gängigen Systeme und native Entwicklungsumgebungen über stabile Schnittstellen zur Verfügung zu stellen. Das Unternehmen Machineering hat mit Industrialphysics eine solche Plattform geschaffen. Mit der ersten Idee zur Konstruktion der späteren Maschine werden alle generierten Daten bidirektional mithilfe einer Schnittstelle vom CAD-System in die Simulationssoftware übertragen. Der große Vorteil liegt darin, dass Änderungen am simulierten Modell unmittelbar auch im CAD-System zur Verfügung stehen. Somit entfällt das redundante Ändern des Modells und allen Mitgliedern des mechatronischen Teams steht jederzeit die aktuelle Version als Arbeitsgrundlage zur Verfügung. Die Software Industrialphysics verfügt über Schnittstellen zu gängigen CAD-Systemen wie SolidWorks, Inventor, Solidegde, Pro/E und auch IronCAD. Neben der Anbindung der diversen CAD-Systeme sind verschiedene interne und reale Steuerungen über TCP/IP oder auch über Feldbussysteme wie Profinet oder Ethernet/IP angebunden, z.B. von Beckhoff, Siemens, B&R, Schneider Electric, Rockwell, Bosch Rexroth. Zudem verfügt Industrialphysics über eine Eplan-Schnittstelle. Darüber hinaus steht den Nutzern eine Roboterbibliothek zur Verfügung sowie die integrierte Anbindung realer Robotersteuerungen Kuka, ABB oder Stäubli. Mithilfe der Vielzahl der angebundenen Systeme und Steuerungen übernimmt die Simulationsplattform eine komplett neue Rolle in der Mechatronikentwicklung. Weg von einer Überprüfung entlang einer Sackgasse zum Ergebnis hin zu einem Medium, das die unterschiedlichen Komponenten einer Maschine in einem artikulierbaren digitalen Prototyp zusammenführt.
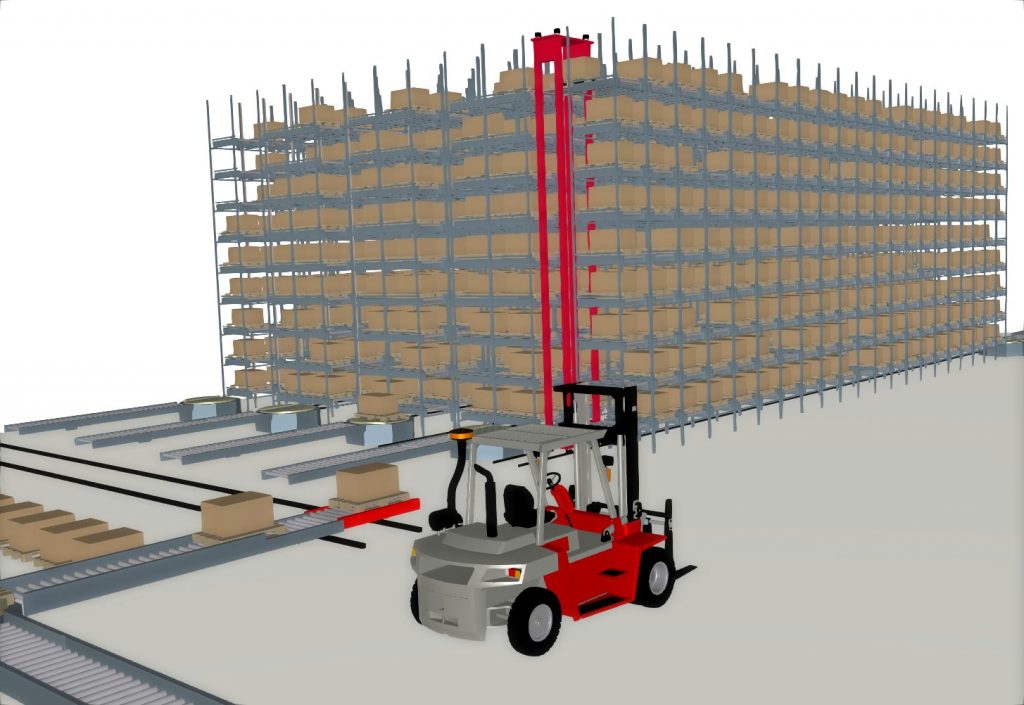
Simulation im laufenden Betrieb
Eine Simulationssoftware vereinfacht nicht nur den Entwicklungsprozesses. Auch im laufenden Betrieb unterstützt sie die Betreiber. Denn mithilfe der Software wird die Anlage jederzeit in Echtzeit simuliert dargestellt. Sollte es zu Störungen oder Problemen kommen, können diese schnell lokalisiert und behoben werden, ohne dass es zu langem Stillstand kommt. Auch bei geplanten Verbesserungen und Modernisierungen einer laufenden Anlage erleichtert Simulation das gesamte Vorgehen. Jede vorzunehmende Änderung kann im Vorfeld virtuell durchlaufen werden. So lassen sich unterschiedliche Szenarien testen und die beste letztendlich auf die reale Anlage übertragen. Das Risiko von Fehleinschätzungen reduziert sich deutlich. Auch hier überzeugt der marginale Stillstand und die damit verbundene Kosteneinsparung.
