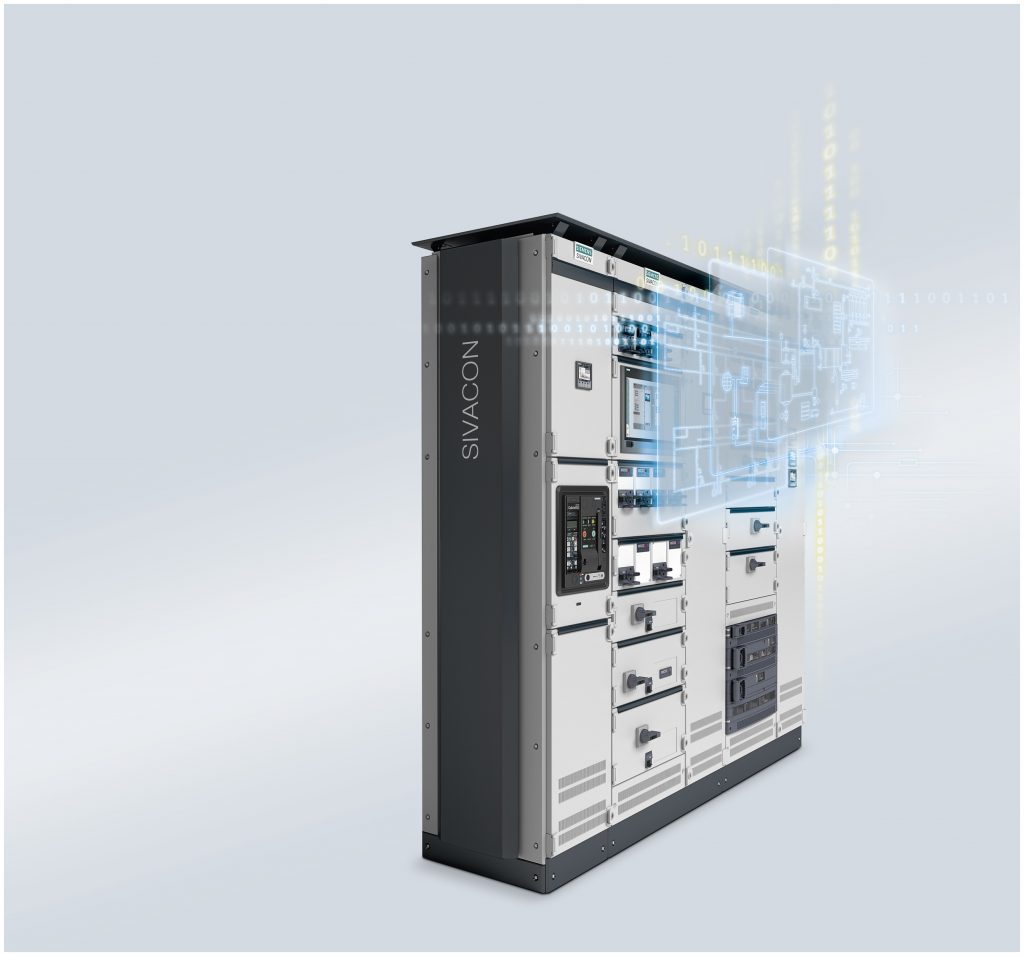
Mit der Baureihe Sivacon S8 hat Siemens ein Niederspannungs-Schaltanlagenprogramm entwickelt, das in zahlreichen Infrastrukturprojekten des Konzerns zum Einsatz kommt. Typische Anwendungsfälle sind neben Energieverteilungen in Rechenzentren vor allem Motor-Control-Center in der Kraftwerkstechnik, der Prozess-, Öl- sowie Gasindustrie. Entsprechend groß ist die Vielfalt an Applikationen und Anforderungen. Der Hauptsitz für die Planung und den Bau der Schaltanlagen befindet sich in Leipzig und ist Teil des Geschäftsbereichs Smart Infrastructure – Distribution Systems. „Unsere Vertragspartner kommen meist aus dem Siemens-Verbund, die Lieferungen gehen aber zum Großteil an externe Kunden“, erklärt Michel Strusch, Head of Electrical Engineering am Standort Leipzig. Man könne davon ausgehen, dass nahezu 80 Prozent der gebauten Anlagen außerhalb Deutschlands installiert sind.
