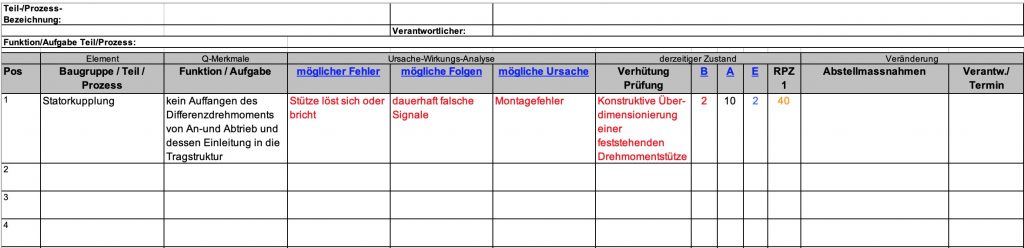
Der Einsatz von vorbeugenden Qualitätsinstrumenten verbessert die Produkt-/Prozessqualität und -zuverlässigkeit nachhaltig und wirkt möglichen Problemen vorzeitig entgegen. Diesen Satz finden wir in den meisten Qualitätshandbüchern, die Einführung und Umsetzung in der Praxis ist meist ein langwieriger Prozess mit einigen Stolpersteinen. Neben der FMEA kann die Qualitätsvorausplanung die Methodik QFD – Quality Funktion Deployment, die Kundenorientierung, die Methodik PO – Problemorientierung mittels PO-Matrix oder einen kompletten, aus dem Automotive-Umfeld kommenden Werkzeugkasten APQP – Advanced Product Quality Planning mit verbindlichen Plänen und Richtlinien enthalten.
Motivation Qualitätsvorausplanung und FMEA
Qualität kostet immer, keine Qualität kostet noch viel mehr. Die Kosten für die Fehlerbehebung am Produkt wachsen bei jedem Entstehungsschritt um den Faktor 10. Diese Aussage ist durch viele Untersuchungen bestätigt und seit langem akzeptiert. Kostet die Überprüfung eines Systemkonzeptes z.B. 1.000 Euro, kann für die Fehlerbehebung in der Entwicklungsphase bereits 10.000 Euro angesetzt werden. Wird ein potentieller Fehler beim Produktionsanlauf festgestellt, so schlägt dies bereits mit 100.000 Euro zu Buche. Tritt der Fehler erst beim Kunden auf, so ergeben sich für die Fehlerbehebung schnell siebenstellige Beträge. Aufwand und Geld sollte nicht zur Fehlerkorrektur in der Fertigung und im Feld eingesetzt werden, sondern für die Fehlervermeidung im Rahmen der vorbeugenden Qualitätssicherung, in der Entwicklung und Fertigungsvorbereitung! Jedoch ist nicht jeder Fehler gleichbedeutend in seiner Auswirkung und nicht jeder Fehler tritt in derselben Wahrscheinlichkeit auf. Hier kommt die FMEA – Fehlermöglichkeit und Eintrittsanalyse (im englischen Failure Mode and Effects Analysis) – ins Spiel.
Grundlagen der FMEA
Die FMEA dient der Erkennung der Fehlerorte, möglicher Fehler, deren Auswirkungen und derer zugrundeliegenden Ursachen. Das Ziel einer FMEA ist zum einen das präventive Erkennen der Zusammenhänge von potentiellen Fehlern, Ursachen und Folgen und die Priorisierung der Ursache-Wirkungs-Ketten bezüglich ihres Risikos. Zum anderen die präventive Einleitung von Abstellmaßnahmen für Ursache-Wirkungs-Ketten mit hohem Risiko. Oder mit anderen Worten, das gedankliche ‚Abklopfen‘ eines bestehenden/neuen Produktes oder Prozesses auf mögliche Schwachstellen – „Was könnte passieren?“ – „Was ist schon einmal in vergleichbaren Projekten/Prozessen passiert?“ – und die Sicherstellung, dass die gefundenen Schwachstellen eliminiert werden. Das grundlegende Prinzip einer FMEA ist die Verknüpfung eines Fehlers mit seinen Ursachen und Auswirkungen.
Risikopriorität
Dies soll an einem praktischen Beispiel aus der Antriebstechnik illustriert werden: Ein Drehgeber wird mit Hilfe einer Statorkupplung am Motor befestigt. Durch eine falsche Montage der Statorkupplung (Fehlerursache) kann sich die Statorkupplung lösen oder gar brechen (Fehler) und zu dauerhaft falschen Signalen (Fehlerfolge) führen. Die Bewertung der Ursache-Wirkungs-Kette erfolgt über die Risikoprioritätszahl RPZ. Diese ist die Multiplikation der Bedeutung der Fehlerfolgen aus Kundensicht (B), die Auftretenswahrscheinlichkeit eines Fehlers mit einer bestimmten Fehlerursache (A) und der Entdeckungswahrscheinlichkeit eines Fehlers mit einer bestimmten Ursache (E), wobei die Bewertung anhand eines Bewertungskataloges von 1 bis 10 erfolgt (Abb. 3).
