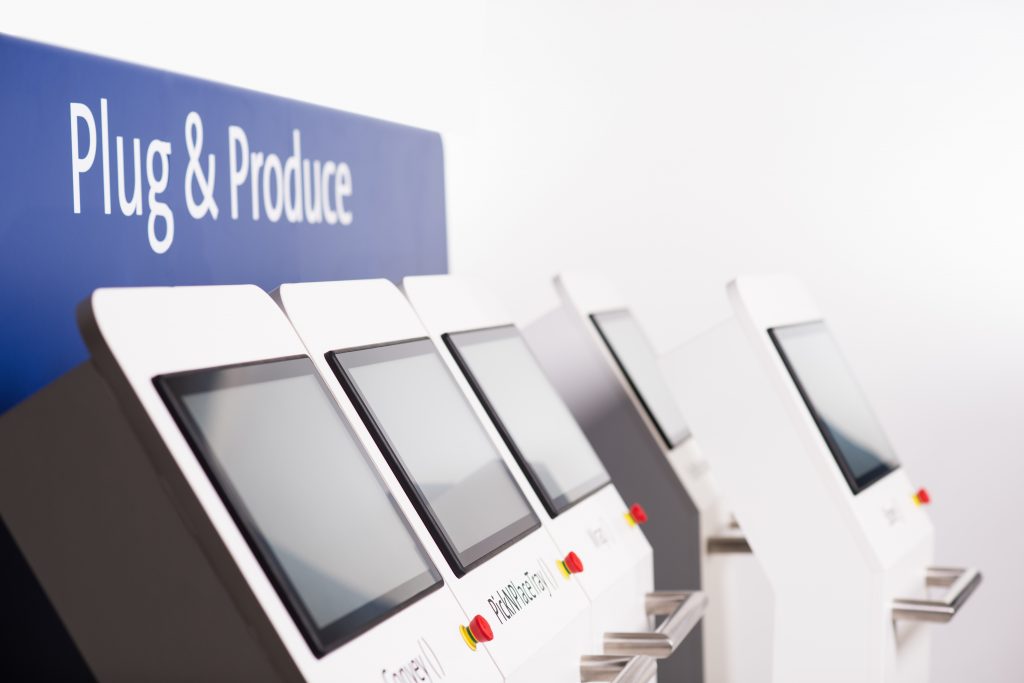
Im Fall eines Produkt- oder Formatwechsels auf einer Anlage sind nicht nur die mechatronischen Module der Maschine auszutauschen. Die Programmierung der Steuerung, das Einbinden in das HMI, Diagnose und Inbetriebnahme sind weitere notwendige Arbeitsschritte bis es zur Wiederaufnahme der Fertigung kommen kann. Das bedeutet hohen Zeit- und Personalaufwand beim Endanwender. Aber auch der OEM muss viel investieren, z.B. um die benötigten Anschluss-Optionen zu realisieren, unterschiedliche Daten oder Datenformate bereitzustellen und sich mit Lieferanten anderer Module abzustimmen.
Manuellen Aufwand vermeiden
Nach dem Plug&Produce-Konzept könnte die Produktionslinie aber schnell wieder einsatzfähig sein – ohne hohen manuellen Aufwand bei der Konfiguration und Programmierung. Dafür nötig sind standardisierte und herstellerübergreifend genutzte Schnittstellen. Auf der SPS IPC Drives 2018 hat Lenze an seinem Stand mit einer Demo-Anwendung gezeigt, wie die Zukunft aussehen kann. Der Showcase simuliert die Verpackung verschiedener Produkte mit unterschiedlichen Modulen in der Fertigungslinie. Der Schlüssel für Plug&Produce – also einfach einstecken und loslegen – liegt in der Kommunikation: Offene, herstellerübergreifende Standards müssen es allen beteiligten Modulen ermöglichen, automatisiert die Produktionslinie zu konfigurieren und untereinander Daten auszutauschen, bis hin zur vollständigen Interaktion im Zuge des Produktionsauftrages. Dann muss die Produktionslinie im Gegenzug nicht mehr programmiert werden.
Vorhandene Standards nutzen
Zu den im Demonstrator genutzten Standards gehört OPC UA und dessen Companion Specification PackML. Lenze nutzte aber auch die Industrie-4.0-Verwaltungsschale, um hierüber Daten zur Beschreibung der Maschinenfähigkeiten bereitzustellen. Auf dieser Basis können sich die Module automatisiert koppeln und das Zusammenspiel im Produktionsprozess organisieren. Ziel des Unternehmens ist es, dass für diese Anwendung ebenfalls herstellerübergreifende Standards geschaffen werden. Dafür engagiert sich Lenze in den Normungsgremien der Verbände und sucht Mitstreiter in der Industrie und unter den OEMs.
Vorteile für OEMs
Der Maschinenbau kann vom Plug&Produce-Konzept erheblich profitieren, denn einheitliche Schnittstellen und Standards vereinfachen die Modularisierung von Maschinen und Anlagen. Zugleich wird das geistige Eigentum des OEM geschützt, denn es muss kein Kern-Knowhow gegenüber Dritten offengelegt werden, um eine reibungslose Kommunikation und Vernetzung sicherzustellen. Der Integrations- und Programmieraufwand sinkt, auch die Integration von Visualisierungssystemen wird vereinfacht – das reduziert mögliche Fehlerquellen, liefert mehr Freiräume zur Entwicklung von Innovationen. Bessere Funktionalität bei kürzerer Time-to-Market und effektiverem Personaleinsatz stärkt zudem die Wettbewerbsfähigkeit.