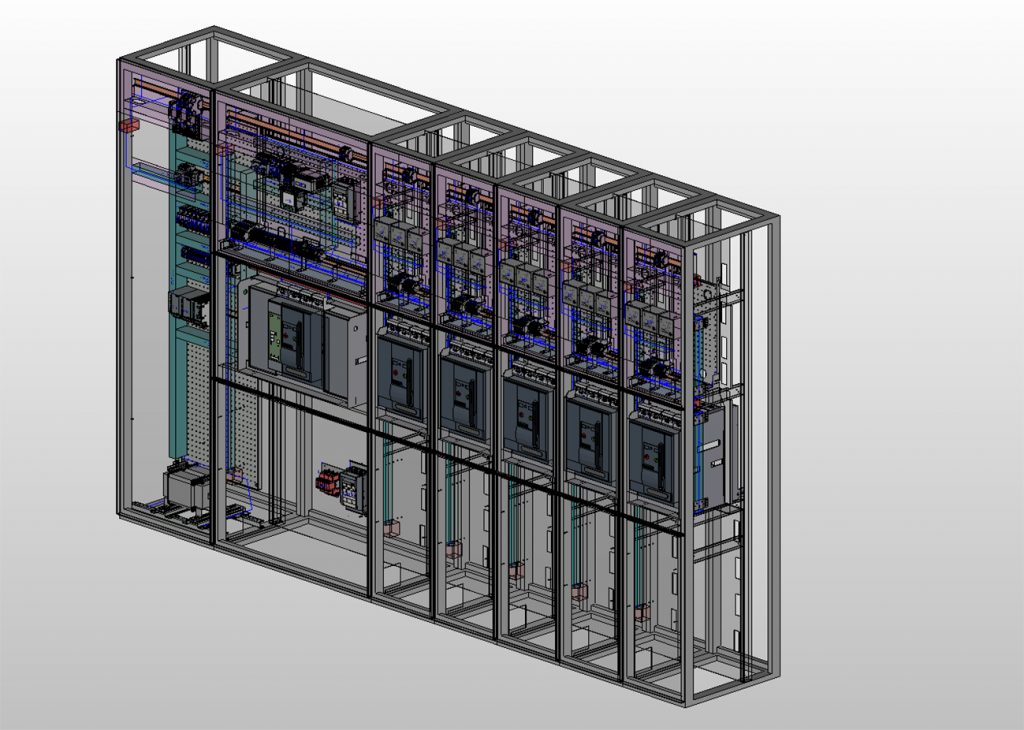
Schaltschrankplanung in Losgröße Eins
Die Schaltanlagen, die in Leipzig entstehen, haben in der Mehrzahl fünf bis 25 Felder mit Breiten von 400 bis 1.200mm. Aber auch Projekte mit mehr als 1000 Feldern wurden schon realisiert. Meist handelt es sich um Sonderanlagen in Losgröße Eins. „Jedes Projekt hat seine eigenen Anforderungen, der Wiederholgrad ist sehr niedrig und die Varianz steigt mit jedem neuen Projekt weiter“, fährt Strusch fort. Umso wichtiger sei aus Sicht von Siemens eine Standardisierung. Deshalb wurde schon vor Jahren ein Konfigurator für Sivacon S8 entwickelt. Das erleichtert und beschleunigt die Projektierung erheblich, weil die Entwickler bei ihrer Arbeit auf bauartgeprüfte Funktionsmodule zurückgreifen können. Allerdings gilt bzw. galt diese Standardisierung nur für die Hauptstromkreise, also die Energiekreise. Die Hauptaufgabe für die Elektrokonstrukteure bestand somit darin, die Sekundär- und Steuerstromkreise zu planen.