- Risikoprioritätszahl (RPZ) = BxAxE:
Je höher die RPZ, umso grösser ist das Risiko, dass ein poten zieller Fehler auftritt.
- Abstellmaßnahmen:
Bei einer RPZ > 100 ist das Risiko nicht mehr tolerierbar und es sollten Abstellmaßnahmen eingeleitet werden, wobei zuerst mit den höchsten RPZ begonnen wird.
- Aber Achtung: Der Fokus liegt auf der Fehlervermeidung – sollten also Einzelbewertungen:
B höher als 7, A höher als 5 und E höher als 6 liegen, so sollten auch diese Auswirkungen untersucht werden, egal wie hoch letztlich die errechnete RPZ ist.
Das oben erwähnte Beispiel einer Ursache-Wirkungs-Kette ist in Abbildung 4 in ein mögliches FMEA-Formblatt übertragen.
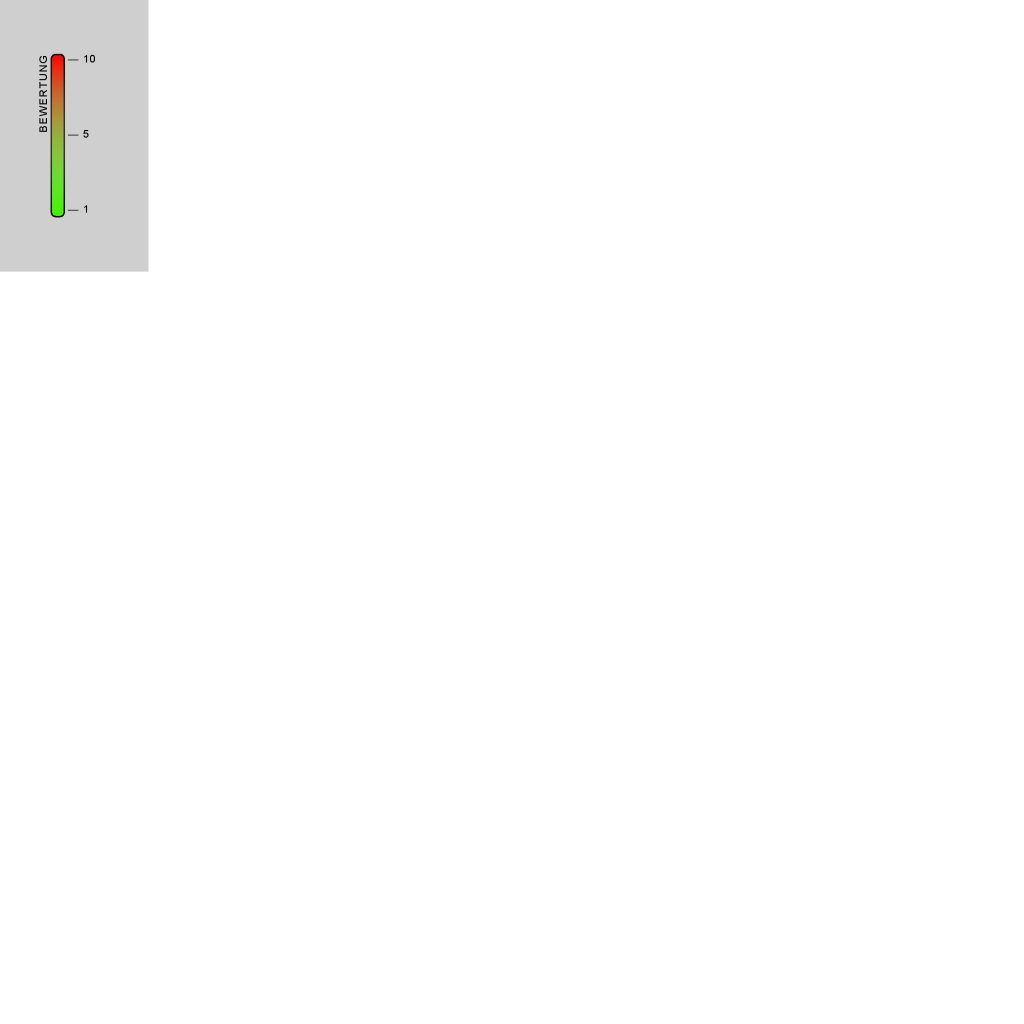
Auslöser für eine FMEA
Der Auslöser einer FMEA kann die Definition und Entwicklung eines neuen Produktes oder Prozesses sein, es kann aber auch die Verwendung des Produktes in einer neuen Anwendung oder die Einführung eines neuen Systems sein. Für die Überprüfung eines Produktes, Systems oder Prozesses mit einem niedrigen Neuigkeitsgrad bei Änderung empfiehlt sich eine verkürzte Form, die Methode Design Review based on Failure Mode – DRBFM.
