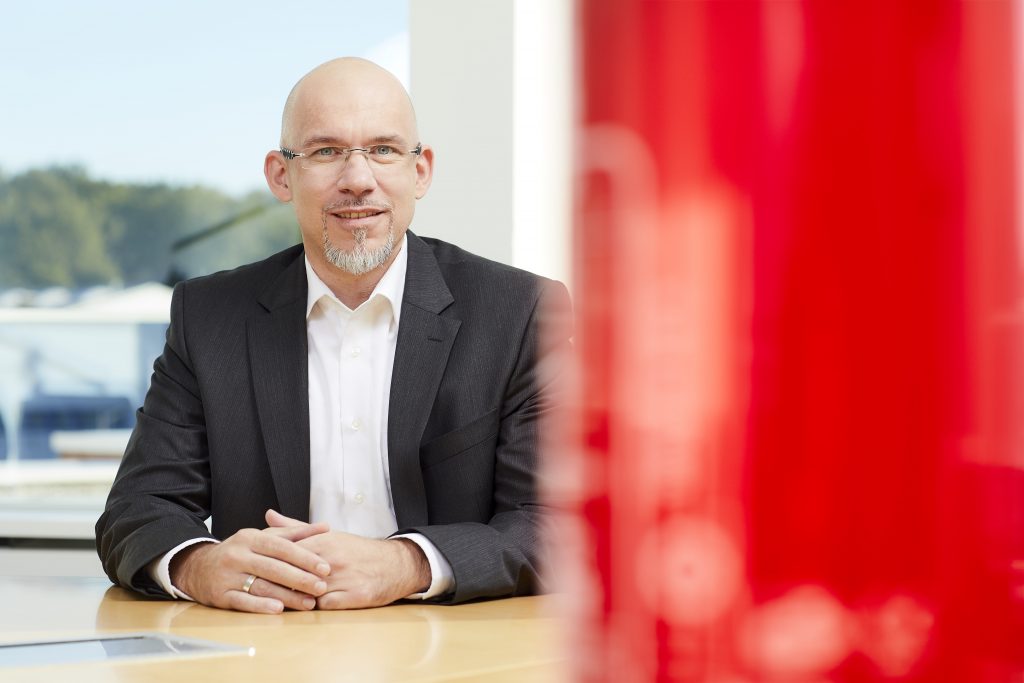
Brauchen wir wirklich einen weiteren Datenstandard?“ Diese oder ähnliche Fragen kommen häufig aus der Industrie, wenn das Stichwort Eplan Data Standard fällt. Sollte im Zeitalter der Standardisierung und Industrie 4.0 diese Aufgabenstellung nicht längst gelöst sein? Schaut man den Markt genau an, finden sich beim Blick auf Gerätedaten heute diverse Klassifizierungsstandards wie eCl@ss Advanced, ETIM und andere. Alle haben eines gemeinsam: Sie kategorisieren die Geräte in unterschiedlichen Klassen und beschreiben auf dieser Ebene mit Merkmalen, welche Informationen ein Gerät mitbringen sollte. Gepaart mit einer Formatbeschreibung bringen diese Standards die notwendige Grundvoraussetzung mit, um Gerätedaten herstellerneutral und systemunabhängig zu beschreiben.
Informationen ja, aber welche?
Damit solche Datenstandards ein möglichst breites Anwendungsspektrum finden, sind in der Regel eine Vielzahl von Informationen notwendig, um ein Gerät zu beschreiben. Bezogen auf das Engineering stellt sich die Frage: Wie unterstützen diese Standards den Konstrukteur ganz konkret im Engineering? Welche Daten werden in welchem Prozessschritt in Rahmen der Wertschöpfungskette benötigt? Und zu guter Letzt: Wie können diese Standards bestmöglich in den Eplan Lösungen genutzt werden?
Data Standard schließt Lücke
Genau hier kommt der neue Eplan Data Standard ins Spiel. Vorweggesagt: Er ersetzt keine existierenden Standards. Vielmehr ergänzt er diese um den Praxisbezug typischer Prozesse – etwa im Schaltanlagenbau. Klassisch beginnt ein solcher Prozess bei der Auswahl des Gerätes. Hier sind z.B. die technischen Werte wie Spannung oder Anzahl von Eingängen einer SPS wichtige Informationen. Ist das Gerät ermittelt, wird es im nächsten Prozessschritt im Schaltplan projektiert. Für den späteren Montageaufbau sind z.B. 3D-Informationen sehr wichtig. Aus dem entstehenden digitalen Zwilling können automatisiert Maschinen angesteuert werden, die die Löcher in die Montageplatte bringen, um die Komponente dann auch an der richtigen Position festzuschrauben. Hier sind fertigungsrelevante Daten wie Bohrbilder von essentieller Bedeutung. Zudem ist es möglich, die nötige Klimatisierung zu berechnen, wenn wir vorab wissen und digital sehen können, welche Komponenten wo im Schrank verbaut sind. Die automatisierte Fertigung ist also der abschließende Schritt, der mit umfassenden Gerätedaten effizienter gestaltet wird. Über die bereits beschriebenen Prozessschritte inklusive der Bestellung von Komponenten (Stichwort kaufmännische Informationen) hinaus können Unternehmen allerdings auch angrenzende Prozesse mit den Gerätedaten bedienen. Die Berechnung des Gewichts eines Schaltschranks ist ein Beispiel, um diesen geeignet transportieren zu können.
Der Kunde im Zentrum
Aus den beschriebenen Prozessschritten erkennt man die Notwendigkeit der Standardisierung auf Geräteebene und deren Verarbeitung in den jeweiligen Systemen. Bisher gab es zwar eine Beschreibung der Gerätedaten und das jeweilige Datenformat, aber es fehlte vielfach der Bezug zur Praxis. Hierzu wurden in Workshops gemeinsam mit Key-Playern im Schaltanlagenbau die wichtigsten Prozessschritte und die entsprechend relevanten Daten definiert und in einem zweiten Schritt mit den Herstellern abgeglichen. Andreas Ripploh, Geschäftsführer bei Ripploh Elektrotechnik, hat seine Ideen in die Entwicklung eingebracht. Für ihn ist ein Datenstandard ein absolutes Muss: „Wir müssen etwa für das Routing genau wissen, wo die Anschlusskoordinaten sind, wie viele davon ein Bauteil hat und mit welchen Aderquerschnitten wir in ein Bauteil hineingehen.“ Um teil- oder vollautomatisiert einen Schaltschrank zu bauen, sind eineindeutige Komponentendaten die Voraussetzung. Dazu bedarf es einer klaren Struktur, die z.B. definiert, wie ein Zahlenwert abgelegt wird. Die internationale Artikelnummer im Eplan Data Portal ist ein solch eineindeutiger Wert, der auch direkt in die Stückliste einfließt.“ Eplan und Rittal positionieren sich in diesem Fall als Sparringspartner. Sie greifen die Anforderungen von Kunden auf und setzen diese gemeinsam mit Herstellern um. Der Eplan Data Standard dient als Leitfaden, welche Felder innerhalb von Eplan wie zu füllen sind. Damit das möglichst effizient und ohne Mehraufwände für Hersteller gelingt, ist in einem ersten Schritt ein Service in Arbeit, der das Mapping zwischen eCl@ss Advanced und Eplan ermöglicht. Somit werden die Anforderungen der Praxis in Bezug auf Datentiefe und Qualität der Gerätedaten umgesetzt. Konkret: Kunden werden in die Lage versetzt, die existierenden Standards entlang der Wertschöpfungskette mit dem größtmöglichen Nutzen einzusetzen.