Standardisierung der Sekundärstromkreise
Im nächsten Schritt sollte die Standardisierung auf diese Stromkreise erweitert werden. Benjamin Herold, als technischer Koordinator verantwortlich für das Projekt: „Im Electrical Engineering arbeiten wir schon seit 2008 mit Eplan.“ Deshalb lag es nahe, auch die Automatisierung der Schaltplanerstellung auf der Eplan Plattform zu vollziehen. Dabei gingen die Verantwortlichen in Leipzig systematisch vor. In Zusammenarbeit mit einem Berater von Eplan erarbeiteten sie 2017 die Grundlagen für die automatisierte Schaltplanerstellung mit Eplan Cogineer. „Wir haben die einzelnen Funktionen und Bausteine in den Steuerstromkreisen zunächst bis auf die unterste Ebene zerlegt“, erzählt Herold. „Dann haben wir diese Bausteine so strukturiert und zusammengefasst, dass sie bestmöglich nutzbare Einheiten bilden.“
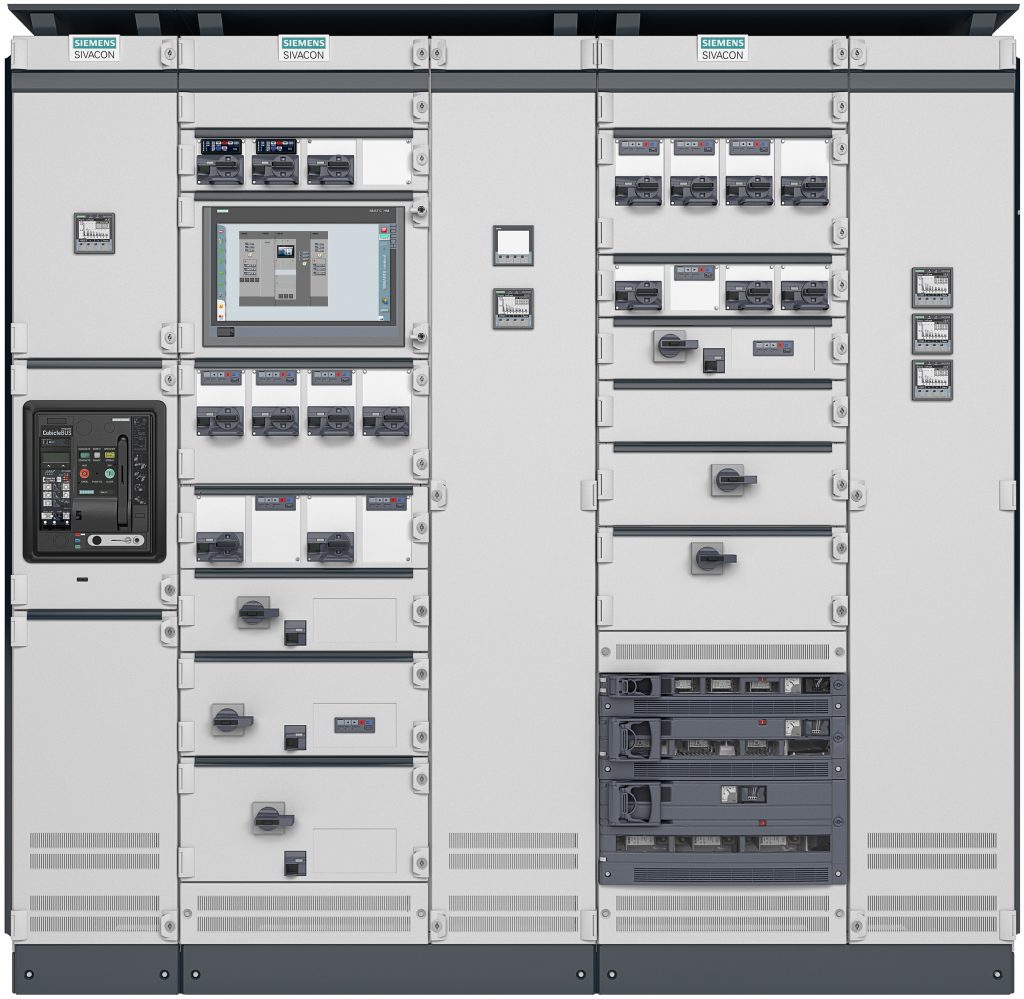
Automatisierte Schaltplanerstellung
Damit haben die Elektrokonstrukteure in Leipzig eine gute und praktikable Grundlage für die Projektierung des Steuerstromkreises geschaffen. „Eplan Cogineer ist intuitiv benutzbar“, so Herold weiter. „Der Elektrokonstrukteur wählt die Geräte bzw. Funktionen aus und der Schaltplan entsteht zu großen Teilen von selbst.“ Das spart Zeit, bietet aber auch noch weitere Vorteile – z.B. eine stärkere Standardisierung. „Bisher war das Layout der Schaltanlagen immer auch vom Projektanten und Elektrokonstrukteur abhängig“, ergänzt Strusch. „Das kann bei Kunden, die regelmäßig Schaltanlagen von uns beziehen, durchaus für Irritationen sorgen. Mit Cogineer befinden sich etwa der Motorschutzschalter oder der Sicherungsautomat immer an derselben Stelle.“ Ebenfalls vorteilhaft ist die Tatsache, dass dieses Tool zur automatischen Schaltplangenerierung schnell um neue Funktionen ergänzt werden kann.
Weniger Fehler im Engineering
Außerdem führt die Nutzung von Cogineer zu verringerter Lagerhaltung, weil stets die gleichen Geräte für ein und dieselbe Aufgabe ausgewählt werden. Fehler treten seltener auf, weil die Funktionsmodule getestet sind. Neue Mitarbeiter können sich zudem schneller einarbeiten. „Sie können dann bei einem Projekt wirklich mit einem leeren Blatt anfangen, müssen sich nicht damit auseinandersetzen, wie bei uns ein