FMEA-Varianten
Der Verband der Automobil Industrie (VDA) unterscheidet zwischen einem System-FMEA-Produkt und einem System-FMEA-Prozess, also zwischen den Produktmerkmalen, die von einem idealen Prozess ausgehen und den Produktionsprozessmerkmalen, die von einem ideal konstruierten Produkt ausgehen. In der Praxis wird das System-FMEA-Produkt meist in weitere FMEA unterteilt, wie z.B. bei einer Safety-Entwicklung zur Ermittlung der Diagnosefunktionen (diese spezifische FMEA wird im nächster Artikel im Detail diskutiert): Diese FMEAbauen aufeinander auf und geben jeder nachfolgenden FMEA Eingangsparameter (Abb. 5). Während eine System-FMEA – wie der Name bereits vermuten läßt – die Systemzusammenhänge analysiert, geht eine Design-FMEA auf die einzelnen Konstruktionsmerkmale ein. Abbildung 6 soll dies verdeutlichen. Eine Prozess-FMEA hat auf der obersten Ebene das Gesamtsystem bzw. das zu liefernde Produkt mit den Funktionen und Fehlfunktionen in Betrachtung. Auch die Anforderungen des Kunden an das Produkt im Zusammenhang mit dem Prozess, werden hier berücksichtigt. Auf der zweiten Ebene werden die einzelnen Prozess- bzw. Arbeitsplätze aufgeführt. Als Funktion bzw. Fehlfunktion sind hier die einzelnen Prozess- bzw. Arbeitsschritte je Station dargestellt, die durchgeführt werden müssen bzw. falsch ausgeführt werden können. Auf der dritten Ebene befinden sich folgende Einflussfaktoren nach Ishikawa – Mensch, Material, Maschine, Methode, Millieu (Umwelt): Anhand des genannten Beispiels soll auch dies in Abbildung 7 verdeutlicht werden.
Tipps und Tricks für die Durchführung einer FMEA
Um den Aufwand mittelfristig für eine FMEA zu reduzieren empfiehlt es sich für wiederkehrende Strukturelemente eine generische FMEA durchzuführen. Wiederkehrende Strukturelemente haben identische Funktion und identischen Aufbau. Diese generische FMEA kann dann für weitere Produkte herangezogen werden. Die übernommenen Umfänge sind bezogen auf den jeweiligen Anwendungsfall kritisch zu überprüfen, insbesondere die Bewertung mit den Erfahrungen aus der Anwendung. Es ist darauf zu achten, dass z.B. geänderte Parameter in der Dimensionierung nicht zu geändertem Verhalten führt.
FMEA Software Tools & Moderatorenkompetenz
Es gibt eine Vielzahl von bewährten FMEA Software Tools, von kostenfreien Produkten bis hin zu Produkten, die in ERP-Systemen wie SAP oder Oracle Financials integriert sind. Diese Werkzeuge haben durchaus Vorteile gegenüber einem Formblatt in einer Standard-Tabellenkalkulation. Neben der graphische Darstellung der Strukturelemente, sowie von Funktions- und Fehlernetz vereinfachen diese auch die teilweise generische Nutzung von bereits erstellten FMEA und es kann aus dem Werkzeug heraus ein Control Plan oder Prüfplan generiert werden. Allerdings gibt es kein Werkzeug, dass eine einfache, effiziente Bedienung erlaubt. Die Werkzeuge machen erst Sinn, wenn FMEA mindestens wöchentlich anstehen, es ausgebildete Vollzeit-FMEA-Moderatoren im Unternehmen gibt und die Methodik der FMEA im Unternehmen etabliert ist. Es empfiehlt sich erst in die Kompetenz von FMEA-Moderatoren zu investieren, FMEA Software Tools können Moderatorenkompetenz nicht ersetzen.
Wer soll an einer FMEA teilnehmen und wann soll diese stattfinden?
Eine FMEA ist grundsätzlich ein ganzheitlicher Ansatz, die Sicht des Kunden, der Entwicklung, der Betriebsmittelentwicklung, der Produktion und des Qualitätsmanagements sind gleichbereichtigt in einer FMEA-Sitzung vertreten.