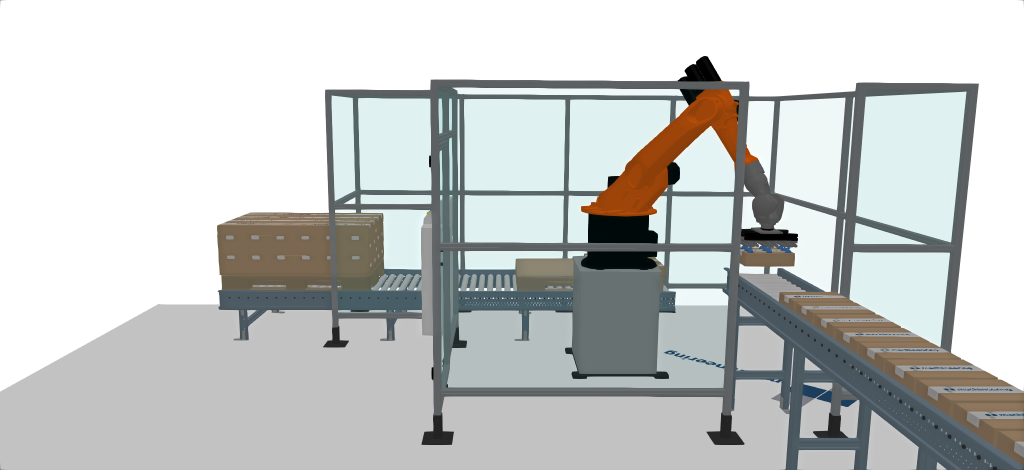
Neue Dimensionen durch Virtual und Augmented Reality
Machineering hat als einer der ersten Anbieter von Simulationssoftware verschiedene Virtual- bzw. Augmented-Reality-Brillen (VR bzw. AR) an die Simulation angebunden. Auf diese Weise können die Anwender von Industrialphysics tief in die visualisierte Anlage eintauchen. Bisher konnten die entsprechenden Maschinen, Anlagen oder Teile nur auf dem Bildschirm entwickelt, verbessert und überwacht, der Materialfluss überprüft und Störungen lokalisiert werden. Mit den VR- und AR-Brillen stehen jetzt zusätzliche Tools zur Verfügung, um noch dichter an die entsprechende Anlage heranzukommen. Neben dem Modell Oculus Rift steht auch die HTC Vive als VR-System mit Head-Mounted-Display zur Auswahl. Mit diesen Systemen ist der Anwender komplett von der Außenwelt abgeschnitten und bewegt sich frei im virtuellen Raum. Die Microsoft HoloLens dagegen basiert auf einem AR-System, also einer computergestützten Erweiterung der Realitätswahrnehmung. So kann der Benutzer mit der Unterstützung durch ein Natural User Interface interaktive 3D-Projektionen in der direkten Umgebung darstellen. Er sieht die Projektionen direkt, nimmt durch die transparenten Bildschirme aber trotzdem die Umgebung wahr. Die HoloLens besticht dabei durch hochauflösenden Projektionen mit projizierten Lichtpunkten. Sie basieren bei Anbindung an Industrialphysics auf realen Daten und sind nicht nur einfache Hologramme. Interaktionen mit weiteren Betrachtern sind durch die uneingeschränkte Reichweite und die Wahrnehmung der Umgebung möglich. So können Anwender beispielsweise in einer leeren Industriehalle komplette Anlagen projizieren oder auch vor Austausch einer Anlage die geplante Anlage bereits vor Ort betrachten. Durch die schnelle Entwicklung in diesem Bereich lässt sich ein großer Schritt in Richtung Industrie 4.0 vollziehen.