Stromlaufplan aussieht und sind sehr schnell produktiv“, so Strusch. Inzwischen nutzen zwölf der 18 Elektrokonstrukteure im Siemens-Werk den Konfigurator. Florian Pusch entwickelt als Designer im Team neben seiner Rolle als Projektleiter für die automatische Stromlaufplanerstellung neue Standardfunktionen und implementiert sie in Cogineer. Die Elektrokonstrukteure sind dabei aufgefordert, Vorschläge zu unterbreiten. Aktuell sind schon 50 konfigurierbare Funktionen mit rund 1.000 Artikeln in Cogineer hinterlegt. Generell war das Ziel bei der Einführung des Tools, so viel Wissen aus Projektierung und Fertigung wie möglich in das System zu verlagern und dort abzubilden. „Die Kollegen haben genau erklärt, wie sie Stromlaufpläne erstellen, wie ein Feld bestückt wird und welche Funktionen miteinander kombinierbar sind“, sagt Pusch. „Dieses Knowhow ist in der Software hinterlegt und kommt bei jedem einzelnen Projekt zur Anwendung.“
Durchgängige Prozesskette
Zeitgleich mit der Einführung von Cogineer hat Siemens in Leipzig die dreidimensionale Schaltschrankplanung Eplan Pro Panel eingeführt. Für dieses Projekt ist Tobias Isensee mitverantwortlich. Er sieht deutliche Vorteile in der parallelen Einführung der beiden Softwaremodule: „Die Arbeitsweise in Cogineer, z.B. das Setzen von Verbindungs-Definitionspunkten, hatte zur Folge, dass wir Pro Panel innerhalb kurzer Zeit nutzen konnten und jetzt mit einer durchgängigen Prozesskette der Elektroplanung arbeiten.“ Das verbessert etwa die (externe) Kabelkonfektionierung. „Hier haben wir sehr spezielle Anforderungen und nutzen sehr viele Querschnitte und Farben“, betont Isensee. „Das lässt sich in Pro Panel gut abbilden. Und das automatisierte Routing steigert die Qualität und sorgt für ein einheitliches Bild in den Schaltschränken.“ Für die mechanischen Bauteile hat Siemens in Pro Panel ebenfalls Standards festgelegt: „Die Montageplatten sind standardmäßig mit Kabelkanälen und Hutschienen bestückt, die Elektrokonstrukteure können dadurch die Geräte passend und nach internen Vorgaben platzieren, die gemeinsam mit der Fertigung entwickelt wurden.“ Auch die Berechnung des Kabelkanalfüllgrades und Kollisionsprüfung sind aus Sicht von Siemens praktische Hilfsmittel, und bei der Gerätebestellung z.B. von Klemmen vereinfacht sich durch Pro Panel ebenfalls der Aufwand.