- Die System-FMEA beginnt mit Vorliegen den Lastenheftes.
- Die Konzept-FMEA mit Vorliegen der Beschreibung der neuen Konzepte.
- Die Design-FMEA mit Vorliegen des detaillierten Designs.
- Die Prozess-FMEA kann mit Vorliegen des detaillierten Designs beginnen, spätestens jedoch mit Bestätigung des Designs im Entwicklungsprozess.
- Abschluss der FMEA ist die Freigabe zur Serienproduktion.
- Die FMEA bauen aufeinander auf und Punkte aus der jeweils vorgelagerten FMEA, die nicht aufgelöst werden können oder Verweise auf die nachfolgenden FMEAs beinhalten, müssen in die neuen FMEAs aufgenommen werden.
- Sollte zum Abschluss eines Meilensteins eine FMEA noch nicht final vorliegen, so empfiehlt sich eine eingeschränkte, konditionale Meilensteinfreigabe mit einem kurzen Zeitfester zur Nacharbeit.
Die FMEA-Dokumente sind während des Projektverlaufs lebende Dokumente bis zur Serienfreigabe.
Grundsätzliches zur FMEA-Moderation
- Der Moderator ist nicht derjenige der protokolliert.
- Der oder die Entwickler eines Bausteins, einer Baugruppe oder eines Gerätes sind nicht der Moderator oder derjenige der protokolliert.
- Der oder die Entwickler eines Bausteins, einer Baugruppe oder eines Gerätes sind nicht die ‚FMEA-Fragesteller‘, sondern diejenigen, die antworten.
- Der Moderator fragt solange nach, bis sowohl Fehlerbeschreibung, als auch Antworten präzise und spezifisch sind.
- Präzise Formulierung des Fehlers und der Ursache:
Falsch: Durchmesser nicht in Ordnung
Richtig: Durchmesser zu groß
Antwort Beispiel ‚falsch‘: „Wie bei den Standard-Produktmotoren.“
Antwort Beispiel ‚richtig‘: „Der Lagerabstand ist wie bei allen Motoren, die im Standardprogramm gefertigt werden. Die Anforderungen bezüglich Lagerlast an den Motor weichen nicht von den Lagerlasten der Standardmotoren ab. Wir haben eine zehnfache Überdimensionierung der Parameter und diese sind durch die Standard-Produktmotoren im Feld erprobt.“
Zusammenfassung und Fazit
Die theoretischen Grundlagen der FMEA zu erlernen ist nicht sonderlich schwer, gleichwohl gibt es bei der Einführung immer wieder erhebliche Hürden zu überwinden. Die größte Hürde ist hier die Mentalität der einzelnen Entwickler, aber teilweise auch die der Abteilungsleiter und der Geschäftsführung.
- Die Mitarbeiter in den entsprechenden Abteilungen müssen sich intensiv mit der Methode beschäftigen, sehen jedoch oft keinen unmittelbaren Nutzen.
- In der Anfangsphase entstehen hohe Kosten und kaum sichtbare Verbesserungen.
- Die erzielten Einsparungen bzw. die erzielten Umsatzsteigerungen kommen erst bei laufender Produktion, bzw. beim Kunden zum Vorschein und sind sehr schwer messbar.
Werden Qualitätsfehlerkosten im Feld, in der Produktion, in der Entwicklung, im Qualitätswesen erfasst, werden die ‚Feuerwehreinsätze‘ quantitativ ausgewertet, so kann sich schnell das Bewusstsein im Unternehmen für eine Qualitätsvorausplanung und damit auch für eine FMEA einstellen. Die FMEA ist eine etablierte Methode, die im Markt verbreitet ist. Ein Unternehmen, dass diese Methode etablieren möchte, kann auf die Erfahrungen anderer aufbauen, sei es durch neue Mitarbeiter mit dem notwendigen Erfahrungshintergrund oder durch externe Beratung. Es empfiehlt sich jedoch nicht, die Methodik anhand ‚Lehrbuchwissen‘ zu etablieren und die notwendigen Praxiserfahrungen außer Acht zu lassen. Die Methoden der vorbeugenden Qualitätssicherung verursachen zwar kurzzeitig Kosten, schaffen jedoch langfristig durch eine Reduktion der Fehlleistungskosten weitaus höhere Einsparungspotentiale. Sie helfen ‚Feuerwehreinsätze‘ zu reduzieren und dadurch Mitarbeitereinsatzplanungen zuverlässiger zu machen. Sie fördern den Ruf des Unternehmens am Markt.