Zeit und Kosten sparen
Die Siemens-Ingenieure bewerten die Relation von Aufwand und Einsparung sowohl bei den Kosten als auch bei der Durchlaufzeit sehr genau. „Aktuell haben wir bei der Planung teilweise noch höheren Aufwand“, erklärt Strusch. „Das liegt am höheren Detaillierungsgrad der Elektrokonstruktion. Früher waren wir manchmal mit dem Stromlaufplan schneller fertig. Da hilft uns aber jetzt die Software Cogineer. Sie gibt uns Zeit zurück.“ Beim Verdrahten verkürze sich der Aufwand deutlich: „Weil der Monteur fertig beschriftete und konfektionierte Leitungen erhält, sparen wir hier teilweise bis zu 40 Prozent Zeit. Die veredelten Leitungen sind zwar etwas teurer, aber unterm Strich sparen wir deutlich. Auch fehlerbedingte Mehrkosten reduzieren sich, weil sich aufgrund des Routings Qualitätsverbesserungen ergeben.“
Kontinuierliche Selbstoptimierung
Bei Siemens sieht man die Einführung von Pro Panel und Cogineer als laufenden Prozess, der im Sinne der kontinuierlichen Verbesserung noch nicht beendet ist. „Wir stellen monatlich ein neues Cogineer-Release zur Verfügung, in das auch Feedbacks aus dem Engineering oder geänderte Gerätedaten einfließen“, führt Pusch weiter aus. „Wir pflegen diese Änderungen dann zentral ein und profitieren davon, dass wir nicht 50 Makros ändern oder anpassen müssen. Wenn wir aus der Fertigung die Information erhalten, dass eine Vorgabe nicht umgesetzt werden konnte, passen wir das direkt in Cogineer an.“
Warten auf die Cloud
Auf der Agenda bei Siemens in Leipzig steht auch die Nutzung von ePulse, der cloud-basierten Plattform für die Elektrokonstruktion. Sie soll die Zusammenarbeit und den Zugang zu allen Projekten ermöglichen. „Wir arbeiten eng mit unseren Schwesterwerken in anderen Ländern zusammen, u.a. in Portugal, China oder der Türkei“, so Strusch. „Oft übernehmen wir hier die Planung und Teile des Engineerings für Anlagen, welche in diesen Werken gefertigt werden. Die Vereinheitlichung durch Eplan hat uns hier schon sehr viel weitergebracht. Wenn wir uns nun auf einer gemeinsamen Konstruktionsplattform verbinden könnten, wäre das ein weiterer Schritt in Richtung Standardisierung und standortübergreifender Kollaboration.“